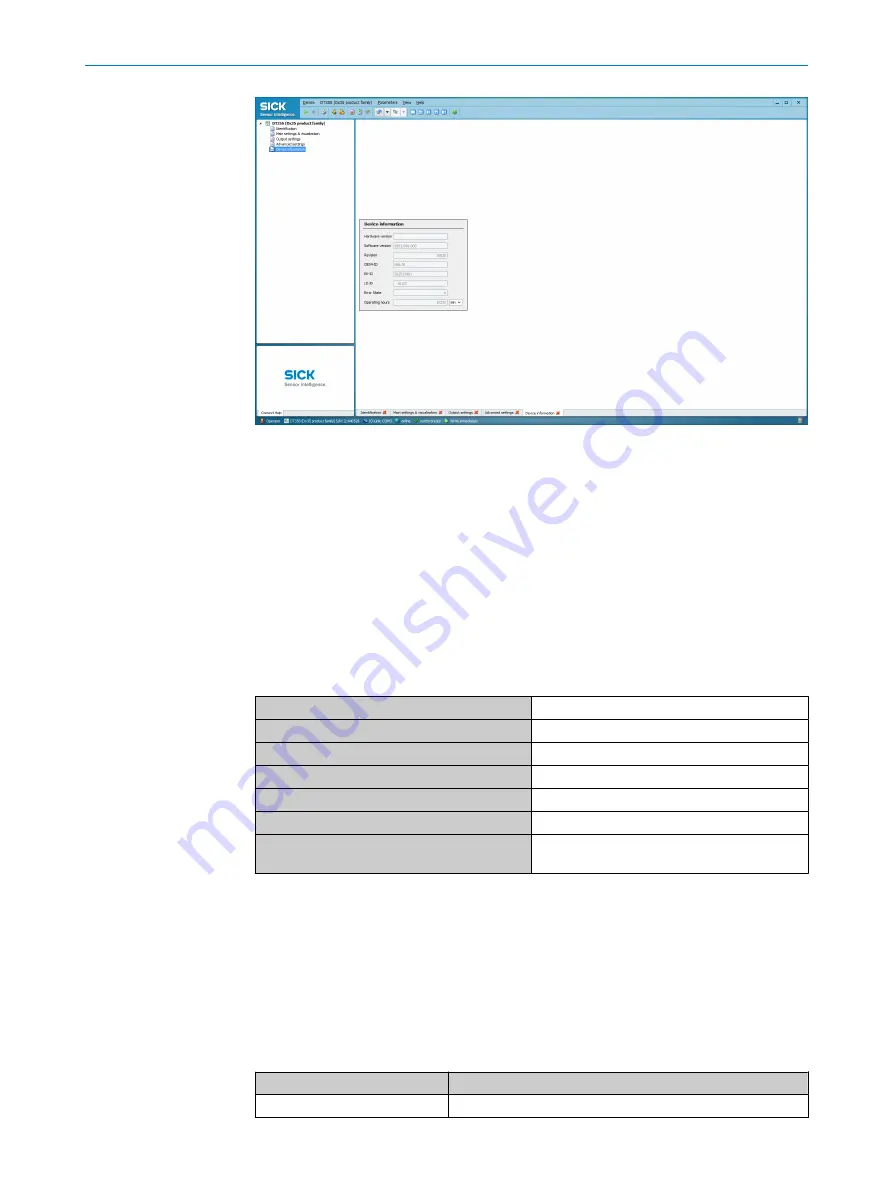
7.3.6
Preventing unintended or unauthorized modification
To prevent unintentional modification, configuration of the device is only allowed via
SOPAS ET and the SiLink2 master required for this. The output of the sensor must be
connected directly to the SiLink2 master. This means that if modification of the device
parameters is desired, the device must first be disconnected from the application. The
device can then be connected to a computer on which SOPAS ET is installed via the SiL‐
ink2 master. The system integrator is responsible for ensuring that this is only done by
authorized and also instructed personnel. The system integrator is also responsible for
checking whether further measures are required to prevent unauthorized modification.
7.4
IO-Link interface
Table 2: Properties of the IO-Link interface
IO-Link specification
V1.1
SIO mode (standard I/O mode)
Yes
Minimum cycle time
2.3 ms
Transmission rate
COM2 (38.4 kBaud)
Process data width
16-bit outgoing (from the device to the master)
Process data type
UINT (unsigned integer)
Parameter configuration server function (data
storage)
Yes
The device-specific IO-Link device description and the IODD can be found on the
product page, which can be accessed via the
SICK Product ID
pid.sick.com/
{P/N}
{P/N}
corresponds to the part number of the product (see type label).
7.4.1
Process data
The process data have a data width of 16 bits. The content can be adjusted using the
“process data structure” index 83. Factory setting for index 83: Option “0”: Distance
(14 bit) + status Q1 + status Q2
Table 3: Process data
Description
Value
Access
Read
7
COMMISSIONING AND CONFIGURATION
44
O P E R A T I N G I N S T R U C T I O N S | DT35S
8027663//2022-08-04 | SICK
Subject to change without notice