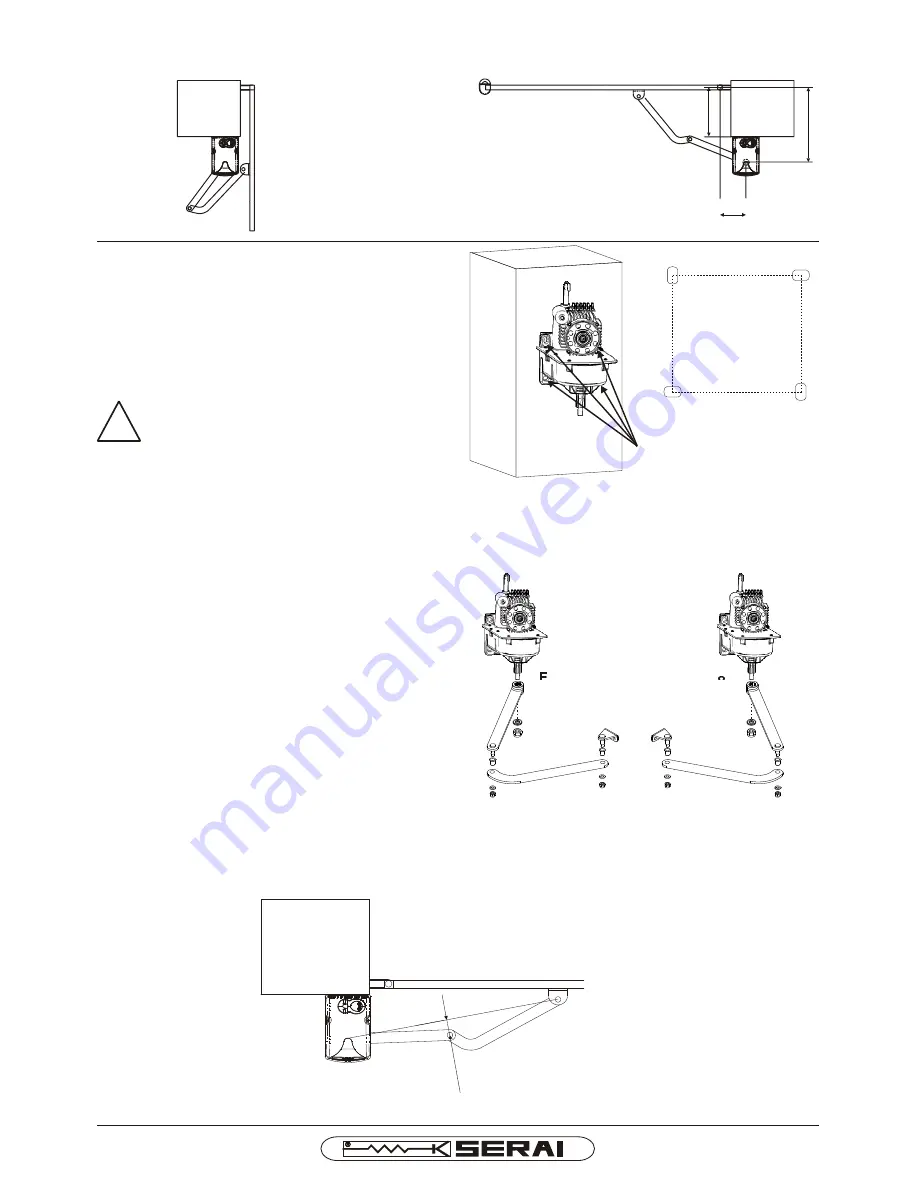
DA
L
19
65
Page 5/18
4 MOTOR FIXING POINTS
EXAMPLE FOR GATE INSTALLED TOWARDS THE EXTERNAL PART OF THE PILLAR
B
=
5
1
2
A=160
M
A
X
3
5
0
INSTALLATION
Fig. 5
MOTOR FIXING
POINTS INTERAXIS
3 -
After having defined the position of installation, fix
the motor to the pillar using N°4 M8 screws (hex
head or cylindrical head with recessed hexagon)
complete with large washer (external diameter
24mm) with fixing system suitable for the type of
pillar.
4 -
fig.7-8.
5 -
Assemble the levers, in left and right assembly, only
the position of the curved arm differs while the
straight arm must always be mounted with the pin
downwards, see
Insert the straight lever bush into the toothed outlet
of the shaft and fix it using the nut and washer.
Fig. 7
Fig. 6
Fig. 8
110mm
1
0
0
m
m
6 -
fig.9.
7 -
8 -
9 -
Position the articulated arm bracket on the gate as far away from the column as possible, extending the arms
to maximum and always respecting the measurement of
as indicated in
Fix the articulated arm bracket to the leaf suitably using screws or by welding.
Keeping the motor reducer released, check the correct movement of the articulated arm and of the leaf.
Repeat the same operation for the other leaf.
C
³
100
C
³
100
Fig. 9
K
IT
/A
9
I
E
!
ATTENTION:
- Should pillar be too narrow, e.g. 100mm,
use the plate K/88
- Should pillar be made of light material,
e.g. stones or tuff, the strength of the
motor against the mechanical stops
could be too high for a normal fixing
system and the motor could come off the
pillar. Use in this case a proper fixing
plate