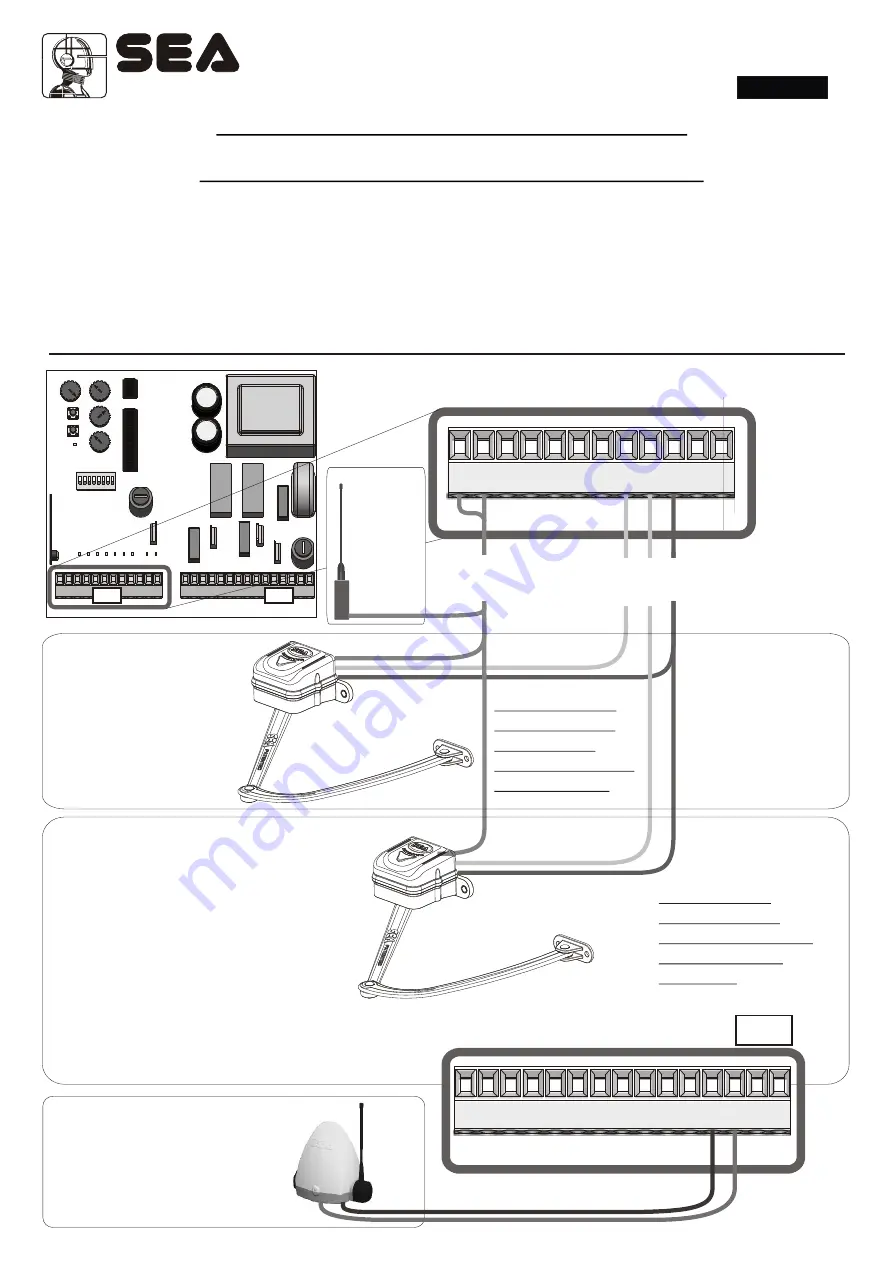
CN1
CN2
10 11 12
1 2 3 4 5 6 7 8 9
SAFETY GATE
SAFETY GATE
SWING 2
2
10
8
2
9
10
-
+
12
13
CN2
10 11 12 13 14 15
1 2 3 4 5 6 7 8 9
Working with DIP 4 placed to ON position and exclusively in working
times self-learning mode.
ENCODER (SAFETY GATE)
MANAGEMENT ACTIVATION
After executing the four programming steps of the card, after connecting the encoder of both the motors and
executing themotor torque adjustments using trimmer RV1 and/or mechanical adjustment devices (by-pass
valves), place DIP 4 to ON position and repeat the programming procedure.
If necessary it’ s possible to disable the SAFETY GATE management placing DIP 4 to OFF position, without
repeating the self-learning times procedure.
SAFETY GATE (ENCODER), FLASHING LAMP
Encoder 2
The encoder (Safety Gate) is a
s y s t e m f o r o b s t a c l e s
detection. It is set in the factory
on a middle level but can be
modified. Low sensibility
levels do not allow a fast
inversion as required by the
En12453 rules.
Connect the encoder 2 as in
the picture.
NOTE: Only in
working times
selflearning
mode (DIP8 OFF
and DIP4 ON)
Encoder 1
The encoder (Safety Gate) is a system for
obstacles detection.
Connect the encoder 1 as in the picture.
The Encoder function can be used in single leaf
modality.
Note: With the PALM device or through the
Trimer Rv4 on board of the control unit. it is
possible to adjust the sensibility of the
encoder on a scale from 0 to 15, where 0
indicates the max. sensibility during the
inversion.
Note: Every time when there is no current
supply and after every osbstacle the
automation, when no limit switches are
installed, will proceed slowly until it reaches
the stop.
Note: Only in
working times
selflearning mode
(DIP8 OFF and
DIP4 ON)
Flashing lamp (230V 50W
MAX)
Connect the flashing lamp as in
the picture.
It’s possible to ebable a pre-
flashing of 3 seconds putting DIP2
to ON position.
~
30
Brown
White
White
Green
English
After an Encoder
intervention and in case
of power supply failure,
the leaves will proceed at
reduced speed until they
reached their referring
stops.
Sistemi Elettronici
di Apertura Porte e Cancelli
International registered trademark n. 804888
®
REV 07 - 05/2009
1
2
Antenna
C o n n e c t
the antenna
as in the
picture.
The sensibility of the
encoder is adjustable
through the Trimmer
Rv4 on board of the
unit, see pag.27.