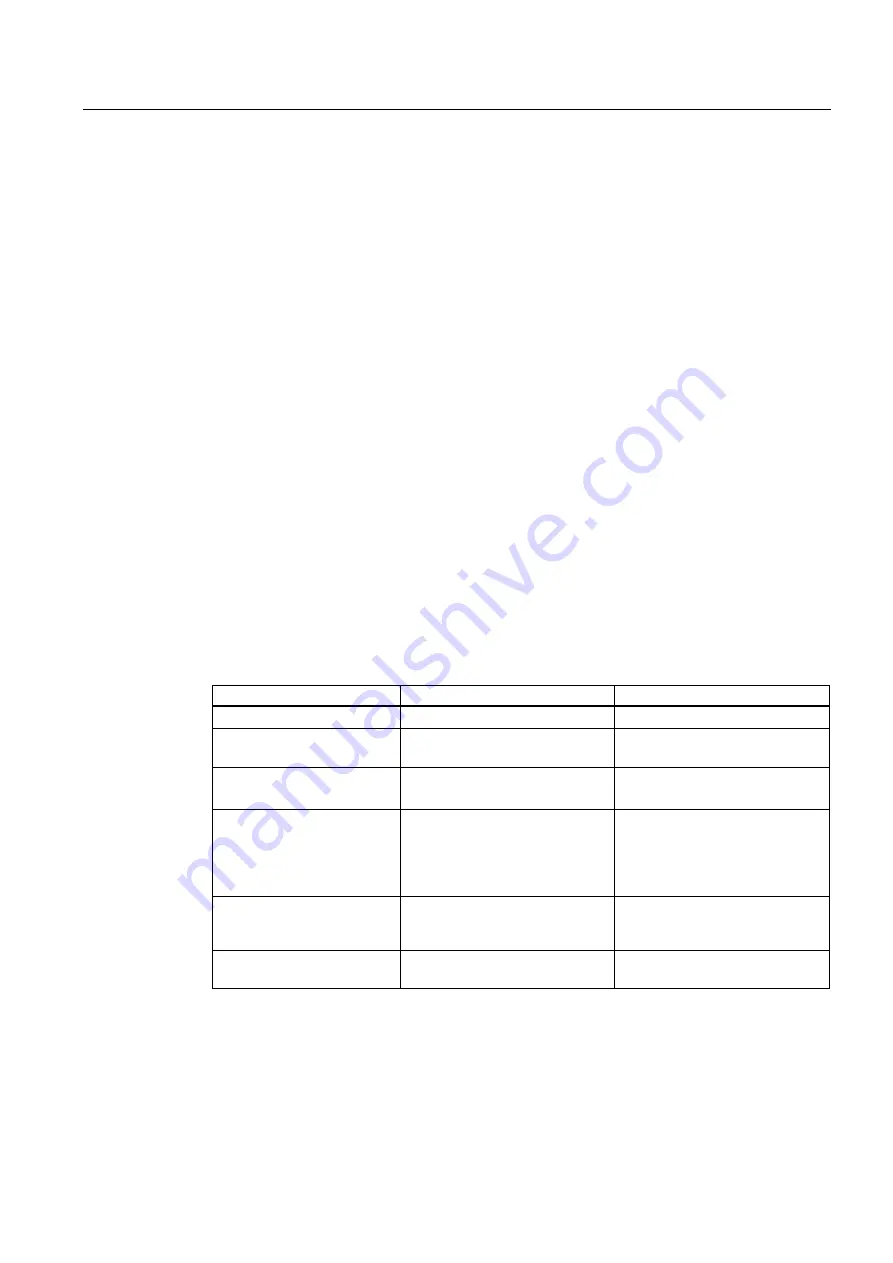
Overview of Fail-safe Systems
1.3 Fail-safe Systems in SIMATIC S7
Safety Engineering in SIMATIC S7
System Manual, 04/2006, A5E00109529-05
1-7
1.3.2
Performance Characteristics of S7 Distributed Safety and S7 F/FH Systems
Common Characteristics of S7 Distributed Safety and S7 F/FH Systems
S7 Distributed Safety and S7 F/FH Systems have the following important characteristics in
common:
•
Integration in S7-300 or S7-400 automation systems; the automation task determines the
system design, and fail-safe engineering is integrated into the system
•
Execution of standard control functions and protection functions on the same system
(standard system with fail-safe capability, which eliminates the need for dedicated fail-
safe solutions)
•
Connection of distributed I/O via PROFIBUS DP with PROFIsafe
•
Use of standard PROFIBUS components (copper and fiber-optic cable technology)
•
Configuration integrated in
STEP 7, same as for standard automation systems
•
Creation of safety program using standard programming languages of
STEP 7
•
Flexible adaptation to the task requirements by providing a wide range of fail-safe I/O
Comparison of System Performance of S7 Distributed Safety and
S7 F/FH Systems
The following table identifies the differences between the fail-safe systems with regard to
important performance characteristics.
Table 1-1
Performance Characteristics of F-Systems
Performance Characteristic
S7 Distributed Safety
S7 F/FH Systems
Achievable safety classes
SIL3/Category 4
SIL3/Category 4
Fault tolerance feature
available
No
Yes
Development stage
Fail-safe system
Fail-safe system
Fail-safe and fault-tolerant system
Connection of fail-safe I/O
•
Centralized and decentralized
via PROFIBUS DP
•
Distributed via PROFINET IO
(ET 200S and ET 200pro
F-modules)
•
Distributed via PROFIBUS DP
Minimum response time of
F-system (dependent on
configuration)
50 ms
100 ms
Typical response time of
F-system
100 ms to 200 ms
200 ms to 500 ms