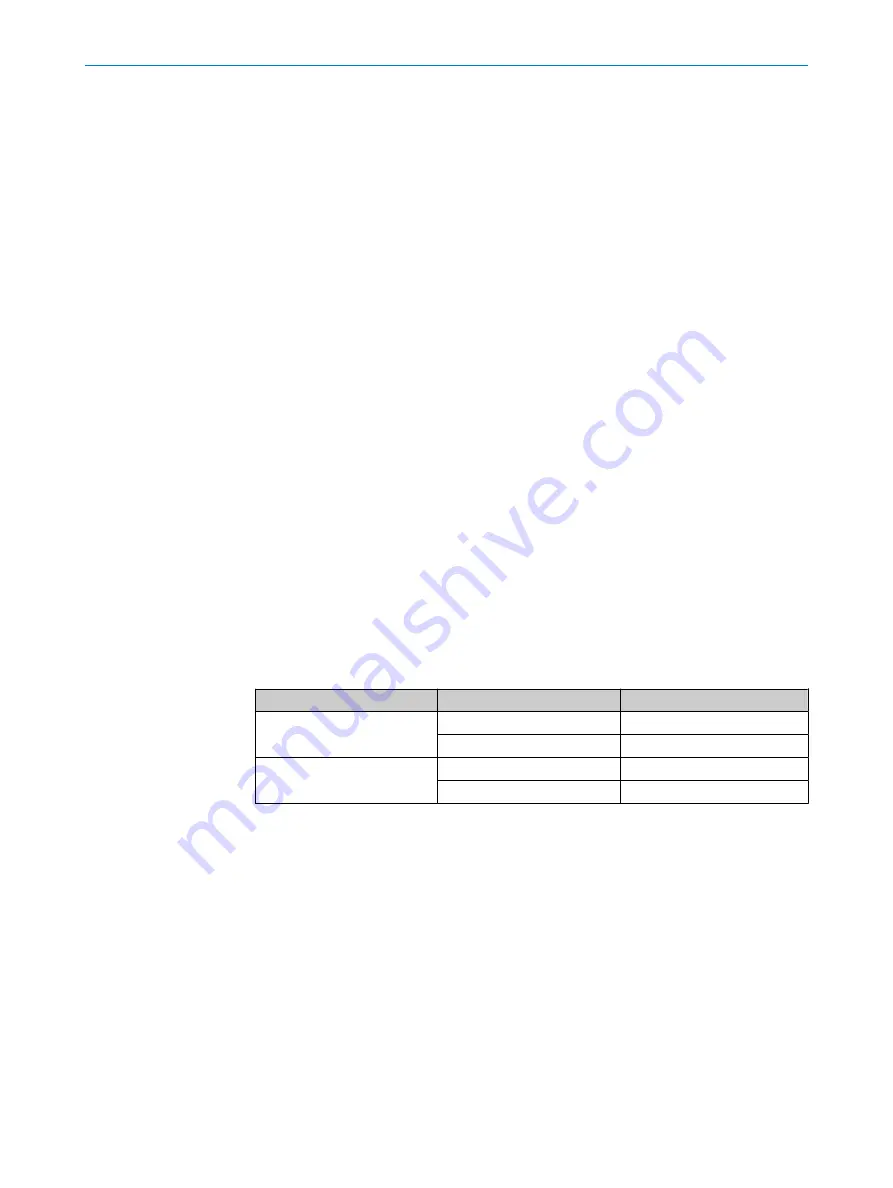
Using the teach function for switching point adjustment
If the exact position value is important for selecting the switching points, the switching
point can be determined using another measuring device and adjusted by means of
a teach in. The systematic error can be minimized while doing so. Any measurement
deviation can then be attributed solely to the statistical error and the total error will
amount to 25 mm. In this case, the ambient conditions that lead to the change in
systematic errors must be kept constant.
9.6
Dynamic measurement deviations
The dynamic measurement deviation represents the deviation between the real dis‐
tance and the distance output when the device and/or the object to be detected moves
with velocity v at a point in time. The dynamic measurement error can be estimated
assuming a constant velocity.
X = v x T
X: Dynamic measurement deviation
v: speed
T: Response time
To evaluate the dynamic deviation from the real position within the scope of a safety
function, the following must be considered separately for safety-related systems:
•
Time required for data transmission from the device to the safe evaluation unit
•
Time required for the data evaluation itself
Allowed approach speeds in the application
Depending on the device variant and the speed setting of the device, the approach
speeds present in the application must be limited to the values shown in the table.
This ensures that the dynamic measurement errors, which depend on the respective
response times, remain commensurate with the other errors.
Table 5: Allowed approach speed
Device variant
Speed setting
Max. allowed approach speed
DT35S-B15251
Medium
5 m/s
Slow
2 m/s
DT35S-B15551
Medium
2 m/s
Slow
1 m/s
When considering high approach speeds in the application, care must be taken how‐
ever to ensure that the required minimum distances, e.g., to stop a mobile platform,
can be maintained. This applies in particular if objects with a low remission factor (for
example 6%) are to be detected in an associated short safety-related detection range.
9.7
Calculation of minimum distances in the application
The calculation of the minimum distance is based on international or national stand‐
ards and statutory requirements applicable at the place of installation of the machine.
The minimum distance depends, among other things, on the following:
•
Machine stopping time (time interval between triggering of the safety function and
assumption of the safe machine state, including signal propagation times in the
network and processing time in the controller)
•
Response time of the entire protective device
•
Position of the device, e.g., on the vehicle
•
Speed of the sensor platform
9
PROJECT PLANNING
50
O P E R A T I N G I N S T R U C T I O N S | DT35S
8027663//2022-08-04 | SICK
Subject to change without notice