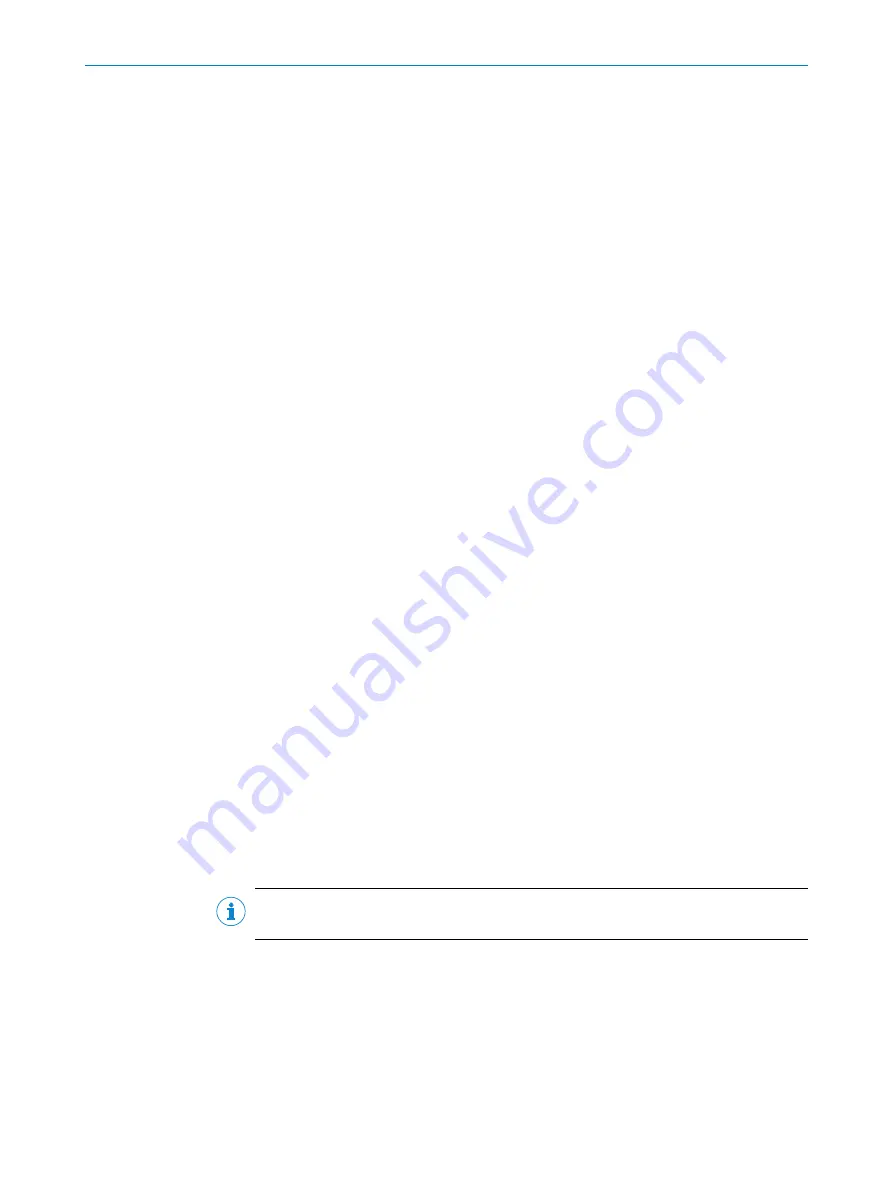
9.8.1.3
Digital output signal level warning
The device measures the amount of reflected light and can compare it to a reference
value to issue a warning to initiate a countermeasure. An external controller with
knowledge of the state of the overall safety function can use this value to derive the
measurement capability of the system.
To use the external signal level warning diagnostics, the switching function parameter
must be set to signal level warning. The result of the check whether the current
amount of reflected light is smaller than the taught-in or projected value (stored in the
signal threshold parameter) is then output at the assigned digital output. The output is
switched active when the condition is met.
To methods are generally used to teach in or configure the signal threshold.
Applications with varying measurement scenarios or objects to be detected:
Starting from the most demanding measurement scenario in the application (usually
lowest remission factor at highest distance), the measured signal level is reduced by
20% for aging and possibly further percentages for a high operating reserve.
Applications with a defined measurement scenario or a fixed object to be detected:
Starting from the scenario to be diagnosed in the application, this is reproduced, for
example by contaminating the windshield or target, and the signal threshold value for
this is recorded. Particular attention must be paid to the statistical fluctuation of the
measured value to determine whether it meets the requirements. Since the measure‐
ment capability has been verified at this signal threshold, no additional margins for
aging of the laser need to be factored in.
If there is an expected value for a certain object at a recurring distance, a contamina‐
tion detection can be performed by checking the signal level against a defined signal
threshold. An early warning of impending failures due to contamination can then be
issued and cleaning initiated before loss of device function occurs.
The diagnostics relate to the optical measuring path and can detect associated internal
and external errors.
9.8.1.4
IO-Link timeout
When communicating via IO-Link, the controller checks whether the communication
was successful within a defined time period. After a timeout, i.e., no successful commu‐
nication within the defined time period, the controller must assume the safe state
According to ISO 13849 4.5.4, a test or diagnostic rate equal to at least 100 times
the demand rate of the safety function is prescribed for category 2. The timer must
therefore always be adjusted for the demand rate and evaluated in the application.
This diagnostic measure enables faults in the logic and output path of the device to be
detected.
NOTE
This diagnostic measure is only able to be used via the IO-Link data interface
9.8.1.5
System response when the laser is switched off and on
The laser is periodically switched off and on via the safety-related input (MF input,
change from inactive to active and back to inactive). The “Clamp” alarm function or the
alarm function need to be configured via the digital output at the same time.
When switched off, no sufficient signal strength is achieved due to the absence of laser
light. As a result, the algorithm triggers the alarm state and the state changes is output
via the selected alarm function (“clamp” or switching output). For clamp this means:
Digital outputs change to the safety-related state or remain in this state while the input
9
PROJECT PLANNING
52
O P E R A T I N G I N S T R U C T I O N S | DT35S
8027663//2022-08-04 | SICK
Subject to change without notice