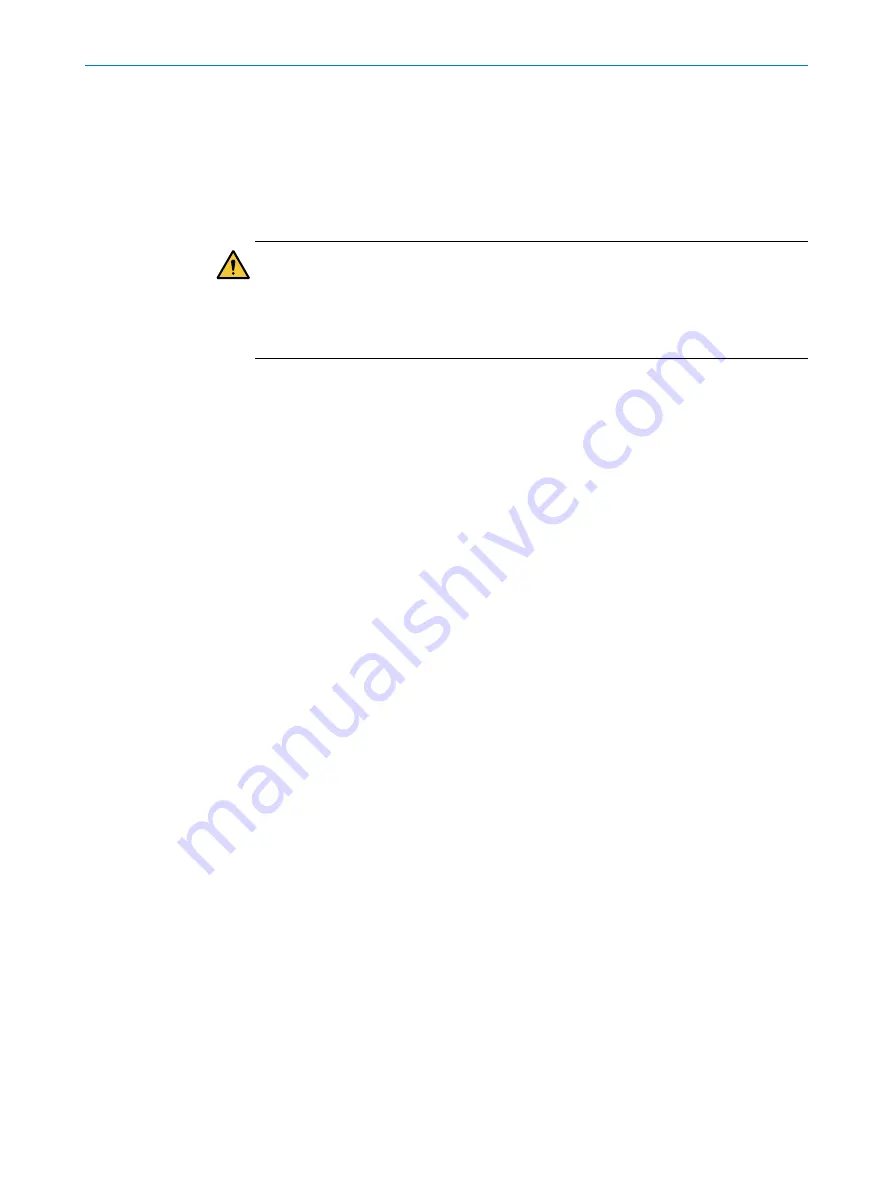
b
Avoid having strong electric fields in the vicinity of the device. These may be
caused by nearby welding or induction cables, for example.
b
Prevent condensation on and/or contamination of the viewing window. To ensure
the continuing, reliable safety function of the device, the viewing window must be
cleaned regularly.
9.3
Preventing unprotected areas
WARNING
Risk of ineffectiveness of the protective device!
The objects to be protected may not be recognized in case of non-observance.
•
Make sure that the following conditions are met so that the device can fulfill its
protective function.
b
The device must be mounted in such a way that objects are reliably detected when
they enter the hazardous area.
b
The device must be affixed so that no mirrors or other highly specular objects
(e.g., due to gloss effects) are in the detection zone, thereby limiting the detection
capability.
b
The device must be affixed so that no small objects (e.g., cables) are in the
detection zone, even if the safety outputs do not switch to the OFF state as a
result.
b
The device must be affixed so that no obstacles disrupt the safety sensor’s field
of view. Take additional protective measures if a risk arises due to unavoidable
obstacles.
b
If objects can be present between the protective device and the hazardous point
without being detected, check if additional protective measures (e.g., restart inter‐
lock) are required.
b
The optical beam path must not be disrupted, e.g. if the system is incorporated
into paneling. No additional protective screen may be fitted.
9.4
Response time of the device
The response times of the device must be taken into account, among other things, so
that the device can be positioned in a suitable location and the switching points can be
configured correctly.
The response times are specified in the technical data,
9.5
Basic measurement deviations
When determining the safe position or distance in the application, the statistical and
systematic error must always be taken into account.
Manual specification of the distance value for the switching point setting
When entering distance values as switching points (without using the teach-in function),
both types of error must be taken into account. This gives a total measurement devia‐
tion of 50 mm. When using the safety-related switching functions, this value must be
taken into account during project planning and must result in an increase in the safety
ranges.
To prevent constant switching of the safety function, the hysteresis can be set to
25 mm and, in case of constantly changing ambient conditions, also to 50 mm.
Unchanging conditions and a high signal quality also allow a hysteresis of 10 mm.
PROJECT PLANNING
9
8027663//2022-08-04 | SICK
O P E R A T I N G I N S T R U C T I O N S | DT35S
49
Subject to change without notice