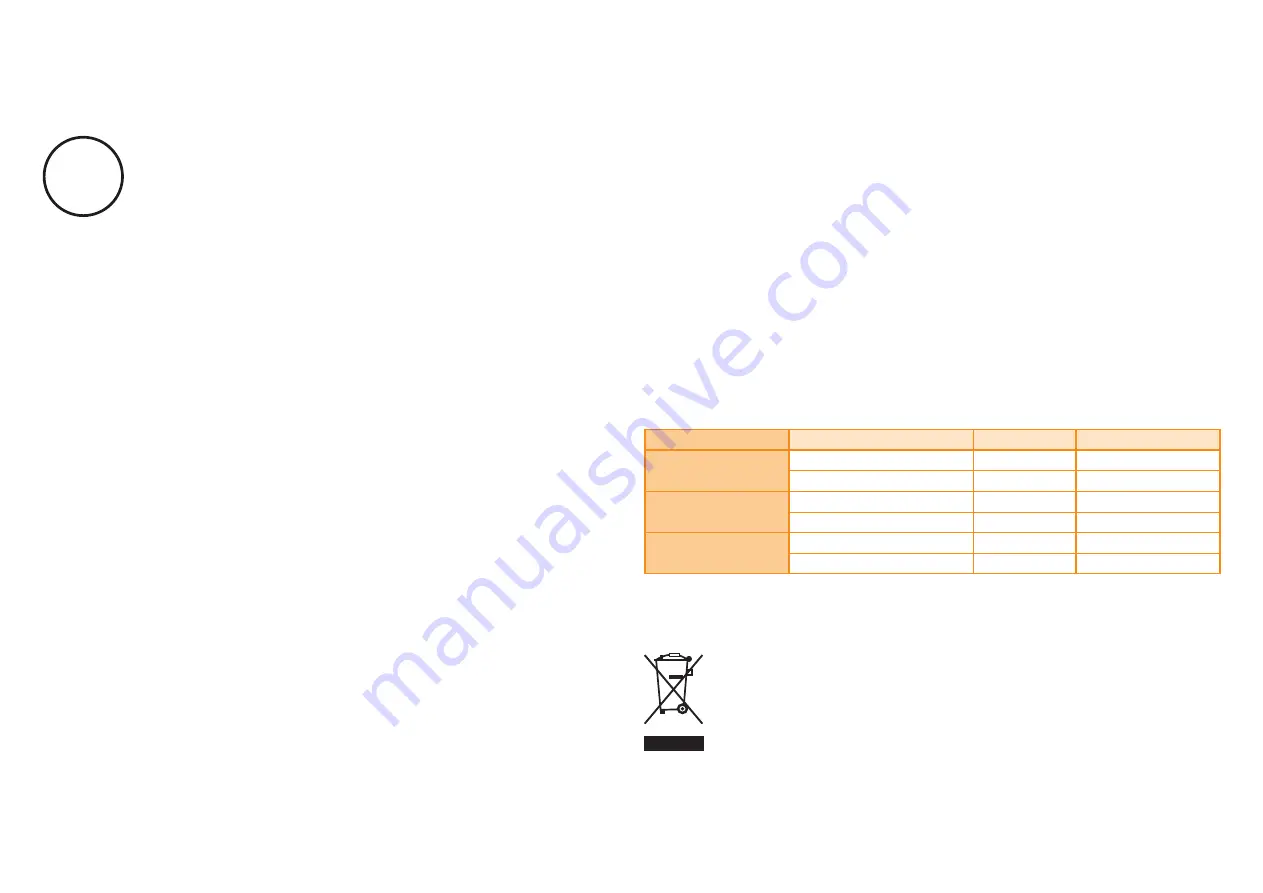
RESOLUTE FS with
BiSS
®
Safety
encoder system installation guide and safety manual
1
Original
instructions
Product compliance
This document is an installation guide and safety manual, which details the actions required for the safe
integration of the RESOLUTE FS (Functional Safety) with
BiSS
®
Safety
encoder system, as designated
by the SA or SL prefix in the part number, into a functionally safe system; this will be referred to as
RESOLUTE FS with BiSS Safety system in the below document.
The RESOLUTE FS with BiSS Safety system as defined below is suitable for use in a Category 3
performance level d (PLd) application in compliance with ISO 13849-1 and in a safety integrity level 2 (SIL2)
application in compliance with IEC 61508-1 and IEC 61800-5-2 when installed and operated in accordance
with the instructions defined.
Failure to follow the correct use instructions and heed the limitations may result in SIL2 and/or PLd
not being achieved and will invalidate the Functional Safety certification.
A copy of the RESOLUTE FS with BiSS Safety certificate is available from our website at
www.renishaw.com/productcompliance
C
Renishaw plc declares that RESOLUTE FS with BiSS Safety system complies with the applicable standards
and regulations. A copy of the EU declaration of conformity is available from our website at
www.renishaw.com/productcompliance
. For further details of FS compliance
FCC compliance
This device complies with part 15 of the FCC Rules. Operation is subject to the following two conditions:
(1) This device may not cause harmful interference, and (2) this device must accept any interference
received, including interference that may cause undesired operation.
The user is cautioned that any changes or modifications not expressly approved by Renishaw plc or
authorised representative could void the user’s authority to operate the equipment.
This equipment has been tested and found to comply with the limits for a Class A digital device,
pursuant to part 15 of the FCC Rules. These limits are designed to provide reasonable protection
against harmful interference when the equipment is operated in a commercial environment.
This equipment generates, uses, and can radiate radio frequency energy and, if not installed
and used in accordance with the instruction manual, may cause harmful interference to radio
communications. Operation of this equipment in a residential area is likely to cause harmful
interference in which case the user will be required to correct the interference at his own expense.
NOTE:
This unit was tested with shielded cables on the peripheral devices. Shielded cables must be
used with the unit to ensure compliance.
Further information
Further information relating to the RESOLUTE FS with BiSS Safety
encoder range can be found at
www.renishaw.com/safety-encoders
and is also available from your local Renishaw representative.
This document may not be copied or reproduced in whole or in part, or transferred to any other
media or language, by any means without the written prior permission of Renishaw.
The publication of material within this document does not imply freedom from the
patent rights of Renishaw plc.
SIL2
FUNCTIONAL
SAFETY
PLd
Patents
Features of Renishaw’s encoder systems and similar products are the subjects of the following
patents and patent applications:
CN1260551
DE10296644
GB2395005
JP4008356
US7499827
CN102197282
EP2350570
JP5480284
KR1630471
US8505210
CN102388295
EP2417423
JP5659220
KR1701535
US10132657
CN102460077
EP2438402
JP5755223
JP6074392
KR1851015
US20120072169
US6465773
EP1094302
JP5442174
US6481115
CN1293983
DE10297440
GB2397040
JP4813018
US7723639
CN1314511
EP1469969
EP2390045
JP5002559
US8466943
US8987633
JP4423196
US7367128
Disclaimer
RENISHAW HAS MADE CONSIDERABLE EFFORTS TO ENSURE THE CONTENT OF THIS DOCUMENT
IS CORRECT AT THE DATE OF PUBLICATION BUT MAKES NO WARRANTIES OR REPRESENTATIONS
REGARDING THE CONTENT. RENISHAW EXCLUDES LIABILITY, HOWSOEVER ARISING, FOR ANY
INACCURACIES IN THIS DOCUMENT.
The packaging of our products contains the following materials and can be recycled.
Packaging Component
Material
ISO 11469
Recycling Guidance
Outer box
Cardboard
Not applicable
Recyclable
Polypropylene
PP
Recyclable
Inserts
Low Density Polyethylene Foam LDPE
Recyclable
Cardboard
Not applicable
Recyclable
Bags
High Density Polyethylene Bag
HDPE
Recyclable
Metallised Polyethylene
PE
Recyclable
REACH regulation
Information required by Article 33(1) of Regulation (EC) No. 1907/2006 (‘REACH’) relating to products con-
taining substances of very high concern (SVHCs) is available at
The use of this symbol on Renishaw products and/or accompanying documentation indicates that the
product should not be mixed with general household waste upon disposal. It is the responsibility of the end
user to dispose of this product at a designated collection point for waste electrical and electronic equipment
(WEEE) to enable reuse or recycling. Correct disposal of this product will help to save valuable resources
and prevent potential negative effects on the environment. For more information, please contact your local
waste disposal service or Renishaw distributor.