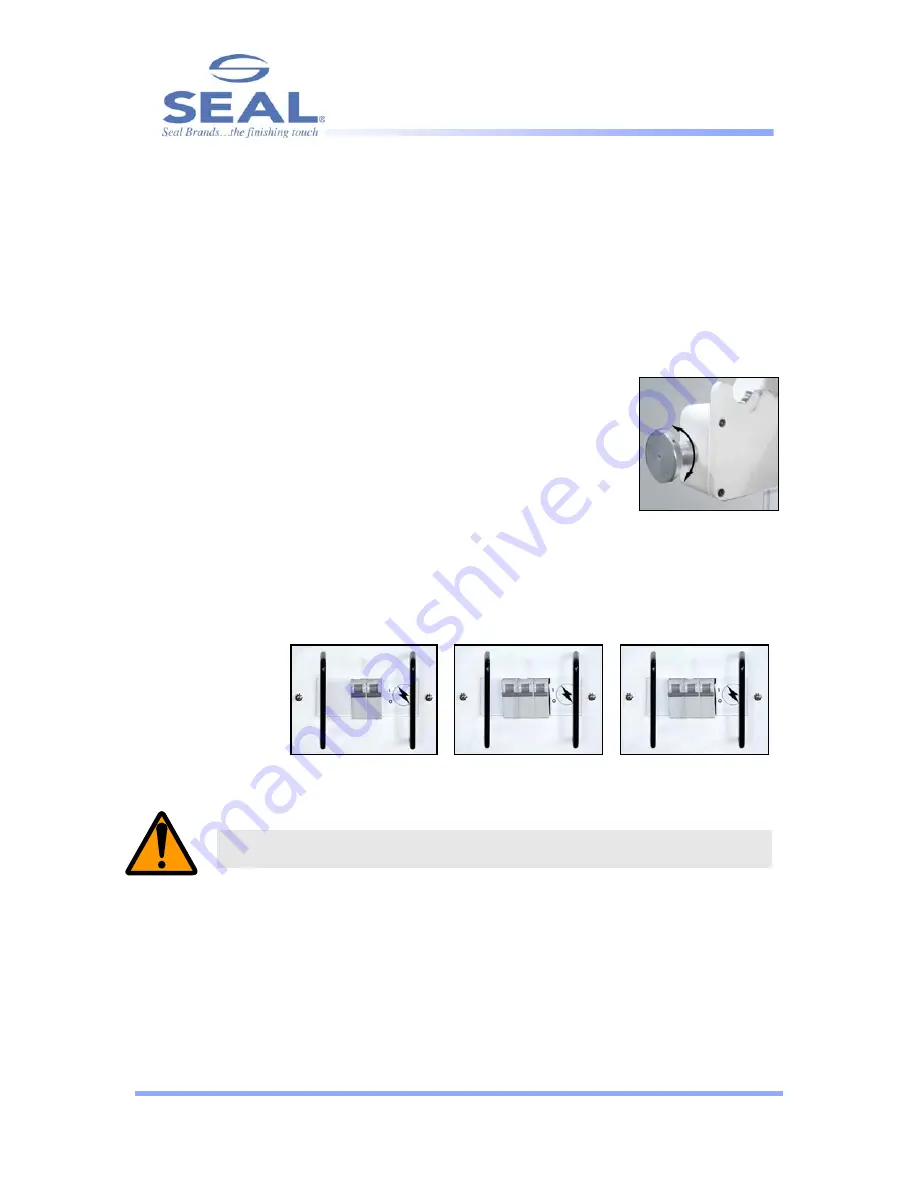
2.1 AccuCure
Feed-back
System
The AccuCure Feed-back System is a PLC-based control system that
utilizes sensors and feedback loop to control coater throughput. The
system allows the operator to select operating modes: (1) TEMP
Mode – an infrared temperature sensor on the back of the Dryer
Panel is used to monitor the substrate temperature (2) SPEED Mode
– an encoder reads the revolution speed on the Web Idler Roller as it
is turned by substrate passing over it.
2.2 Brake
Tension
Control
The Brake Tension Control knob is used to
provide back tension on the substrate during
operation. The Brake Tension Control knob
increases or decreases braking pressure on the
Unwind Roller. Turning the knob clockwise adds
braking pressure and counter-clockwise reduces
braking pressure.
Figure 6: Brake Tension
Control
2.3 Main Circuit Breaker Switch
The Main Circuit Breaker Switch controls all ON/OFF power coming to
the machine.
60 Amp Single Phase
50 Amp Three Phase
30 Amp Three Phase
Figure 7: Circuit Breakers
WARNING:
DO NOT OPEN CABINET DOORS UNTIL THE MAIN
CIRCUIT BREAKER SWITCH IS TURNED OFF.
2.4 Connections
2.4.1 Power Connection - This is where the unit connects to your power
source (see Section 3 for Specifications).
2.4.2 Compressed Air Connection - The connection where an outside source
for compressed air is connected (see Section 3 for Specifications).
7
Summary of Contents for AquaSEAL SW-2600
Page 4: ......
Page 43: ...Notes 31 33 ...