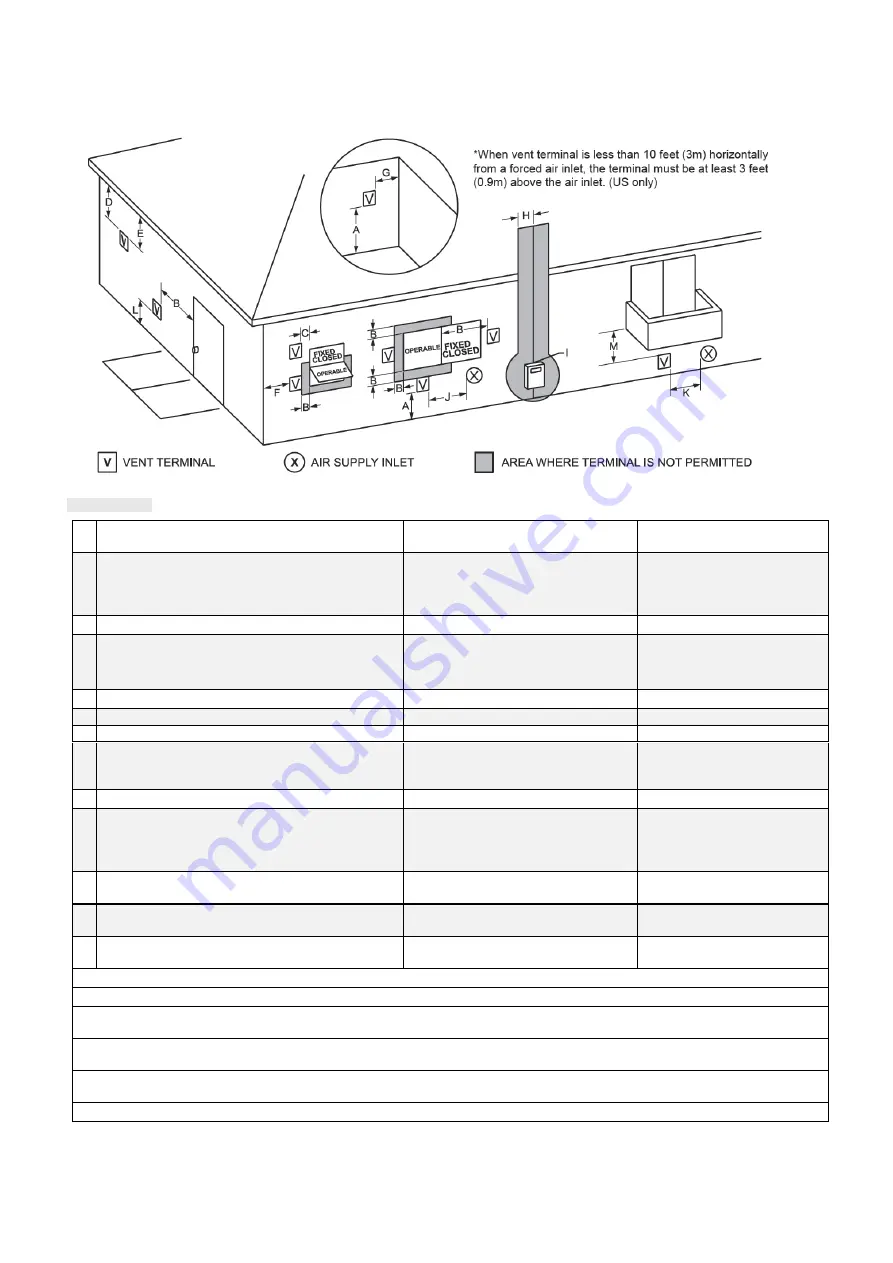
68
E93.1901EN032 Installation and Service Manual SlantFin VGH-CH / CO
5. Maintain clearances as stated in this manual. Also maintain the following:
6. Locate terminations so they are not likely to be damaged by foreign objects, such as stones or balls, or
subject to buildup of leaves or sediment.
Figure 9.14
A Clearance above grade, veranda, porch, deck, or
balcony
12" (30 cm)
see note 3
12" (30 cm)
see note 3
B Clearance to window or door that may be opened
Direct vent only: 12" (30 cm)
Non-Direct vent: 4 ft (1.2 m) below or
to side of opening; 1 ft (30 cm) above
opening
36 inches (91 cm)
C Clearance to permanently closed window
see note 4
see note 5
D Vertical clearance to ventilated soffit located
above the terminal within a horizontal distance of
2 ft (61 cm) from the center line of the terminal
see note 4
see note 5
E Clearance to unventilated soffit
see note 4
see note 5
F Clearance to outside corner
see note 4
see note 5
G Clearance to inside corner
see note 4
see note 5
H Clearance to each side of center line extended
above meter/regulator assembly
see note 4
3 ft (91 cm) within a height of
15 ft above the
meter/regulator assembly
I
Clearance to service regulator vent outlet
see note 4
3 ft (91 cm)
J
Clearance to nonmechanical air supply inlet to
building or the combustion air inlet to any other
appliance
Direct vent only: 12” (30 cm);
Non-Direct vent: 4 ft (1.2 m) below or
to side of opening; 1 ft (30 cm) above
opening
3 ft (91 cm)
K Clearance to a mechanical air supply inlet
3 ft (91 cm) above if within 10 ft (3 m)
horizontally
6 ft (1.83 m)
L Clearance above paved sidewalk or paved
driveway located on public property
Vent termination not allowed.
7 ft (2.1 m)
M Clearance under veranda, porch, deck, or
balcony
see note 4
12" (30 cm) see note 6
note 1: In accordance with the current ANSI Z223.1 / NFPA 54 National Fuel Gas Code
note 2: In accordance with the current CAN/CSA-B149.1 Installation Codes
note 3: Maintain 12” of clearance above the highest anticipated snow level or grade or, whichever is greater. Please refer to
your local codes for the snow level in your area
note 4: For clearances not specified in ANSI Z223.1 / NFPA 54, clearance is in accordance with local installation codes and
the requirements of the gas supplier.
note 5: For clearances not specified in CAN/CSA-B149, clearance is in accordance with local installation codes and the
requirements of the gas supplier
note 6: Permitted only if veranda, porch, deck, or balcony is fully open on a minimum of two sides beneath the floor.
Summary of Contents for VHG-100-CH
Page 2: ......
Page 8: ...8 E93 1901EN032 Installation and Service Manual SlantFin VGH CH CO 1 SAFETY GUIDELINES...
Page 9: ...E93 1901EN032 Installation and Service Manual SlantFin VGH CH CO 9 CONSIGNES DE S CURIT...
Page 83: ...E93 1901EN032 Installation and Service Manual SlantFin VGH CH CO 83 Figure 10 5...
Page 85: ...E93 1901EN032 Installation and Service Manual SlantFin VGH CH CO 85 Figure 10 7...
Page 162: ......
Page 163: ......