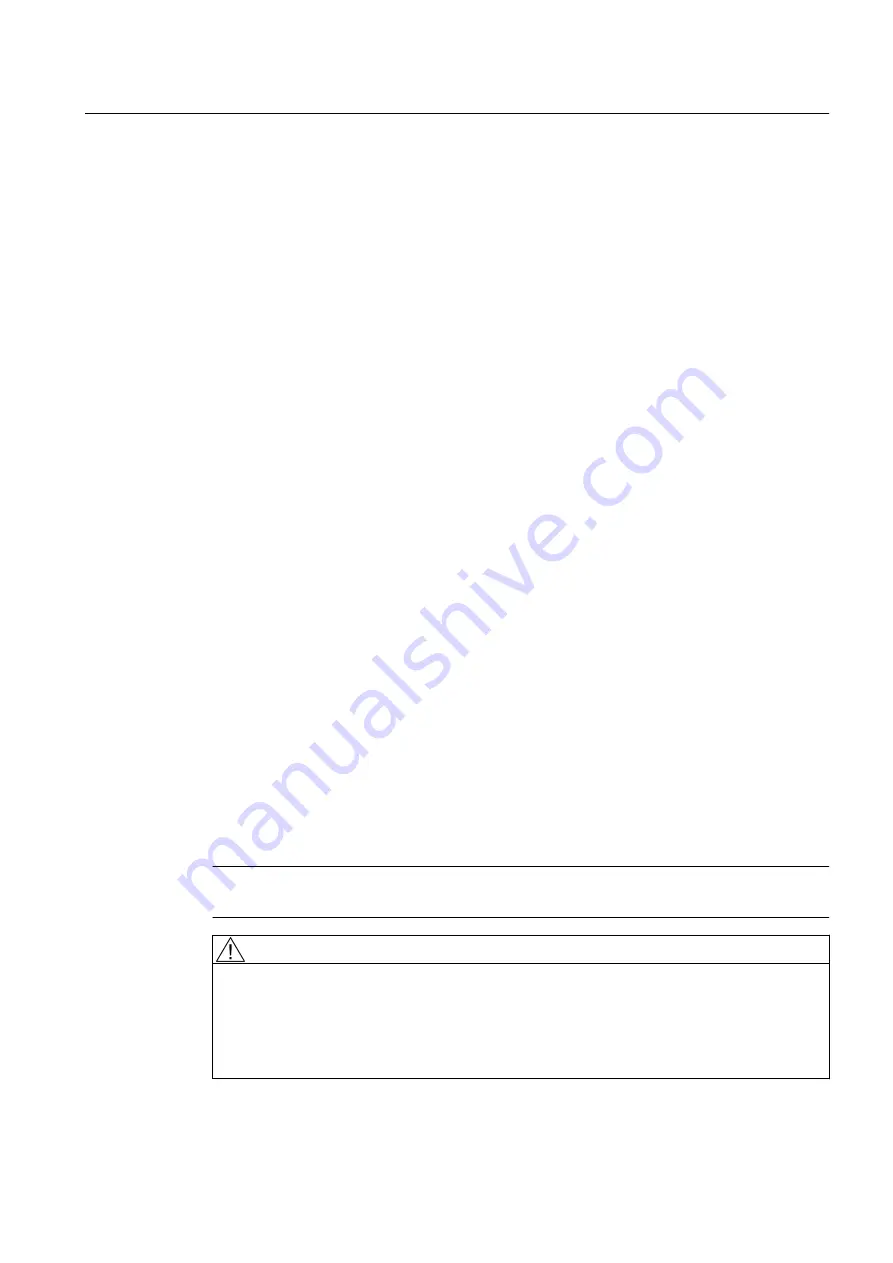
Operate the machine in continuous operation in Zone A. Prolonged operation in Zone B is not
recommended:
● Exceeding the permissible tolerances for voltage and frequency can lead to an
impermissibly high temperature rise of the winding. This can result in long-term damage to
the winding.
● Limit exceptions of this sort with regard to the values that arise, how often, and for how long
they occur.
● Where possible and within a reasonable time take corrective actions such as reducing the
power. In this way you can avoid that the service life of the machine is reduced as a result
of thermal aging.
4.14
Phase synchronization during supply system switching
Damage to the machine may be caused when switching to another supply system with different
phasing.
● The phasing must be synchronized during switching. Use appropriate means to
synchronize the phasing.
4.15
System-inherent frequencies
Excessively high vibration levels and system resonances can damage the machine set.
● Configure and match the system consisting of the foundation and machine set in such a way
that no system resonances can arise and result in the permissible vibration levels being
exceeded.
● The vibration values according to DIN ISO 10816-3 must not be exceeded.
4.16
Torsional load of the drive train
In the event of faults in the electrical connection during operation, excessive air gap torques can
lead to additional mechanical torsional load on the line shaft.
Note
The system planner is responsible for the entire drive train.
WARNING
Torsional loadings of the shaft assembly
If the configuration does not correctly recognize the mechanical torsional loadings of the shaft
assembly, this can lead to serious damage to the machine. This can result in death, serious
injury or material damage.
When planning the system, consider the configuration data.
Preparations for use
4.14 Phase synchronization during supply system switching
SIMOTICS FD 1LH1
Operating Instructions 01/2019
39
Summary of Contents for SIMOTICS FD 1LH1
Page 2: ...23 01 2019 19 26 V11 01 ...
Page 28: ...Description SIMOTICS FD 1LH1 28 Operating Instructions 01 2019 ...
Page 122: ...Operation 8 10 faults SIMOTICS FD 1LH1 122 Operating Instructions 01 2019 ...
Page 140: ...Maintenance 9 2 Corrective Maintenance SIMOTICS FD 1LH1 140 Operating Instructions 01 2019 ...
Page 162: ...Disposal 11 5 Disposal of components SIMOTICS FD 1LH1 162 Operating Instructions 01 2019 ...
Page 164: ...Service and Support SIMOTICS FD 1LH1 164 Operating Instructions 01 2019 ...
Page 168: ...Quality documents SIMOTICS FD 1LH1 168 Operating Instructions 01 2019 ...
Page 173: ......