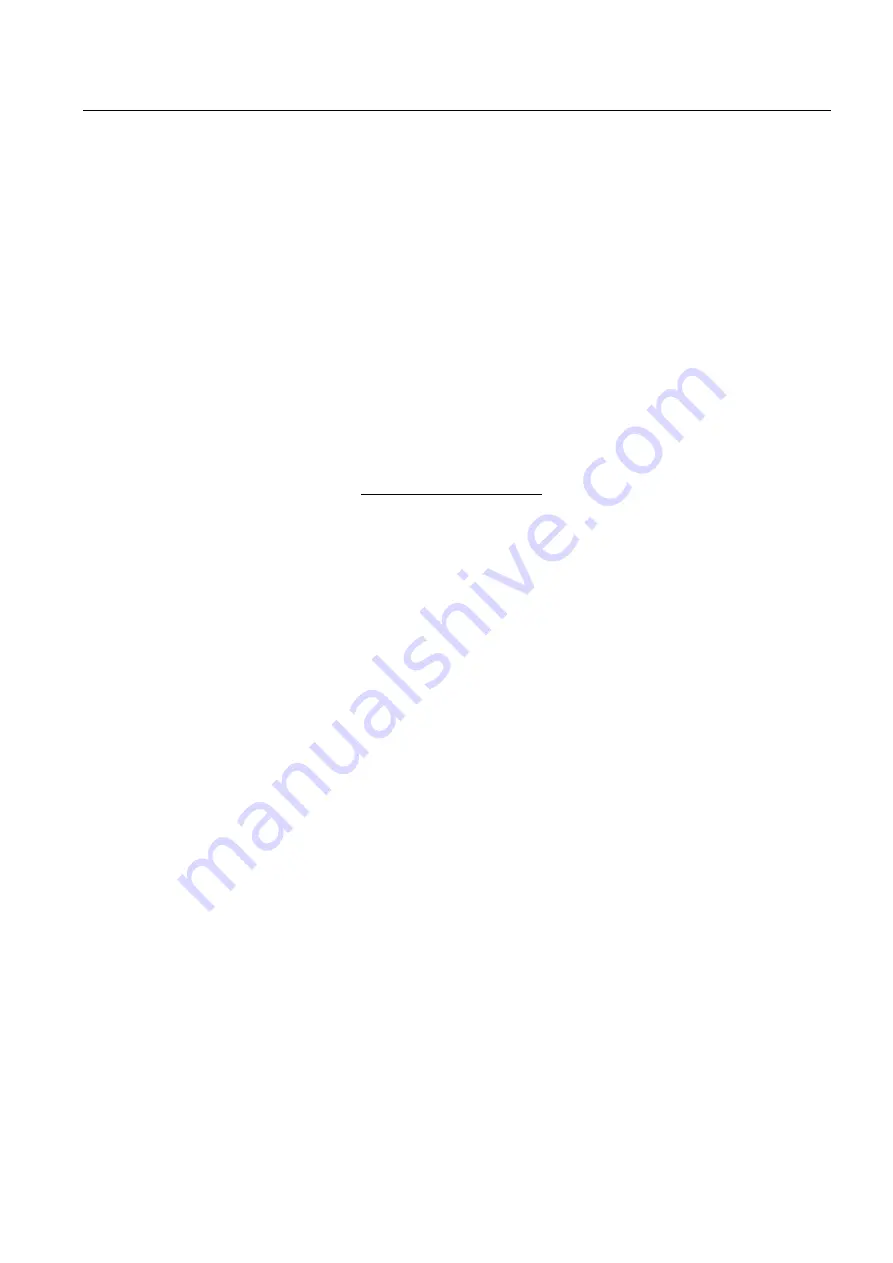
Description
3.4 Theory of Operation
FUS1010 IP65 NEMA 4X & IP66 NEMA 7
Operating Instructions, 01/2013, A5E02951520-AC
31
Channel 1+2 produces a data output via a virtual Channel 3, proportional to the sum of the
liquid and energy flow of two independent pipes. You have to set-up two channels
independently. Only clamp-on or in-line transit-time operation is supported.
Channel 1-2 produces a data output via a virtual Channel 3, proportional to the difference of
the liquid and energy flow of two independent pipes. You have to set-up two channels
independently. Only clamp-on or in-line transit-time operation is supported.
WideBeam Transmission
As shown in the figure above, an ultrasonic sensor induces an axial sonic beam within the
wall of the pipe. These vibrations spread along the pipe wall and then enter the liquid in the
form of a WideBeam wave front traveling at an angle to the main pipe axis. The wide beam
"rains" over the receiving sensor. The wide coverage of the receiver is necessary because
the angle of the sonic beam is related to the liquid’s sonic propagation velocity by Snell’s
Law.
%HDP$QJOH $UF6LQH
7UDQVGXFHU3KDVH9HORFLW\
/LTXLG6RQLF3URSDJDWLRQ9HORFLW\
According to this formula, it can be stated that as the liquid sonic propagation velocity
changes so will the angle between the sonic beam and the flow stream.
Therefore, a significant liquid sonic velocity shift could deflect a "narrow" beam transmission
away from the receiving sensor entirely. The upstream vs. downstream transit-time
difference will also be affected by the changing (or refracting) beam angle. This makes it
necessary for flow meter systems to continuously compute this angle, since it is subject to
varying degrees of refraction. The flow meter derives the angle by knowing the fixed position
of the sensors, the dimensions of the pipe and the measured transit-time.
Summary of Contents for FUS1010
Page 224: ......
Page 225: ......
Page 226: ......
Page 227: ......
Page 228: ......
Page 229: ......
Page 230: ......
Page 231: ......
Page 232: ......
Page 233: ......
Page 234: ......
Page 235: ......
Page 236: ......
Page 237: ......
Page 238: ......
Page 239: ......
Page 240: ......
Page 241: ......
Page 242: ......
Page 243: ......
Page 244: ......
Page 245: ......
Page 246: ......
Page 247: ......
Page 248: ......
Page 249: ......
Page 250: ......
Page 251: ......
Page 252: ......
Page 253: ......
Page 254: ......
Page 255: ......
Page 256: ......
Page 257: ......
Page 258: ......
Page 259: ......
Page 260: ......
Page 261: ......
Page 262: ......
Page 263: ......
Page 264: ......
Page 265: ...21614 C 1011NFPS 7 ...
Page 266: ...1011NFPS 7 C 21614 ...
Page 267: ...1011NFPS 7 C 21614 ...
Page 268: ...21614 C 1011NFPS 7 ...
Page 269: ......
Page 270: ......
Page 271: ......
Page 272: ......
Page 273: ......
Page 274: ...21614 C ...
Page 275: ......
Page 276: ......
Page 277: ...1012TN 7 INSTALLATION DRAWING 1010 SERIES TRANSDUCERS AND MOUNTING TRACKS 21614 C ...
Page 278: ...1012TN 7 INSTALLATION DRAWING 1010 SERIES TRANSDUCERS AND MOUNTING TRACKS 21614 C ...
Page 279: ...1012TNH 7 INSTALLATION DRAWING 1010 SERIES TRANSDUCERS AND MOUNTING TRACKS 21614 C ...
Page 280: ...1012TNH 7 INSTALLATION DRAWING 1010 SERIES TRANSDUCERS AND MOUNTING TRACKS 21614 C ...
Page 281: ......
Page 282: ......
Page 283: ......
Page 284: ......
Page 285: ......
Page 293: ...Glossary FUS1010 IP65 NEMA 4X IP66 NEMA 7 228 Operating Instructions 01 2013 A5E02951520 AC ...
Page 297: ...Index FUS1010 IP65 NEMA 4X IP66 NEMA 7 232 Operating Instructions 01 2013 A5E02951520 AC ...