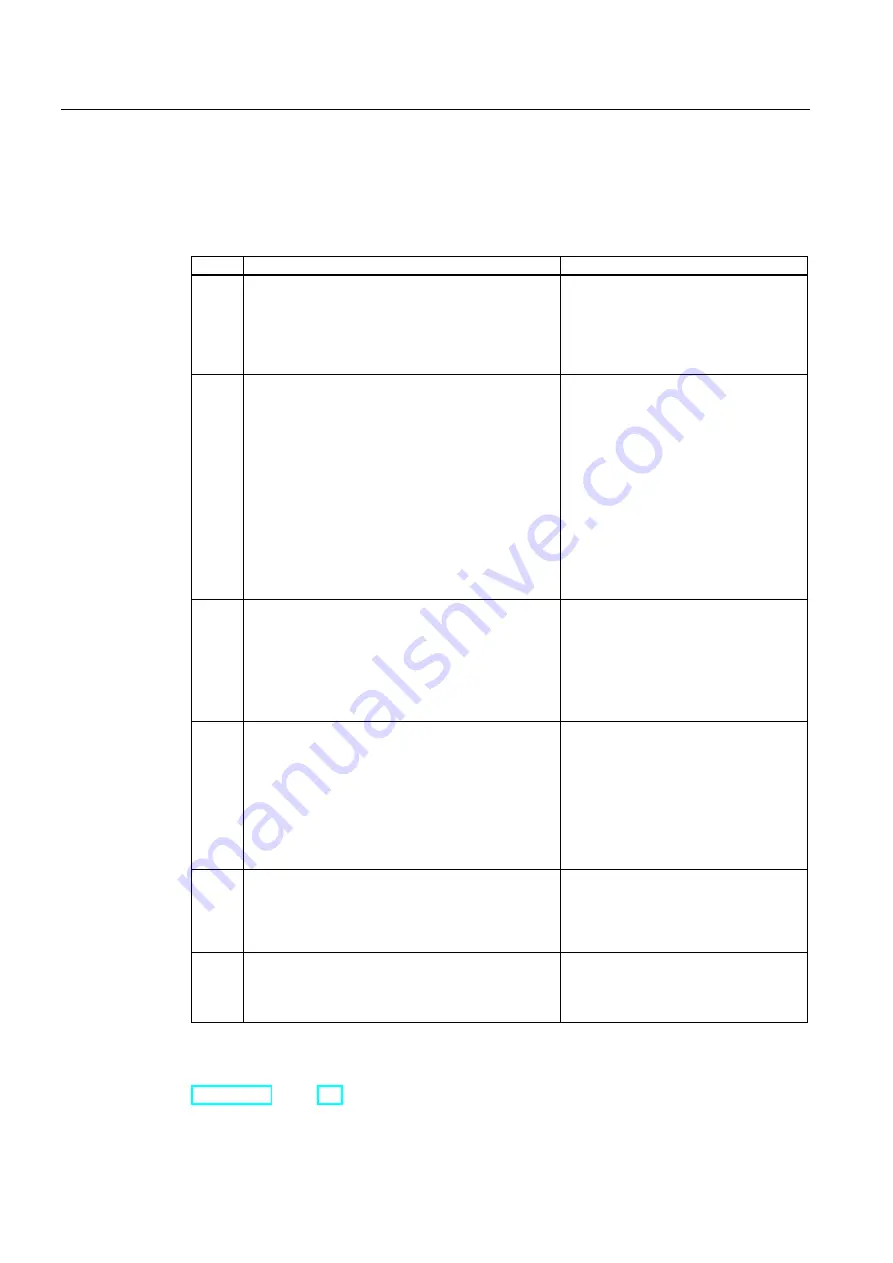
Overview of Fail-safe Systems
1.5 Guide to Working with F-Systems
Safety Engineering in SIMATIC S7
1-18
System Manual, 04/2006, A5E00109529-05
Sequence of Steps Ranging from Selection of Components to Maintenance of F-Systems
The following table provides references to manuals for obtaining information. The relevant
product information sheets provide additional information on the F-CPUs.
Table 1-7
Sequence of Steps Ranging from Selection of Hardware to Maintenance of F-Systems
Step
Procedure
Reference
1.
Plan system:
•
Specify safety functions with appropriate safety
classes (SIL/Category).
•
Specify S7 Distributed Safety, S7 F Systems,
or S7 FH Systems; select hardware and
software components.
Safety Engineering
system description,
"Overview of Fail-safe Systems"
section
Product catalog
2.
Configure hardware in STEP 7:
•
Configure F-CPU and assign parameters for
safety program.
•
Configure and assign parameters for fail-safe
I/O (F-SMs, F-modules) according to safety
class and wiring diagram.
•
Integrate and assign parameters for fail-safe
DP standard slaves and I/O standard devices.
Safety Engineering
system description,
"Configuring F-Systems"
section
S7 Distributed Safety:
S7 Distributed
Safety, Configuring and Programming
S7 F/FH Systems:
S7 F/FH Automation
Systems
ET 200S:
ET 200S, Fail-safe Modules
ET 200pro:
ET 200pro, Fail-safe
Modules
ET 200eco:
ET 200eco, Fail-safe I/O
Module
F-SMs
S7-300, Fail-safe Signal
Modules
3.
Set up hardware:
•
Set the PROFIsafe addresses on the ET 200S,
ET 200pro, ET 200eco, and S7-300 F-SMs via
switch.
•
Install modules.
•
Wire modules according to required wiring
diagram.
ET 200S:
ET 200S, Fail-safe Modules
ET 200pro:
ET 200pro, Fail-safe
Modules
ET 200eco:
ET 200eco, Fail-safe I/O
Module
F-SMs
S7-300, Fail-safe Signal
Modules
4.
Create safety program in STEP 7:
•
Create F-blocks or select them from F-library;
position, interconnect, and assign parameters
for F-blocks.
•
Compile safety program and download it to the
F-CPU.
•
Test safety program.
•
If necessary, modify safety program.
•
Document configuration and safety program.
Safety Engineering
system description,
"Programming F-Systems"
section
S7 Distributed Safety:
S7 Distributed
Safety, Configuring and Programming
S7 F/FH Systems:
S7 F/FH Automation
Systems
5.
Commission system:
•
If necessary, arrange for acceptance testing of
safety-related parts by the relevant authorities
before starting safety mode.
•
Commission system.
S7 Distributed Safety:
S7 Distributed
Safety, Configuring and Programming
S7 F/FH Systems:
S7 F/FH Automation
Systems
6.
Perform system maintenance:
•
Replace hardware and software components.
•
Update operating system.
•
Uninstall F-system.
S7 Distributed Safety:
S7 Distributed
Safety, Configuring and Programming
S7 F/FH Systems:
S7 F/FH Automation
Systems
See also