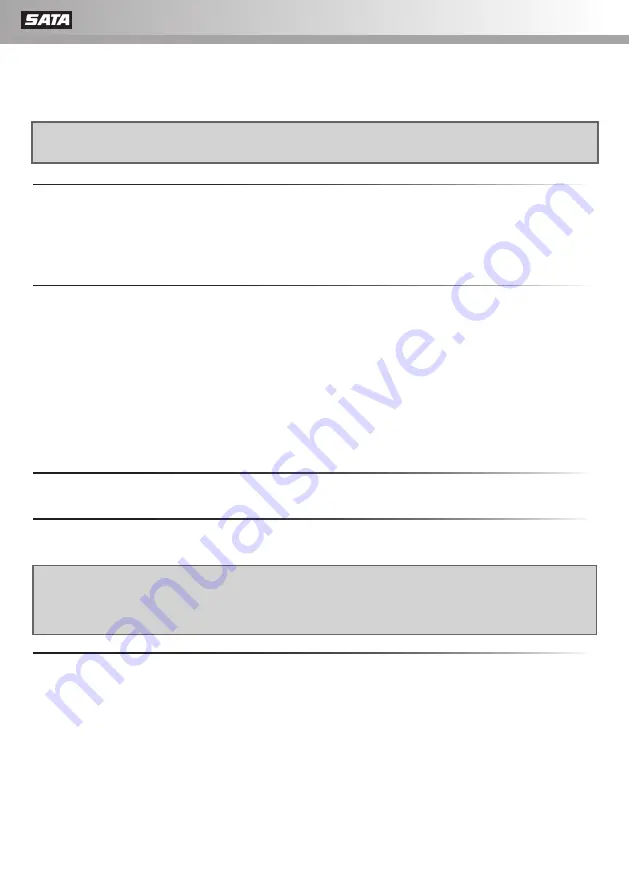
Prior to putting into operation the system, read the operating instructions completely and thoroughly. The stipulations contained therein are to be respected in any case. After that,
the operating instructions are to be stored in a safe place, accessible for every user of the equipment. The system/paint spray gun may only be put into operation by persons
familiar with ist use (professionals). Inappropriate use of the system/paint spray gun, modification of any kind or combination with inappropriate other parts may cause serious
hazard to the user’s, other person’s or animal’s health or even death. SATA shall not take any responsibility for such damages (e.g. failure to respect the stipulations laid out in the
operating instructions). The applicable safety, workplace and worker health protection regulations of the respective country or area/district in which the system/paint spray gun is
used are to be respected in any case (e.g. the German Rules for the Prevention of Accidents BGR 500 issued by the Central Office of the Professional Trade Associations, etc.).
Caution!
When using solvents and cleaning agents based on halogenated hydrocarbons e.g. 1.1.1-trichlorethylene and methylene chloride, chemical reactions can occur on
the aluminium cup, gun and on galvanized components (small quantities of water added to 1.1.1-trichlorethyelene produce hydrochloric acid). This can cause oxidation of the
components; in extreme cases, the reaction can be explosive. Therefore only use solvents and cleaning agents for your paint gun which do not contain the substances named
above. Never use acid for cleaning purposes.
Never point paint spray gun at yourself or at other persons. Solvents and diluting agents can cause burns. Only the respective quantities of solvents and material required for work
progress may be present in the direct surroundings of the unit and are to be returned after work to their assigned storage rooms. Before any repair work may be carried out, the
unit must be disconnected from the compressed air network and pressure must be released. Before starting to use the paint gun, particularly after repairs, ensure that screws and
nuts are correctly tightened, and check that gun and hoses do not leak. Defect components must be replaced or repaired, use original spare parts only.
No ignition source is permitted within the operation area, since the use of this equipment/these paint spray guns may easily cause inflammable compounds. Occupational safety
regulations must be applied when painting (respiratory protection etc.). Appropriate ear protection muffs are required, as a sound level of 90 dB(A) can be exceeded when painting
under higher pressure levels. No vibration is transmitted to the upper parts of the operator‘s body during the painting process.
Recoil forces are negligible.
The use of this product in explosion hazard areas Zone 0 is prohibited.
The paint spray gun and the pump dolphin with pressure transmission 14:1 and the pump shark with pressure transmission 32:1 are used fpr processing paints and varnishes
and other free-flowing materials. Abrasive and acid materials and those containing petrol may not be processed. The pump only works when the material is actually required, so
that it should be seperated from the compressed air network during any interruptions to operations. Please observe the pot life for 2-component paints, as the material can no
longer be removed from the pump when this time has expired.
1 Chassis
2 Stand,
cpl.
3 Wall holder, cpl.
4 Pump height adjustment
5 Pump
engine
6 Material pressure regulator
7 Atomization air pressure regulator
8 High pressure filter
9 Neck for rinsing liquid
10 Gun material connection
11 Air connection G ¼ ext.
12 Suction pipe
a) Before dispatching the paint spray gun it was treated with rust proofing equipment; we recommend to clean the spray gun thoroughly with detergent before operation.
b) Unscrew air pressure control completely, connect pump with compressed air network, place container under suction pipe (see 12), adjust required values with gun in
triggered position. Check spraying result on paper or similar and adjust to achieve optimum results by altering the pressure.
a) After use, thoroughly clean pump and gun (cleaning fluid is to remain inside the pump)
b) If performance decreases, put 1 drop of thin machine oil into the air inlet, and check suction sieve for material remainders; clean if necessary.
c) Never immerse pump into cleaning fluid.
d) In case of leakage tighten or replace packings.
The warranty conditions are valid provided that the supplier has a manufacturer’s guarantee according to offer.
a) The supplier grants a guarantee period of 12 months for this kind of equipment; the guarantee period commences on the date of sale to the final customer.
b) The guarantee covers the material value of components with manufacturing and material faults which are detected during the guarantee period. The guarantee does not
cover any damage caused by incorrect handling, normal wear or mechanical damage.
c) Any other further claims of any sort lodged against the supplier, particularly claims for damages, are ruled out. This also applies to damages caused during consultation
talks, instruction sessions and demonstrations. The final customer‘s rights vis-à-vis his contracting partner remain unaffected.
d) If the customer requires immediate repair or replacement before ascertaining whether we as suppliers are obliged to provide replacement, the replacement delivery or
repairs are provided and will be invoiced and paid according to the currently valid price. If further verification of the complaint reveals that the customer is entitled to claim
under the guarantee, the purchaser shall receive a credit note corresponding to the guarantee service provided for the invoiced repair or replacement delivery. Components
for which replacements have been delivered become the property of the supplier again. Notifications of faults or other complaints do not entitle the customer or his repre
sentative to refuse or delay payment.
e) The unit is to be returned with transport costs paid. The supplier does not assume any costs for delegating engineers (travelling time and costs) together with freight and
packaging costs. The supplier‘s conditions for the delegation of engineers apply here.
f) Any services provided under the guarantee do not prolong the guarantee period.
g) The guarantee becomes null and void in the event of any third-party interference
h) These guarantee conditions are an integral part of the supplier‘s general conditions of delivery.
SATA, SATAjet, the SATA Logo and/or other SATA products referenced herein are either registered trademarks or trademarks of SATA Farbspritztechnik GmbH & Co. KG in the
U.S. and/or other countries. The names of companies and products mentioned herein may be the trademarks of their respective owners.
To be noted
1. Construction and description of functions
2. Putting into operation
3. Service and maintenance
4. Guarantee conditions
Subject to technical alterations
Important Notice:
Paint spray guns may be cleaned with solvent or cleaning agents manually or in a conventional gun washing machine.
The procedures mentioned below will damage the guns/systems and may lead to expiry of the explosion proofness certificate as well as total loss of any
waranty:
- Immersing the paint spray gun in solvent or cleaning agents, or for a period longer than required for the cleaning process as such
- Failure to remove the paint spray gun from the gun washing machine after finishing the cleaning process
- Cleaning the paint spray gun by means of ultrasound cleaning systems
Operating Instructions
- 6 -
13 Material sieve
14 Material ball tap
15 Barrel fixing
16 Suction tube
17 Hose pair
18 SATAjet 3000 K spray mix Paint spray gun
19 Stepless regulation for round and flat spray
20 Trigger
21 Material filter G ¼ ext.
22 Paint pipe
23 Nozzle set