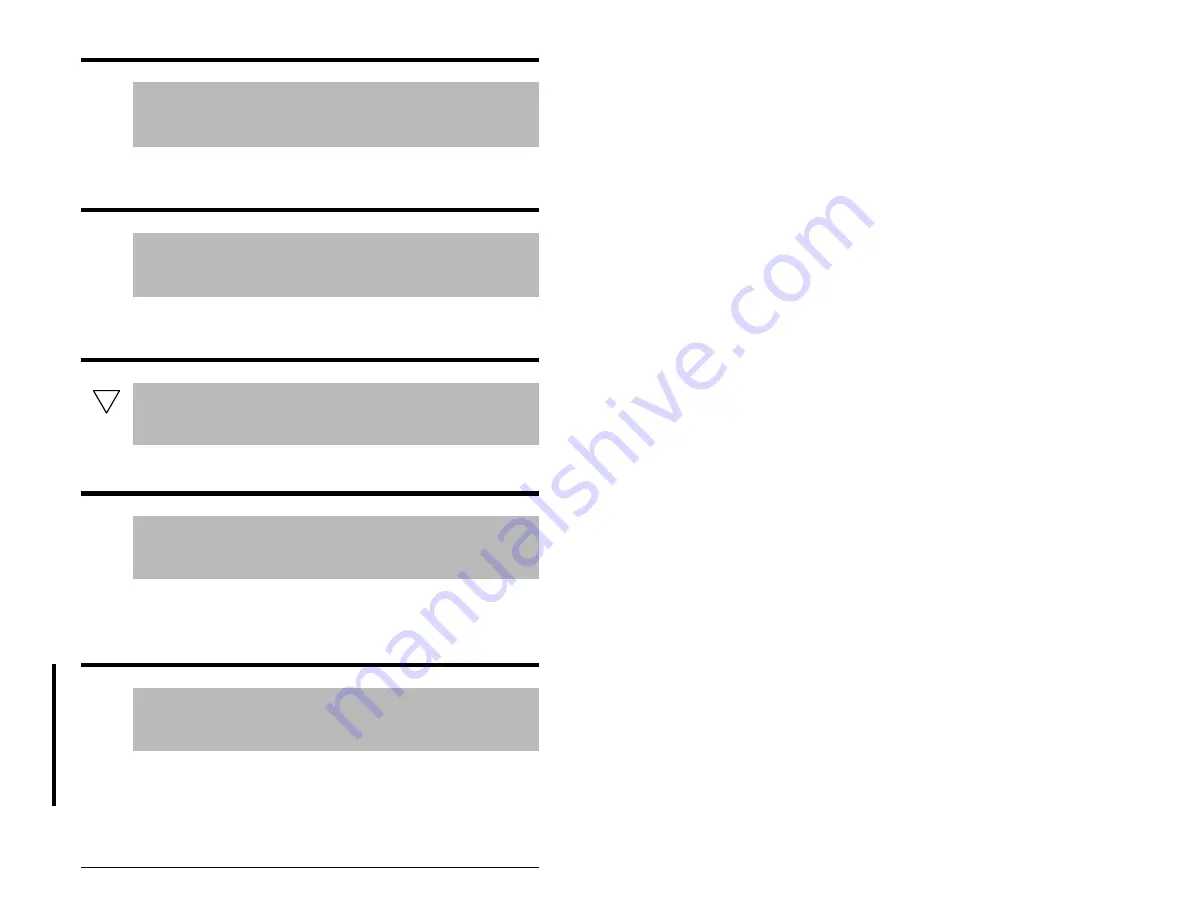
Parameter Descriptions
9-52
Displays the present operating temperature of the drive power
section.
Displays the current value of the counter when the counter is
enabled.
Displays the current value of the timer when the timer is enabled.
When Speed Reference (P038) is set to 6 = Stp Logic, this
parameter displays the current step of the StepLogic
TM
profile as
defined by parameters Stp Logic x (A140-A147).
Displays the current value of the motor torque current as measured
by the drive.
d024 Drive Temp
Range:
0 to 120 degree C
Default:
Read Only
See also:
N/A
d025 Counter Status
Range:
0 to 9999
Default:
Read Only
See also:
N/A
d026 Timer Status
Range:
0.0 to 9999 seconds
Default:
Read Only
See also:
N/A
32
d028 Stp Logic Status
Range:
0 to 7
Default:
Read Only
See also:
N/A
d029 Output Torque Current
Range:
0.00 to (Drive Rated Amps x 2)
Default:
Read Only
See also:
N/A
Summary of Contents for Reliance Electric MD65
Page 2: ...Instruction Manual MD65 AC Drive User Manual Version 2 0 D2 3519 2 ...
Page 7: ...IV MD60 AC Drive User Manual ...
Page 9: ...VI MD65 AC Drive User Manual ...
Page 11: ...VIII MD65 AC Drive User Manual ...
Page 13: ...1 2 MD65 AC Drive User Manual ...
Page 47: ...6 12 MD65 AC Drive User Manual ...
Page 119: ...10 12 MD65 AC Drive User Manual ...
Page 123: ...A 4 MD65 AC Drive User Manual ...
Page 129: ...B 6 MD65 AC Drive User Manual ...
Page 135: ...C 6 MD65 AC Drive User Manual ...
Page 139: ...D 4 MD60 AC Drive User Manual ...
Page 149: ...Accessories E 10 ...
Page 179: ...PID Set Up I 10 ...
Page 184: ......
Page 185: ......
Page 186: ......