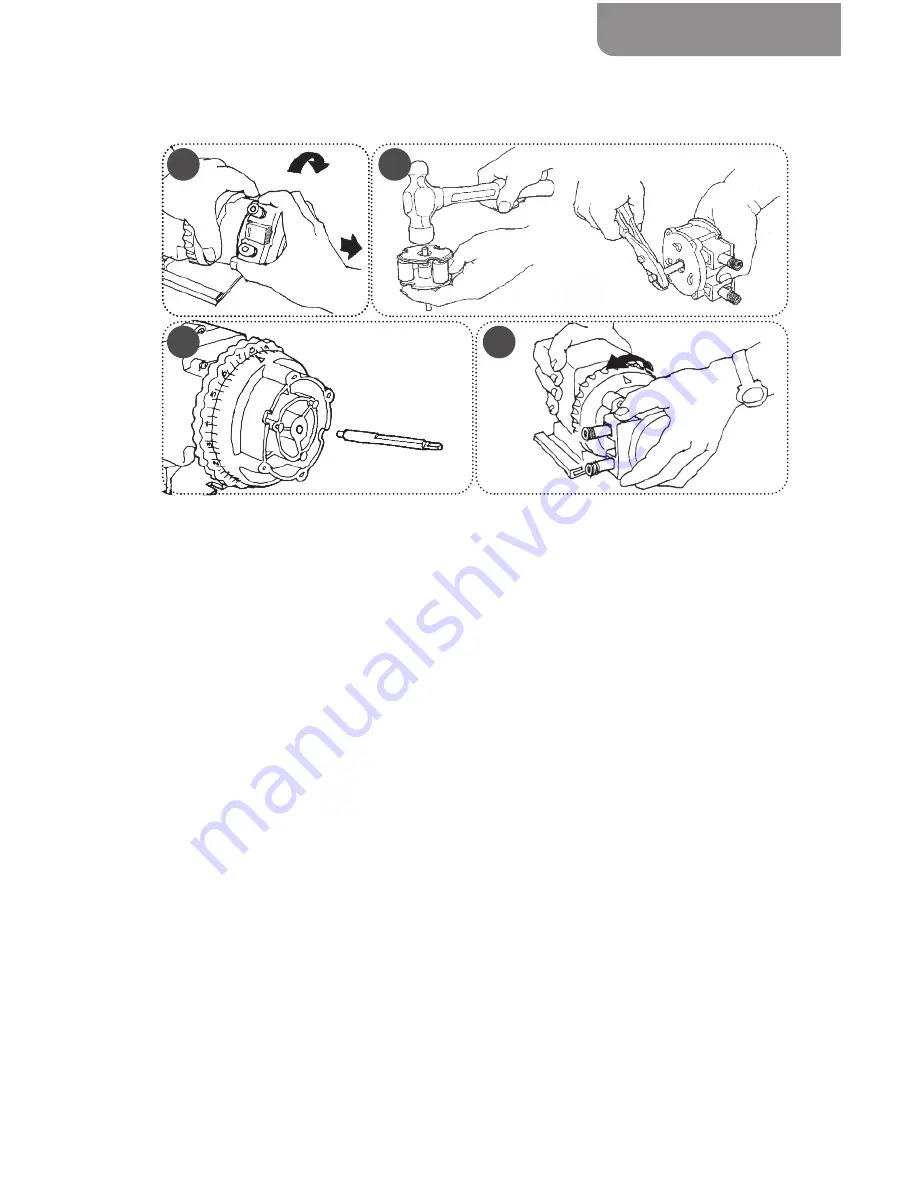
31
PUMP HEAD
PUMP HEAD REPLACEMENT
ADJUSTABLE MODEL
REMOVE PUMP HEAD & INSTALL QuickPro
®
PUMP HEAD
1.
Turn off the pump and unplug the power cord.
a.
To remove the pump head, hold the feed rate securely, grasp the head and
turn it clockwise until it stops.
Figure A
b.
Remove the head by pulling it straight out from the pump. The main shaft will
come out with the pump head.
c.
Using a pair of pliers, grasp the main shaft and rock it back and forth
(clockwise and counter-clockwise) while pulling it straight out of the pump
head. Set aside the shaft to be reinstalled later. Discard the old tube, housing
and cover. If the shaft will not come out, remove the cover from the pump head
and use a hammer to tap the shaft from the front of the roller assembly to
dislodge it.
Figure B
d.
Insert the shaft back into the feed rate control.
Figure C
e.
Put the new pump head onto the feed rate control and turn it counter-clockwise
until the shaft falls into place.
2.
Push the pump head in while turning it counter-clockwise. Line up the rivet holes on
the pump head with the rivets on the feed rate control (adjustable pump) OR motor
(fixed output pump).
Figure D
3.
Continue to push until the rivets are inside the holes.
4.
Turn the pump head counter-clockwise to secure the rivets in the rivet slots, firmly
attaching the pump head. Proceed to page 33.
USA and Canada 800.683.2378, International 904.641.1666.
A
B
C
D