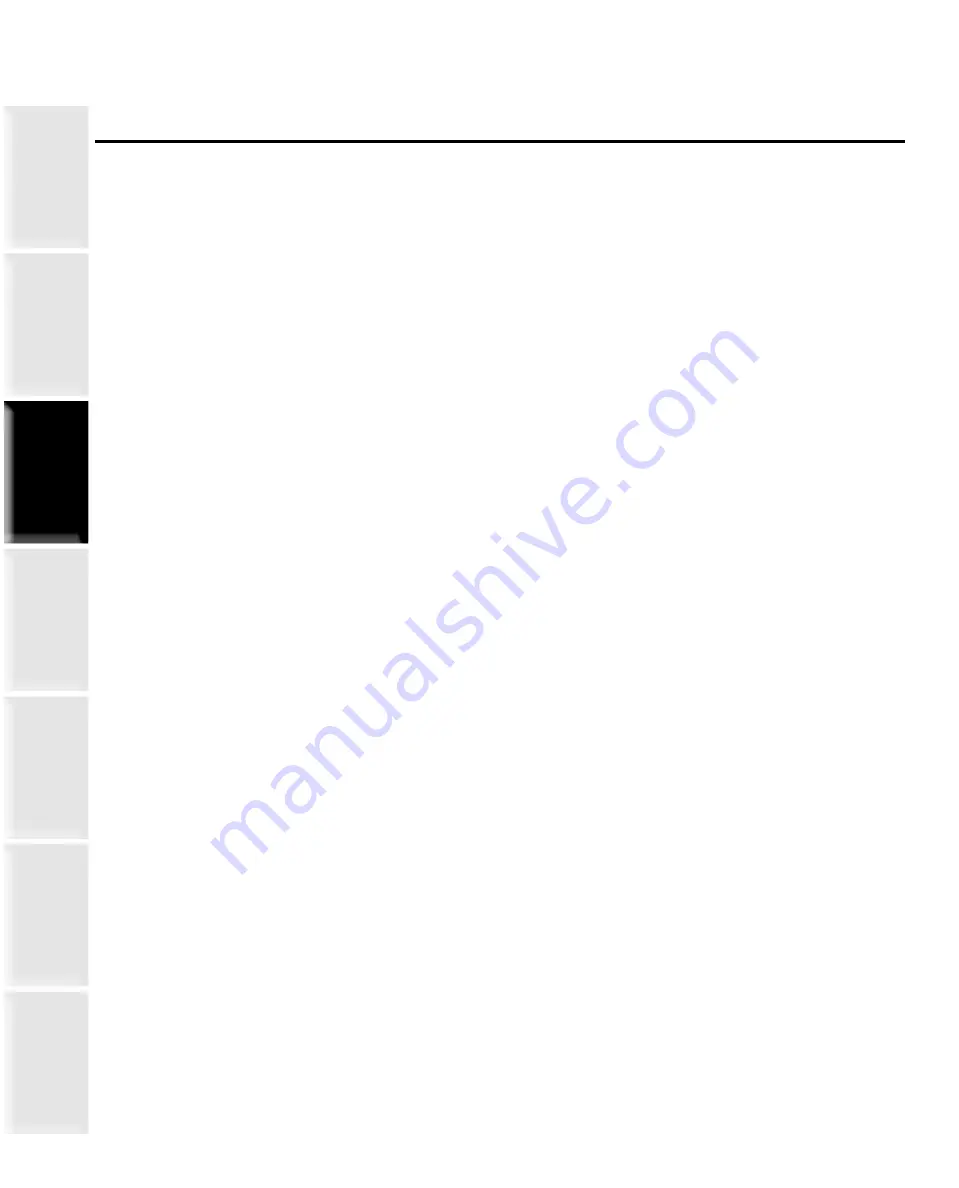
© 2022 Staheli West
86
Judging Bale Moisture with a
Handheld Moisture Probe
•
Hay with Stem Moisture: When baling hay with stem moisture, a handheld “contact type”
moisture sensor is not accurate when baling and will normally read lower than the actual
moisture content of the hay.
▫
A stem of hay that is not fully cured may be relatively dry on the outside but green on the
inside. Therefore, while the inside of the stem may be very conductive, the conductivity
between stems is typically much lower. This insulates the signal between the measuring
points on the sensor, resulting in a lower overall reading at the time of baling. Moisture
readings with a handheld probe a few days after baling will be higher when the moisture
from the stems migrates more fully throughout the bale profile.
•
This type of moisture probe is effective several hours after the hay has been baled, as the
applied moisture diffuses throughout the plant tissue more completely.