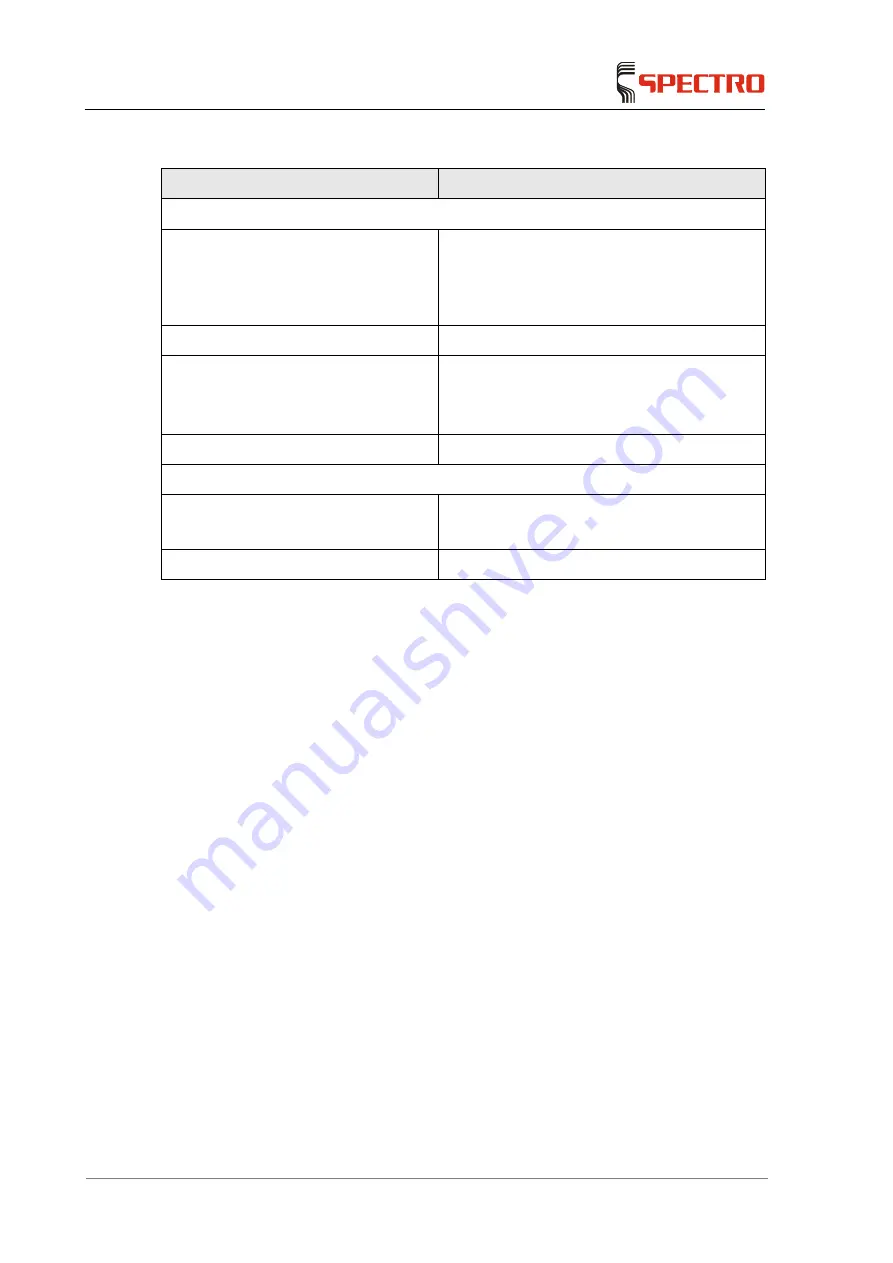
Technical data
— 16
SPECTRO GENESIS FES 27 — 17.07.2019
Description
Value
Argon gas connection
Inlet pressure during operation
6–8 bar (87–116 psi)
7 bar (101 psi) recommended
A maximum Ar inlet pressure of 8 bar (116 psi)
must not be exceeded.
Quality
≥ 4.6 (99.996 %)
Optical system gas flushing rate
0 L/min (off)
0.5 L/min (low)
1 L/min (high)
Plasma gas consumption
≤ 25 L/min
Extraction (continuous)
Plasma torch box
Depending on the ambient temperature
100 – 140 m³/h; 59 – 82 ft³/min
Generator
250—300 m³/h; 150–177 CFM
Summary of Contents for FES 27
Page 2: ......