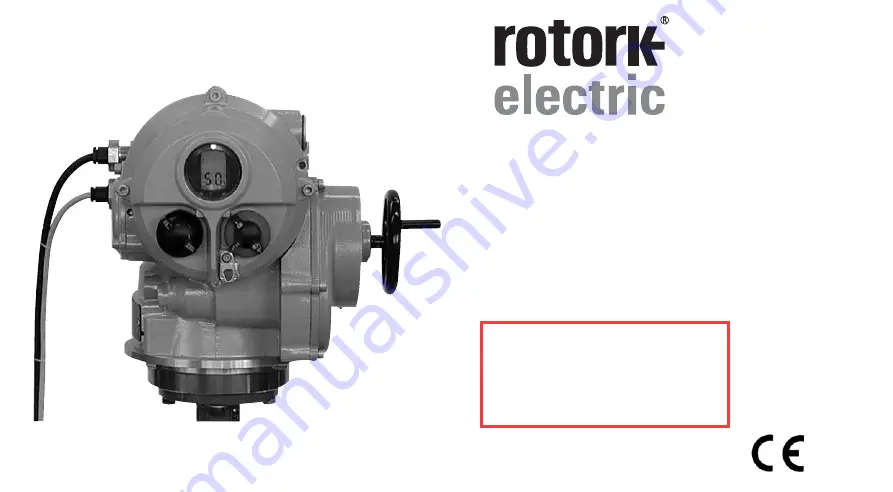
IQT Range
Installation and
Maintenance Instructions
Publication number E175E
Date of issue 07/04
Please ensure that this publication is thoroughly read and understood
For the latest information on
commissioning this actuator see
the addendum starting on p78.
Click