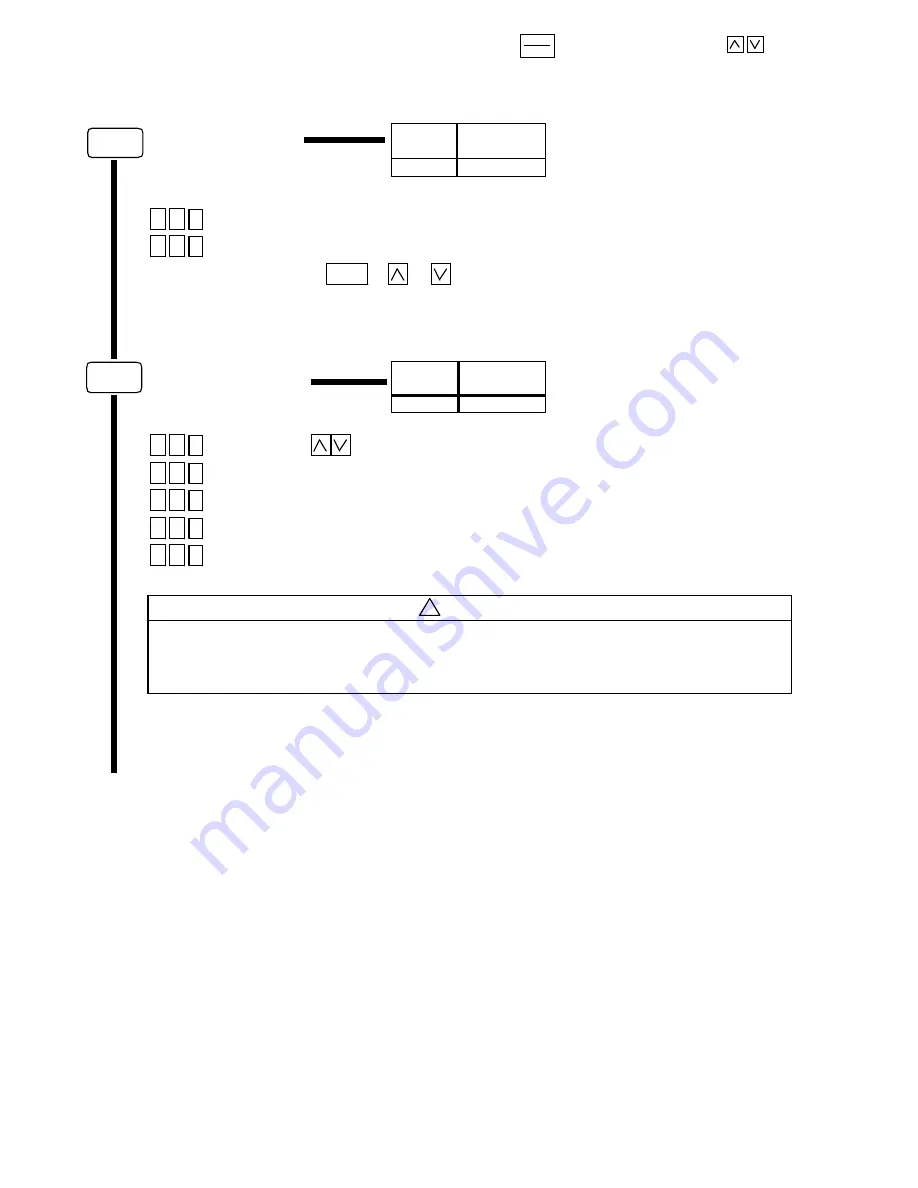
Change during operation: N = impossible,
Y* = possible (enabled by using ), Y= possible (enabled by using
)
-38-
FUNC
DATA
5-2
Details of Each Function
Data protection
Set data can be locked to prevent it from being changed by mistake when using the keypad panel:
0
Data can be changed.
1
Data is protected.
Data is changed when the
STOP
+
or
key are pressed simultaneously.
Frequency command
The following five values can be selected:
0
Key operation [
key
]
1
Voltage input (terminal 12) (0 to + 10Vdc)
2
Current input (terminal C1) (4 to 20mA)
3
Voltage input (terminal 12) + current input (terminal C1)
4
Analog setting (POT built in drive)
!
CAUTION
High-speed operation can be set by the drive easily. Carefully check the limit of the motor and
machine before changing the setting,
otherwise injuries could occur.
F00
Factory
setting
Change during
operation
0
N
F01
Factory
setting
Change during
operation
4
N