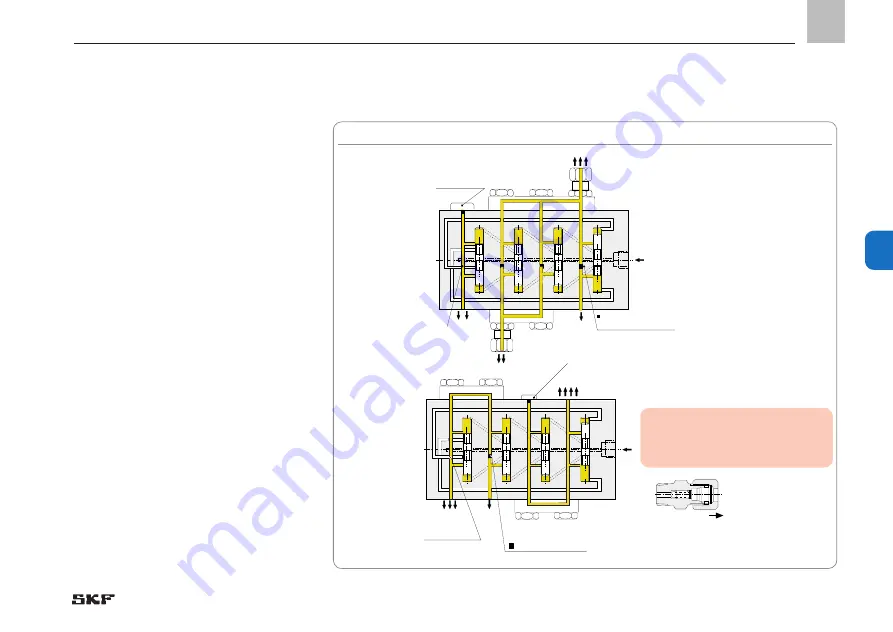
6
EN
6. Assembly
- 75 -
951-180-083-EN
Version 02
6.5.8 Consolidation of multiple outlets on the VPB (crossporting)
3
1
2 7
4
8
5
1
7
5
6
6
3
4
2
8
4
3
2 7
1
4
5
1
7
5 6
6
3
4
2
8
8
Plug screw 466-431-001
Plug
917-006-101 removed
Plug 917-006-101 (hexagon socket WAF 3)
Plug screw 466-431-001
Plug 917-006-101 (hexagon socket WAF 3)
Plug
917-006-101 removed
Note!
Use only a fitting with check valve
(VPKM-RV-S4) on the metering
device outlet.
-See Figures 30 to 32
It is possible to subsequently connect two
opposite outlets internally by removing a
plug from the right outlet borehole and
closing one of the two outlets.
Fig. 30
VPB functional diagram of bridge designs (crossporting)
Summary of Contents for LINCOLN VP Series
Page 115: ...115 951 180 083 EN Version 02 Notes...
Page 117: ......