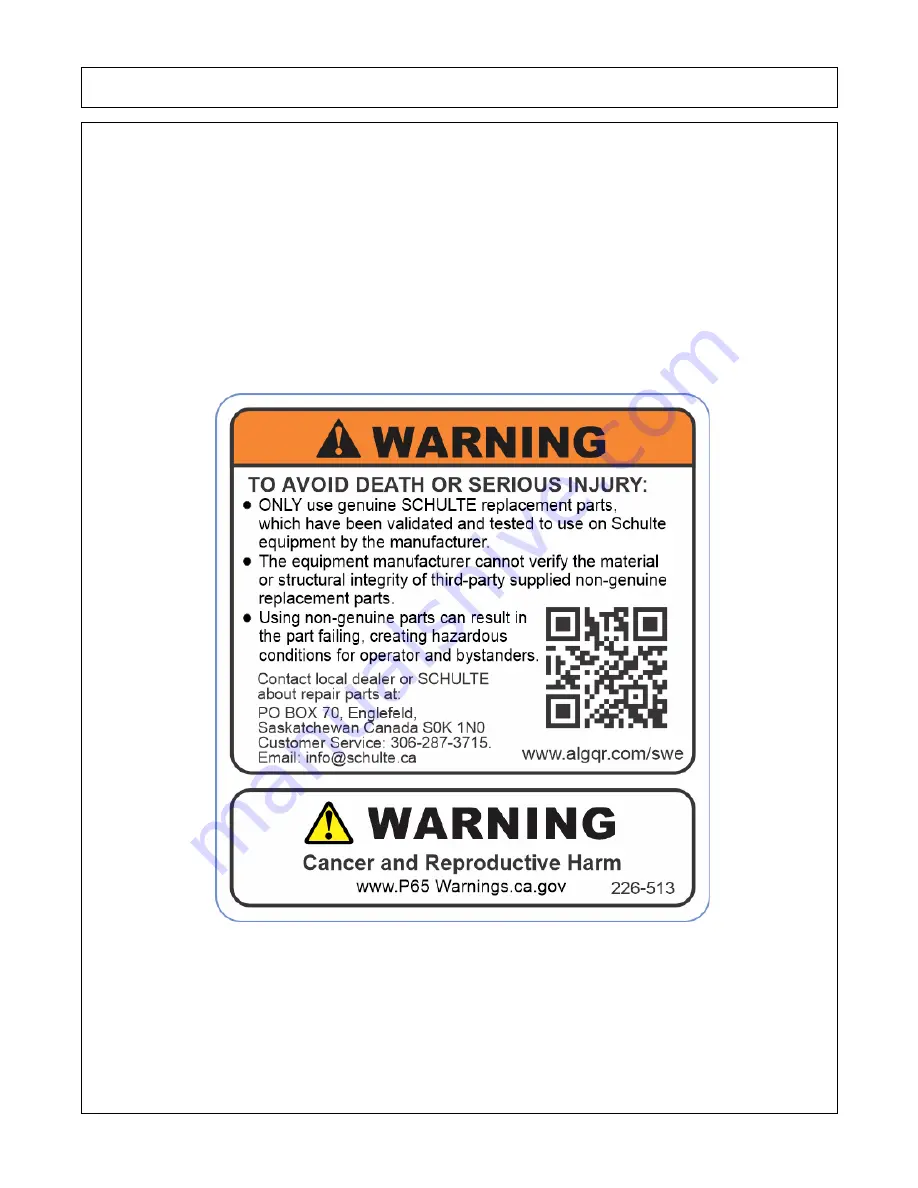
INTRODUCTION
Titan 5000 Series II 01/22
Introduction Section 2-3
© 2022 Alamo Group Inc.
Attention Owner/Operator
BEFORE OPERATING THIS MACHINE:
1. Carefully read the Operator’s Manual, completely understand the Safety Messages and instructions, and
know how to operate correctly both the tractor and Implement.
2. Fill out the Warranty Card in full. Be sure to answer all questions, including the Serial Number of the
Implement. Mail within 30 days of delivery date of this implement.
NOTE:
Warranties are honored only if completed “Owner Registration and Warranty” forms are received by
Schulte within thirty days of delivery of the implement.
3. Record the Rock Picker Model and Serial Numbers on the Warranty page at the front of the Operator’s
Manual. Keep this as part of the permanent maintenance file for the Implement.
Summary of Contents for Titan 5000 II Series
Page 4: ......
Page 7: ...Safety Section 1 1 2022 Alamo Group Inc SAFETY SECTION ...
Page 22: ...SAFETY Titan 5000 Series II 01 22 Safety Section 1 16 2022 Alamo Group Inc SAFETY ...
Page 23: ...SAFETY Titan 5000 Series II 01 22 Safety Section 1 17 2022 Alamo Group Inc SAFETY ...
Page 24: ...SAFETY Titan 5000 Series II 01 22 Safety Section 1 18 2022 Alamo Group Inc SAFETY ...
Page 25: ...SAFETY Titan 5000 Series II 01 22 Safety Section 1 19 2022 Alamo Group Inc SAFETY ...
Page 26: ...SAFETY Titan 5000 Series II 01 22 Safety Section 1 20 2022 Alamo Group Inc SAFETY ...
Page 27: ...SAFETY Titan 5000 Series II 01 22 Safety Section 1 21 2022 Alamo Group Inc SAFETY ...
Page 29: ...Introduction Section 2 1 2022 Alamo Group Inc INTRODUCTION SECTION ...
Page 34: ......
Page 35: ...Assembly Section 3 1 2022 Alamo Group Inc ASSEMBLY SECTION ...
Page 49: ...ASSEMBLY Titan 5000 Series II 01 22 Assembly Section 3 15 2022 Alamo Group Inc ASSEMBLY ...
Page 62: ......
Page 63: ...Operation Section 4 1 2022 Alamo Group Inc OPERATION SECTION ...
Page 97: ...Maintenance Section 5 1 2022 Alamo Group Inc MAINTENANCE SECTION ...
Page 106: ......
Page 107: ......
Page 108: ...Titan 5000 Series II 01 22 P N R801 010C Printed Canada ...