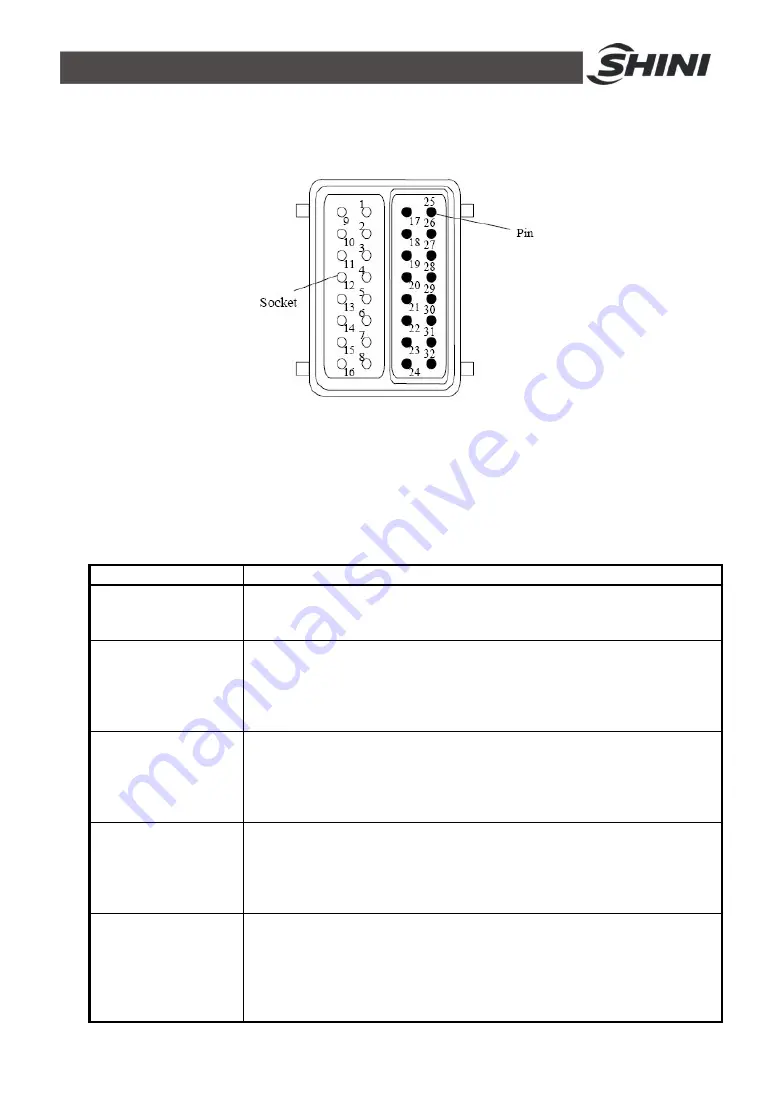
32(142)
2.5.2 Euromap12 Interface
The interface consists of the plug connection between the injection molding
machine and the robot:
The robot-injection molding machine interface is designed according to
Euromap12, which state:
Unless otherwise noted, the signals are maintained during the described
function.
2.5.2.1
Injection Molding Machine Output Signals
Plug Contact No.
Function
1
,
9
Emergency stop of machine
The emergency stop switch of the injection molding machine is used to
interrupt the emergence stop circuit of the robot.
2
Mold open
The switch contact (pin contact 16) is closed when mould opening position is
equal or more than required position. Inadvertent alteration to mould opening
stroke smaller than that required for the handing device to approach must be
impossible.
3
,
11
Safety system active
The switch contact is closed when safety devices (e.g. safety guard,
footboard safety, etc.) on the injection molding machine are operative so that
dangerous movements of the handing device/robot are possible. The signal is
active in any operation mode.
4
Ejector back
The switch contact is closed when the ejector has been retracted regardless
of the moving platen position. (See pin contact No.16) acknowledgement f or
the
“
Enable ejector back
”
signal (see pin contact No 21), when the ejector
sequence is selected. (see pin contact No.16)
5
Ejector forward
The switch contact (see pin contact No.16) is closed when the ejector has
been advanced. The signal is the acknowledgement signal for the
“
enable
ejector forward
”
(see pin contact No 22).
It is recommended to close the switch contact when the ejector sequence not
in use. (see pin contact No.16)
Summary of Contents for ST1-S
Page 1: ...ST1 S User Manual Date May 2016 Vision V1 0 English ...
Page 2: ......
Page 10: ...10 142 ...
Page 94: ...94 142 7 Assembly Diagram 7 1 Traverse Unit ST1 S and ST1 T S Picture 7 1 ...
Page 99: ...99 142 7 2 Vertical Unit ST1 S Picture 7 2 ...
Page 102: ...102 142 7 3 Main Arm Unit ST1 S Picture 7 3 ...
Page 105: ...105 142 7 4 Sub arm Unit ST1 S Picture 7 4 ...
Page 108: ...108 142 7 5 Main Arm ST1 T S Picture 7 5 ...
Page 110: ...110 142 7 6 Sub arm ST1 T S Picture 7 6 ...
Page 113: ...113 142 7 7 Vertical ST1 T S Picture 7 7 ...
Page 115: ...115 142 7 8 Traverse Unit ST1 T S Middle Telescopic Arm Picture 7 8 ...
Page 119: ...119 142 7 9 Main Arm ST1 T S Middel Telescopic Arm Picture 7 9 ...
Page 123: ...123 142 7 10 Sub arm ST1 T S Middel Telescopic Arm Picture 7 10 ...
Page 127: ...127 142 7 11 Crosswise Unit ST1 T S Middle Telescopic Arm Picture 7 11 ...
Page 131: ...131 142 8 1 2 The Panasonic Servo Motor and Servo Driver Wiring Diagram Picture 8 2 ...
Page 132: ...132 142 8 1 3 The Panasonic Servo Motor and I O Board Wiring Diagram Picture 8 3 ...
Page 133: ...133 142 8 1 4 The Delta Servo Motor and Servo Driver Wiring Diagram Picture 8 4 ...
Page 134: ...134 142 8 1 5 The Delta Servo Motor and I O Board Wiring Diagram Picture 8 5 ...
Page 135: ...135 142 8 1 6 The Cuinsico Servo Motor and Servo Driver Wiring Diagram Picture 8 6 ...
Page 136: ...136 142 8 1 7 The Cuinsico Servo Motor and I O Board Wiring Diagram Picture 8 7 ...
Page 137: ...137 142 8 1 8 Z axis I O Board Wiring Diagram Picture 8 8 ...
Page 138: ...138 142 8 1 9 Main Arm Wiring Diagram Picture 8 9 ...
Page 139: ...139 142 8 1 10 Sub arm Wiring Diagram Picture 8 10 ...
Page 140: ...140 142 8 1 11 Main Arm Output Wirng Diagram Picture 8 11 ...
Page 141: ...141 142 8 1 12 Signals Input Wiring Diagram Picture 8 12 ...
Page 142: ...142 142 8 1 13 Signals Output Wiring Diagram Picture 8 13 ...