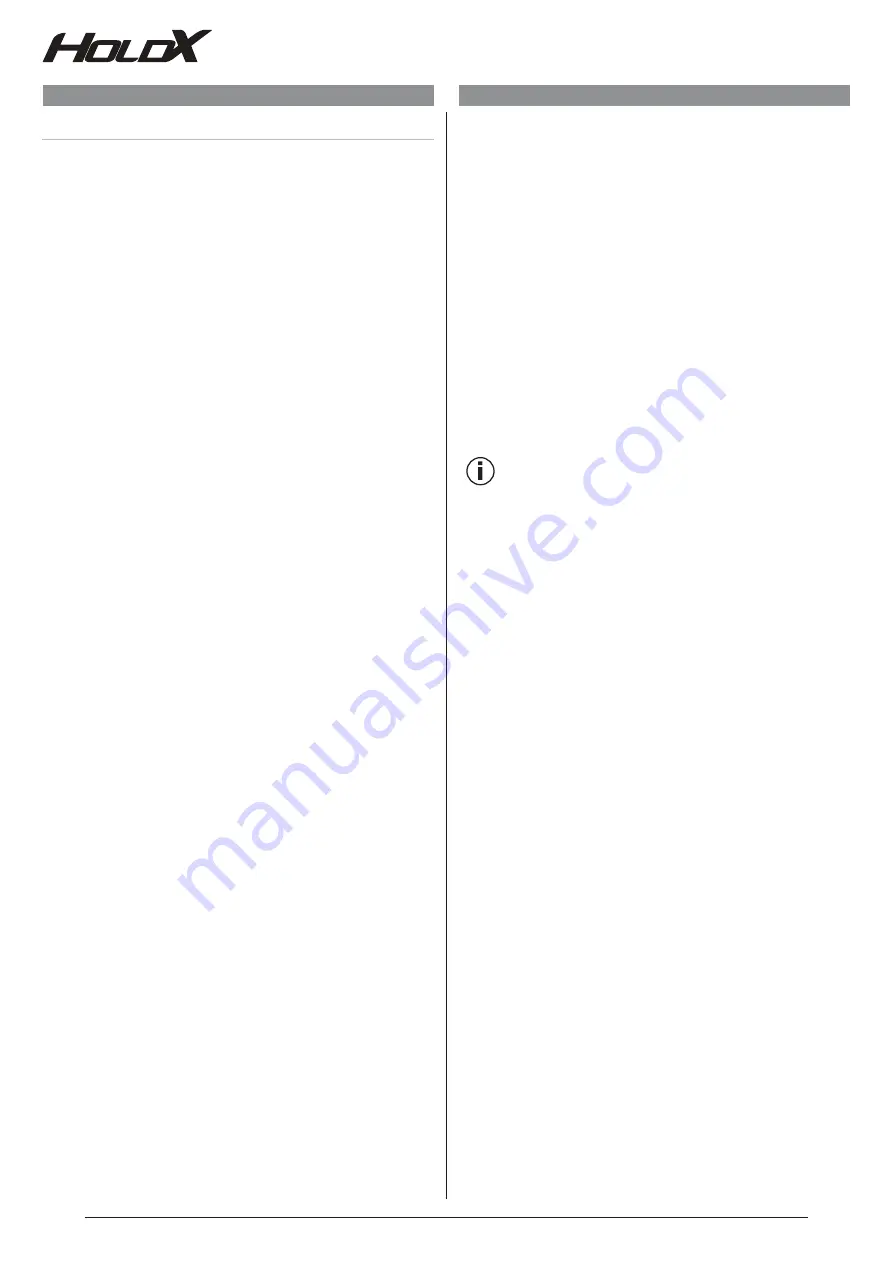
34
EN
5 . Inputs and outputs function
5 .1 Mode of operation of the safety outputs
The process lock with safety function has 2 short-circuit-proof safety outputs (OSSD) Pin 2
(X1) and Pin 4 (X1). The safety outputs switch on under the following conditions:
• The correct anchor plate is detected in the detection zone (protective device closed).
• A high signal is present at both safety inputs Safety IN Pin 2 (X2) and Pin 4 (X2).
• No error is detected.
The process lock with safety function switches off the OSSD outputs under the following
conditions:
• There is no or the incorrect anchor plate in the detection zone
• A low signal is present at one of the two inputs
• An error is detected (not all errors switch off the OSSD outputs)
The two safety outputs can be connected to the inputs of a safety controller under the
following conditions:
• The input must be suitable for clocked safety signals (OSSD signals); the control unit must
tolerate test pulses on the input signals with a length of up to 0.3 ms, see Section 2.8
Technical data. Please observe the instructions of the control unit manufacturer. Wiring
examples can be found in Section 10.1.
The current status of the safety outputs can be checked at any time via the optional built-in
Bluetooth - interface and the "HOLDX-Manager" software.
5 .2 Safety inputs
The process lock with safety function has 2 safety inputs Safety IN Pin 2 (X2) and Pin 4 (X2).
• If the process lock is used individually, the safety inputs must be connected to +24 VDC.
• When using the process lock in a series connection, the safety inputs of the first slave
is connected to X2 to +24 VDC via the Termination Plug SP-X-71-002-06 on X2 - the
safety inputs of the following process lock are connected to the safety outputs of the
preceding HOLDX. Please also refer to Section 2.6 – Series connection
• Pulses with a duration of max. 900 μs are tolerated at the safety inputs. Wiring examples
can be found in Section 10.1.
The current status of the safety inputs can be checked at any time via the optional built-in
Bluetooth - interface and the "HOLDX-Manager" software.
5 .3 EDM + Reset input,
only for version HOLDX-Master RL2-CS-12P-_-B
Monitored EDM + Reset input
Connect an external reset button of your machine control to the EDM + Reset input PIN
9 (X1). The reset input is only recognized as correctly set if at least one valid start pulse is
detected after the sensor has been actuated and the safety inputs have been set. The valid
start pulse is detected if a falling edge is detected after a rising edge within the permissible
start pulse duration of between 30 ms and 5 s. Examples can be found in Section 10.1.
5 .4 Serial outputs
The master HOLDX RL2 sends all diagnostic signals of every single participant via the
serial outputs Serial OUT Pin 7 (X1) and Pin 8 (X1) to a superior control system. Diagnosis
information is e.g. door status (door open/closed), locking status (door locked/unlocked)
and error message of the individual participants. Refer to Section 6 for further diagnosis
information. – Operating states and diagnosis.
The current diagnosis information, states of the HOLDX process locks, as well as the individual
configurations can be checked or configured at any time via the optionally built-in Bluetooth
interface and the "HOLDX-Manager” software.
For optimal communication to the standard PLC, the speed (baud rate) of the serial output
can be adjusted via the integrated Bluetooth interface and the "HOLDX-Manager” software.
Factory setting for the serial output
Data pulse width: 60 ms
Clock pulse width: 30 ms
Note
The diagnosis output is not a safety-related output
You can find the software function blocks (Software-Gateways) for various
PLC systems under
www.safety products.de.