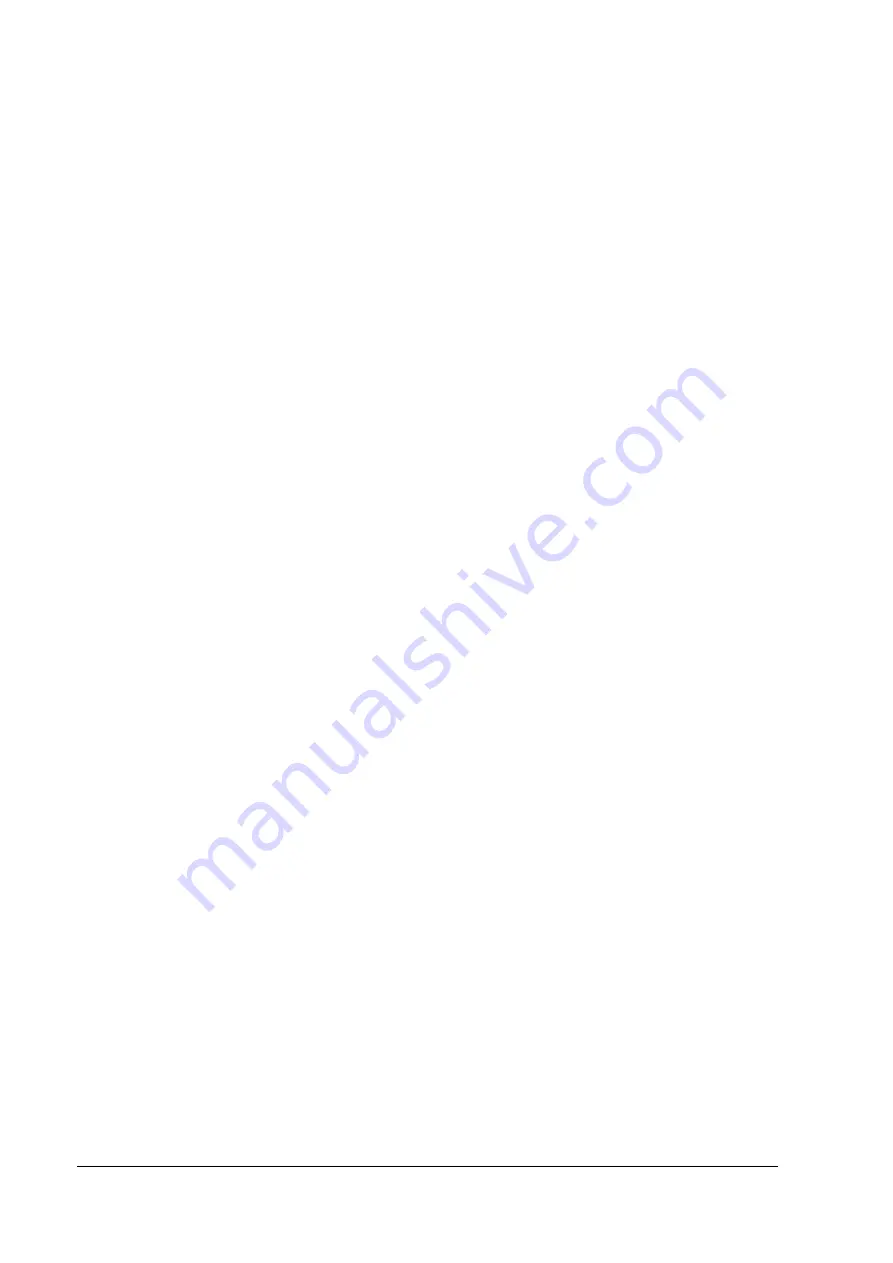
4
M0720-1 ver 3.4
CONTENTS
2.3 Mounting of cable/cables in weld power connectors, P6716/P6784 and P6726.........14
2.5 Mounting of water/air modules on tool changer or tool attachment .............................17
4.2.3 Cleaning and lubrication of TC (every 3rd month or 125,000 tool changes) .................. 32
4.2.4 Cleaning and lubrication of tool attachment (every 3rd month or 125,000 tool changes) 33
4.2.5 Cleaning and lubrication of TC (every 6
month or 250,000 tool changes) ................... 34
4.2.6 Cleaning and lubrication of tool attachment (every 6th month or 250,000 tool changes) 36
5 MANUAL UNLOCKING OF TOOL CHANGER ........................................................... 38
Summary of Contents for M0720-1
Page 2: ...2 M0720 1 ver 3 4 ...
Page 63: ...M0720 1 ver 3 4 63 ...
Page 64: ...64 M0720 1 ver 3 4 ...