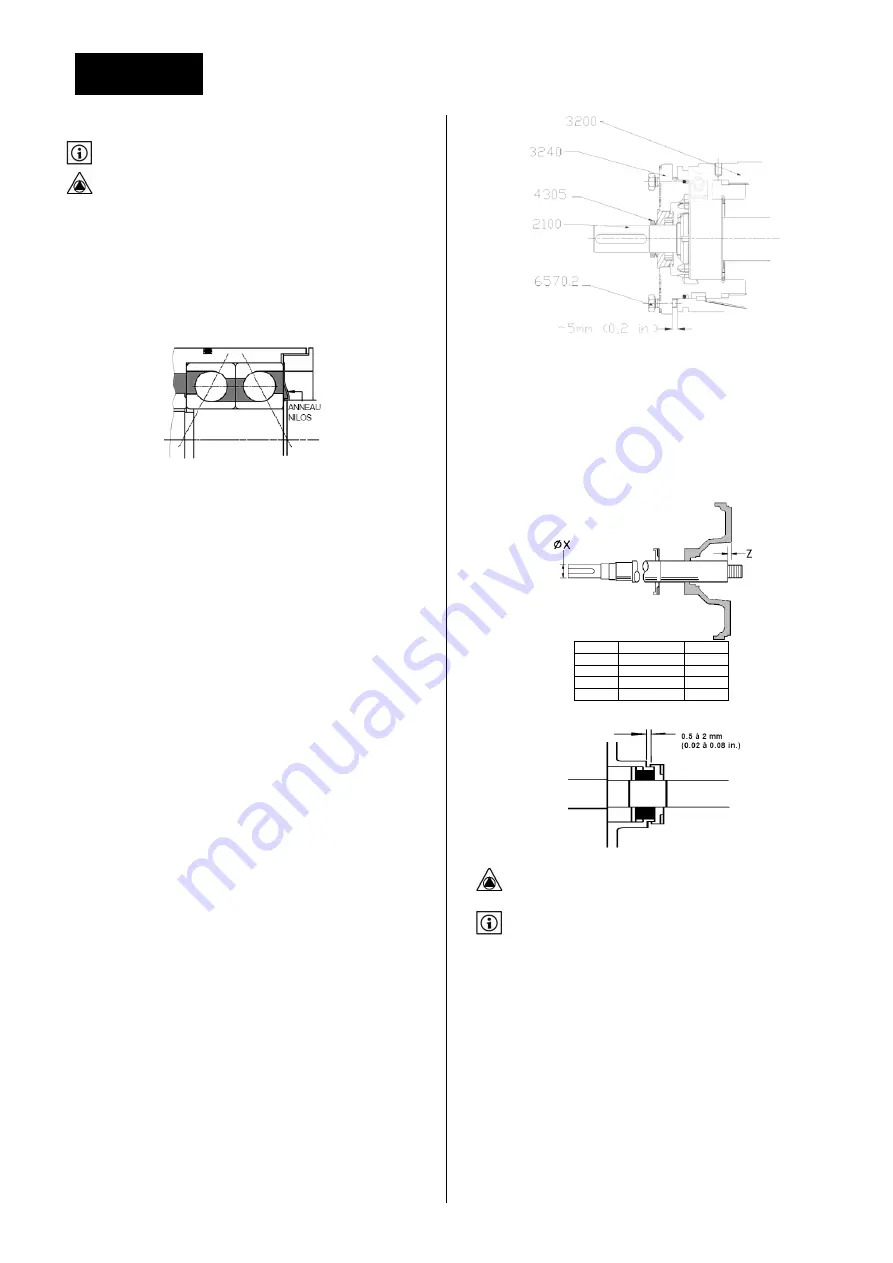
ENGLISH
18
9.3.2
RE-ASSEMBLY
To assemble the pump consult the sectional drawings.
Ensure threads, gasket and O-ring mating faces are clean. Apply
thread sealant to non-face-sealing pipe thread fittings.
9.3.2.1 ASSEMBLY OF BEARING BRACKET AND SHAFT
1. Clean the inside of the bearing housing 3200, bearing carrier 3240 and
bores for bearings.
2. Attach bearing housing support foot 3134.
3. Fit the thrust ball bearing 3013 on to shaft 2100.
The double row thrust bearing must not have a filling slot, as such
bearings are limited to taking thrust in only one direction. If the pair of
angular contact thrust bearings are to be fitted, these must be mounted
back-to-back, as shown below :
Grease retainer (clearance type) is only fitted on grease lubricated units.
The following methods are recommended to set the bearings onto the
shaft:
1
rst
method
: Use a hotplate, hot bath, oven or induction heater to heat
the bearing race so it can easily be placed in position then allowed to
shrink and grip the shaft. It is important that the temperature is not
raised above 100 ºC.
2
nd
method
: Press the bearing onto the shaft using equipment that can
provide a steady, even load to the inner race. Take care to avoid
damaging the bearing and shaft.
4. With bearings at ambient temperature, screw on the self-locking
bearing locknut 3712.1 (with its polyamide insert facing away from the
bearing) until tight.
5. With the double row thrust bearing place the bearing circlip 6544 over
the shaft, with the tapered face facing the impeller end.
6. With the heavy duty thrust bearing option, the lock nut 3712.2, 3864
grease retainer and 3712.2 if grease lubricated, should be placed on the
shaft with the larger diameter end facing the impeller end.
7. Fit pump radial ball bearing 3011 onto the shaft using Method 1 or 2
above.
8. With the NUP roller bearing option, the loose ring should be against
the shaft shoulder.
9. Fit O-ring 4610.2 on the bearing carrier. Lightly lubricate the bearing
carrier bore and O-ring.
10. If a labyrinth seal is used make sure that the oil port is positioned
downward (if any question ask manufacturer).
11. Ensure the shaft keyway edges are free of burrs. During installation,
use shimming or tape over the keyway to avoid damaging the drive side
bearing seals.
12. On grease lubricated pumps, ¾ fill the space between bearing races
with the appropriate grease.
13. Slide the bearing carrier 3240 onto the shaft/ bearing assembly and
insert inner circlip 6544 into the carrier groove or screw up the bearing
locking ring.
14. Check shaft 2100 for free rotation.
15. Fit the labyrinth ring 4330 into the bearing housing 3200 ensuring
the drain hole faces the bearing and is at the 6 o'clock position.
16. Install the shaft assembly into the bearing housing 3200 until the gap
is approximately 5 mm (0.2 in.).
17. Fit the bearing carrier screws 6570.1 but do not tighten
18. Press drive side v-ring 4305 and pump side liquid deflector 2540 onto
shaft 2100 where applicable. The V-ring type shall be fitted with light
contact with the bearing carrier 3240.
19. The pump side deflector 2540 (this feature is integral with some
proprietary labyrinth seals) should only be set in its final position after
setting the shaft axial position.
20. Temporarily fit the cover 1220 to the power-end. The cover, above
125 size, is retained by studs 6580 and their nuts. The shaft 2100 may
now be positioned in relation to the cover face, by rotating the carrier,
position as shown below:
Palier
Dia. X mm
Z mm
1
24
9
2
32
17
3
42
9
4
48
22
21. The pump side deflector 2540 may then be moved towards the
bearing housing 3200 and set with its clearance.
9.3.2.2 ASSEMBY OF MECHANICA L SEAL
Extreme cleanliness is required. The sealing faces and shaft [2100]
or sleeve [2400] surface must be free from scratches or other
damage.
Refer to following section to know mechanical seal positioning.
1. Carefully press the stationary seat into the cover 1220 or mechanical
seal cover 4213, ensuring that the seating ring is not deformed. Where
an anti-rotation pin is fitted ensure that correct engagement with the
slot is achieved.
2. Place any separate seal covers over the shaft 2100.
3. Refer to manufacturer's instructions to position the mechanical seal
rotating elements. Tighten any drive screws in the seal drive collar. For
precise compression most cartridge seals should be set after complete
pump assembly.
4. Fit the cover 1220 into the bearing housing 3200 and tighten all
fasteners.
9.3.2.3 ASSEMBLY OF GLAND PA CKED STUFFING BOX
1. Assemble the gland packing 4130 into the cover before fitting on to
the shaft 2100.
2. Stagger the joints in the gland packing by 90 degrees to each other.
3. The lantern ring halves 4134, if required, should be positioned mid-
way along the packing.
Summary of Contents for NEX
Page 2: ......
Page 27: ...FRAN AIS 27 12 1 1 PLAN EN COUPE Roue ouverte Roue aubes invers es...
Page 29: ...FRAN AIS 29 13 DECLARATION CE...
Page 30: ...FRAN AIS 30...
Page 53: ...ENGLISH 25 12 1 1 SECTIONAL DRAWING Open impeller Reverse vane impeller...
Page 55: ...ENGLISH 27 13 EC DECLARATION OF CONFORMITY...
Page 56: ...ENGLISH 28...
Page 59: ...5 1 1 1 2 2 1 2 2 SALMSON 2 3 2 4 2 4 1 25 68 5 C 2 4 2...
Page 60: ...6 2 5 2 6 Salmson 2 7 2 8 2 9 ATEX...
Page 62: ...8 2 9 7 2 9 8 2 9 9 3 3 1 3 2 3 3...
Page 63: ...9 6 Salmson 3 4 25 3 4 1 4 NEX 5 5 1 NEX...
Page 69: ...15 0 4 7 1 2 1 2 3 1 2 3 4 5 6 7 8 7 1 3 7 1 4 0 2 1...
Page 70: ...16 Parallel Angular 7 2 7 2 1 7 2 2 L 2 3 7 2 3...
Page 71: ...17 8 10 2 NPSHR NPSHA 7 2 4 3 3 10 0 35 2 0 7 7 3 230 400 400 400 690 690 60079 14...
Page 72: ...18 7 3 1 Y 230 400 400 690 7 3 2 U 7 3 3 U 3 7 3 4 7 4 850 dU dt 2500 ATEX NPSHR NPSHA...
Page 73: ...19 40 55 8 8 1 2 1 8 2 8 3 1 2 3 4 20 30 5 8 4 HMT P 100 SG 9 806 SG 7 1 4...
Page 74: ...20 125 P 0 5 P P 0 5 0 1 0 2 3 4 4 140 20 40 8 5 Salmson 9 9 1 9 2...
Page 86: ...32 11 12 12 1 12 1 1...
Page 89: ...35 13...