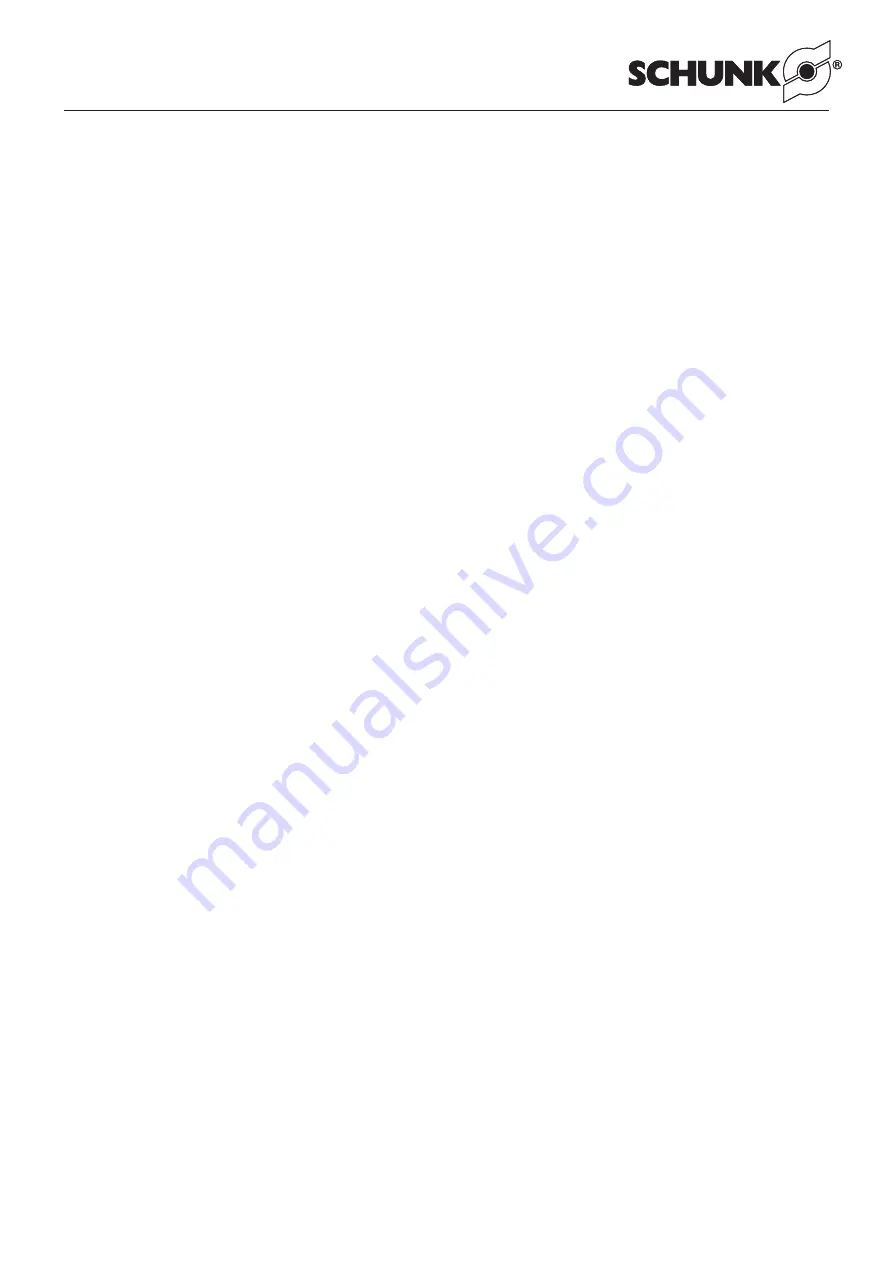
18
������
Eines der beiden Sicherheitsventile hat sich in seinem
Ventilsitz festgesetzt. Dies kann verschiedene Gründe
haben (verschmutztes Öl, Überdruck, Korrosion, Verände-
rungen der Temperatur, Verschleiß der Innenteile des
Sicherheitsventils). Den Hydraulikdruck abstellen und die
beiden Entlüftungsschrauben A und B öffnen (siehe Bild 3
auf Seite 23). Beachten Sie, dass eine der beiden Zy-
linderkammern noch unter Druck steht. Nach dem Öffnen
dieser Entlüftungsschrauben tritt eine geringe Menge Öl
aus. Hierdurch werden die Rückschlagventile druckent-
lastet. Die Entlüftungsschrauben wieder einsetzen. Sollte
sich der Kolben des Spannzylinders immer noch nicht
bewegen, wird es notwendig, eines oder beide Rück-
schlagventile auzutauschen (siehe Anleitung).
������
Überprüfen Sie, dass das verwendete Zugrohr nicht zu
lang (oder zu kurz) ist, und somit einen mechanischen
axialen Stopp des Kolbenhubes herbeiführt.
������
Die Abdichtung an der Vorder- und der Rückseite wird
durch dynamische Radialdichtringe durchgeführt (siehe
Bild 3 auf Seite 23).
A) Bei einer Leckage an der Rückseite wird lediglich die
Abdeckung 6B entfernt und die Dichtung 37B ersetzt.
B) Bei Leckage an der Vorderseite ist es notwendig, die
komplette Zuführung zu demontieren und die vordere
Dichtung 37B zu ersetzen. In diesem Fall empfehlen
wir, die hintere Dichtung sowie die beiden Lager 46B
und 47B ebenfalls zu ersetzen, die bei dieser Demon-
tage evtl. beschädigt werden können.
������
Bei einer Leckage an der Vorderseite zwischen dem
Zylinderkörper 1 und der Kolbenstange 3A muss die
Dichtung 26 ersetzt werden.
Bei einer Leckage an der Rückseite zwischen dem
\/erteilerflansch 2 und der Kolbenstange 3A ist es not-
wendig, die Dichtung 25 zu ersetzen.
������
Vorausgesetzt die Hydraulikeinheit der Maschine ist von
ihrer Größe her korrekt ausgelegt, bestehen noch fol-
gende Fehlerquellen:
– im Hydraulikkreislauf
– im Spannzylinder
������
Probleme im Hydraulikkreislauf:
A) Die Druckfiiter sind verstopft und erlauben nicht den
vollen Durchfluss der Pumpenleistung. In diesem Fall
bitte Filtereinheiten reinigen oder ersetzen.
Beachten
Sie, dass der Druckfilter einen Filtereinsatz mit 10
µm Feinheit haben muss. Dieser muss alle 6 – 8
Monate ersetzt werden.
B) Die Pumpe ist verschlissen und bringt nicht mehr die
volle Förderleistung. Die Förderleistung überprüfen.
Sollte die Förderleistung nicht ausreichend sein, die
Pumpe ersetzen.
C) Die Magnetventile öffnen nicht vollständig und redu-
zieren somit den Durchflussquerschnitt. Dies kann
durch
Verschleiß
der
Ventile
oder
durch
Ver-
schmutzung hervorgerufen werden.
������
Probleme im Hydraulikzylinder: Um festzustellen, ob das
Problem im Hydraulikkreislauf oder im Zylinder liegt, 2
Manometer in die Entlüftungsbohrungen A und B ein-
setzen. Hierfür geeignete Verschraubungen verwenden
(siehe Bild 3 auf Seite 23).
������
One of the two safety valves jammed into its seat, due to
different reasons (dirty oil, overpressure, water ham-
mering, changes in temperature, wear of the internal
components of the valves). Keeping the power unit without
pressure, carefully unscrew the 2 drain screws A and B
(see illustr. 3 on page 23). Be careful that one of the cylin-
der chambers is still under pressure. By loosing these
screws, a certain quantity of oil will come out from one of
them, resetting the valve control. Reassemble and tighten
the screws, then, operate the cylinder. If the piston does
still not move, it is necessary to change 1 or 2 safety valves
(see instructions).
������
Check that the draw tube for the connection to the chuck is
not too long (or too short), causing a mechanical axial stop,
hindering the piston stroke.
������
The oil seal between the front and rear parts of the oil
manifold is made by means of ratating rubber seals (see
illustr. 3 on page 23).
A) If the leakage is in the rear is it is only necessary to
remove the rear cover 6B and change the rear seal
37B.
B) If the leakage from the front, it is necessary to dis-
mantle the complete oil manifold group and change the
front seal 37B. In this case our suggestion is to also
change the rear seal and the bearings 46B and 47B
which could have been damaged during the dis-
mantling operations.
������
If the leakage is in the front side between the body 1 and
the piston rod 3A it is necessary to change the rubber seal
26.
If the leakage is in the rear, between the distribution flange
2 and the piston rod 3A, it is necessary to change the
rubber seal 25.
������
Let’s suppose that the machine tool manufacturer
dimensioned the power unit considering the real needs of
oil capacity. If the power unit is well dimensioned, there
can be two kinds of problems:
– in the hydraulic circult
– in the cylinder
������
Problems in the hydraulic circuit:
A) The filters are clogged and do not allow the regular flow
of the pump capacity: in this case, clean the filters and,
if necessary, replace them.
NOTE: Be careful that the
delivery filter must be a paper filter with 10 µ
aperture size and must be replaced every 6 – 8
months.
B) The pump is worn and does not guarantee the regular
delivery. Measure the delivery in l/min. and, if it is not
enough, replace the pump.
C) The solenoid valves do not make the whole stroke and
reduce the room for the oil flow. It can be caused by
wear of the valves or by the entry of dirty oil between
the pistons.
������
Problems in the hydraulic cylinder: To be sure if the
problem is in the hydraulic circuit or in the cylinder, mount
2 gauges in the drain holes A and B, using 2 suitable
fittings (see illustr. 3 on page 23).