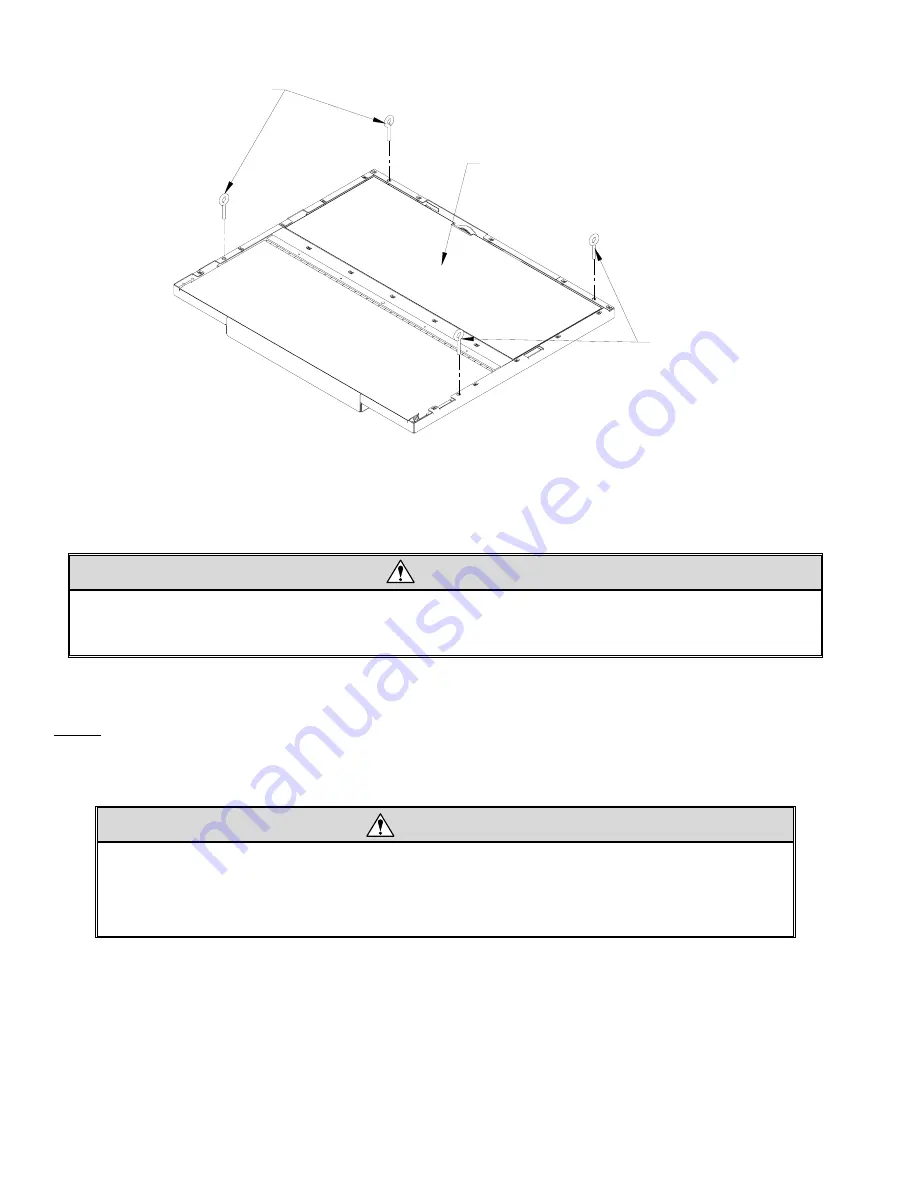
2 - 2
32DPF702.A
ACCESS PANEL
EYE BOLTS
EYE BOLTS
FIGURE 2-2: EYE BOLT LOCATIONS
f. Refer
to
Figure 2-3
. Rotate timing belt approximately 25-30 times in the direction shown in
Figure 2-3
until the tip of the ramp appears approximately 50mm out of the enclosure.
WARNING!
VERIFY THAT THE HINGED FLOOR IS PROPERLY LOCKED IN A RAISED POSITION BEFORE
ATTEMPTING TO INSTALL RAMP. THIS WILL HELP PREVENT INJURY WHILE INSTALLING THE RAMP.
g. Refer
to
Figure 2-3
. Use rod found under hinged floor to support and lock hinged floor in a raised posi-
tion.
NOTE:
Mechanical support of the ramp must be made using six provided attachment points located on three sides of
the ramp. Each attachment point uses two bolts, for a total of 12 bolts, that must be a minimum of 10 mm di-
ameter. Please use mounting hardware provided with the ramp in kit #39021.Please use mounting hardware
provided with the ramp in kit #39021.
WARNING!
DURING RAMP INSTALLATION, BE SURE THERE ARE NO GAPS BETWEEN THE TRAIN’S
RAMP FRAME BRACKET AND THE BOTTOM OF THE RAMP ENCLOSURE. IF GAPS EXIST, THE
RAMP WILL DEFORM WHEN MOUNTING BOLTS ARE TIGHTENED. FLEXURE EXC/-
1/25” (1mm) MAY CAUSE UNINTENDED OVER CURRENT CONDITIONS THAT WILL RESULT IN
RAMP MALFUNCTION. RAMP WILL NOT DEPLOY OR STOW AUTOMATICALLY.
h. Check for gaps between the train’s ramp frame bracket and the bottom of the ramp enclosure. Should
there be any gaps, insert spacers as needed (i.e. flat washers, etc.) to assure that the ramp enclosure
does not deform when bolts are tightened.
i. Refer
to
Figure 2-3
. Install 4 flat washers, spring washers and mounting bolts at rear end, two on each
side.
j. Refer
to
Figure 2-3
. Install 4 flat washers, spring washers and mounting bolts at mid section, two on each
side.
k. Refer
to
Figure 2-3
. Install 4 flat washers, spring washers and mounting bolts at front, two on each side.