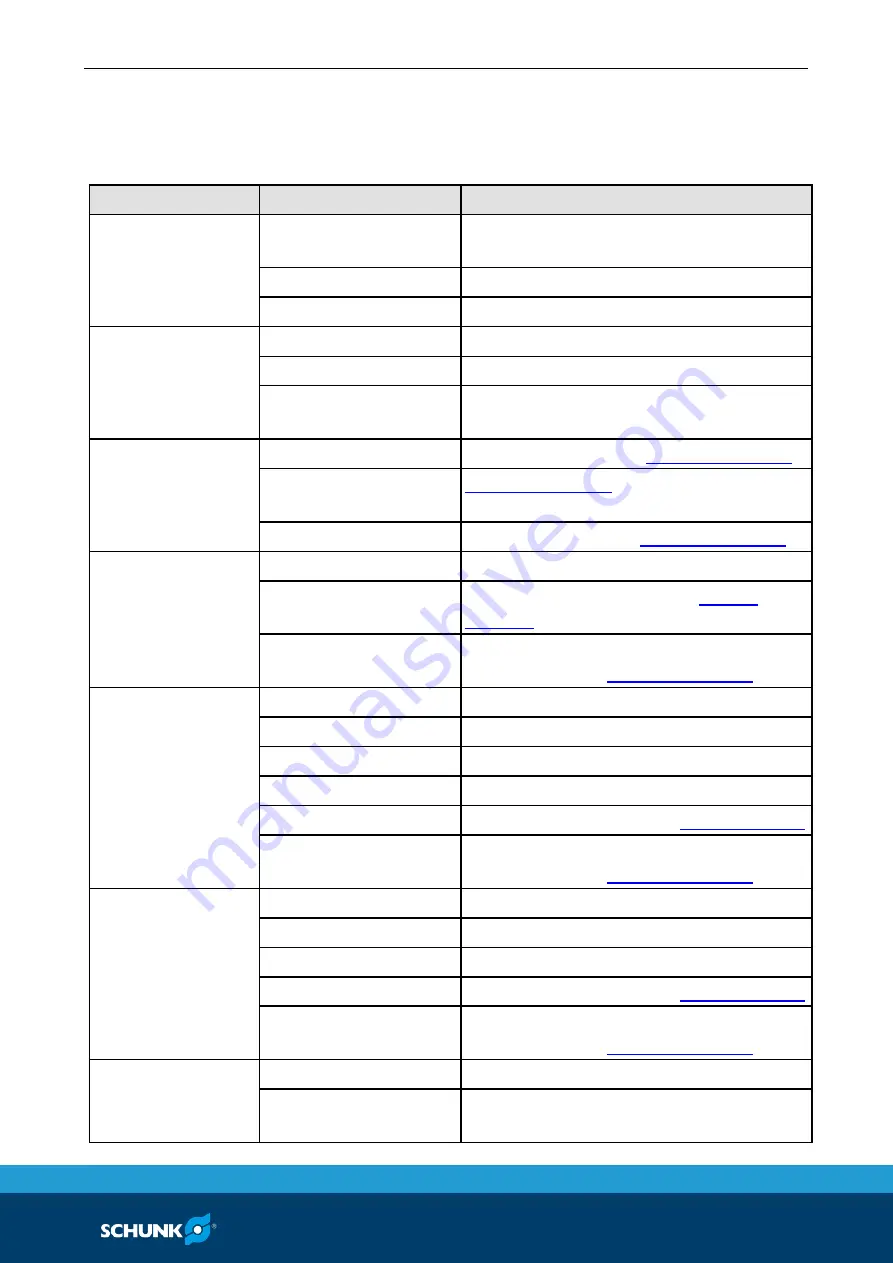
Troubleshooting
02.01|FDB 150, 300, 340, 660, 900, 1040 |en
33
Troubleshooting
Deburring process development is an iterative, learning task. The fol-
lowing table is presented to assist in solving deburring problems.
Symptom
Cause
Resolution
Burr Wear
Hard work material
Use better grade burr material add coating
(TiAlN)
Too heavy a cut
Decrease width of cut/make multiple passes
Feed rate is too slow
Increase feed rate
Burr Breakage
Too heavy a cut
Decrease width of cut/make multiple passes
Deflection at corner
Climb mill/do not begin path at sharp corner
Impacting part
Decrease feed rate at contact/ enter part
at an angle
Unequal compliance Pivot bearing worn
Compliance preload
screw not set properly
Worn ring cylinder
Poor finish on
work piece
Feed rate is too fast
Reduce feed rate
Burr is worn
Inspect burr if worn, replace.
Motor bearings are
worn
Inspect spindle shaft, if shaft feels loose or
Burr Chattering
during cut
Feed rate is too fast
Reduce feed rate
Lack of rigidity
Increase radial compliance pressure
Too heavy a cut
Decrease width of cut/make multiple passes
Improper Burr selection Choose burr designed for work material
Burr is worn
Motor bearings are
worn
Inspect spindle shaft, if shaft feels loose or
Secondary Burrs
created on work
piece after cut
Incorrect feed rate
Reduce feed rate
Too heavy a cut
Decrease width of cut/make multiple passes
Improper Burr selection Choose burr designed for work material
Burr is worn
Motor bearings are worn Inspect spindle shaft, if shaft feels loose or
Chip Packing of Burr Too heavy a cut
Decrease width of cut/make multiple passes
Not enough chip clear-
ance
Use a burr with less flutes
7