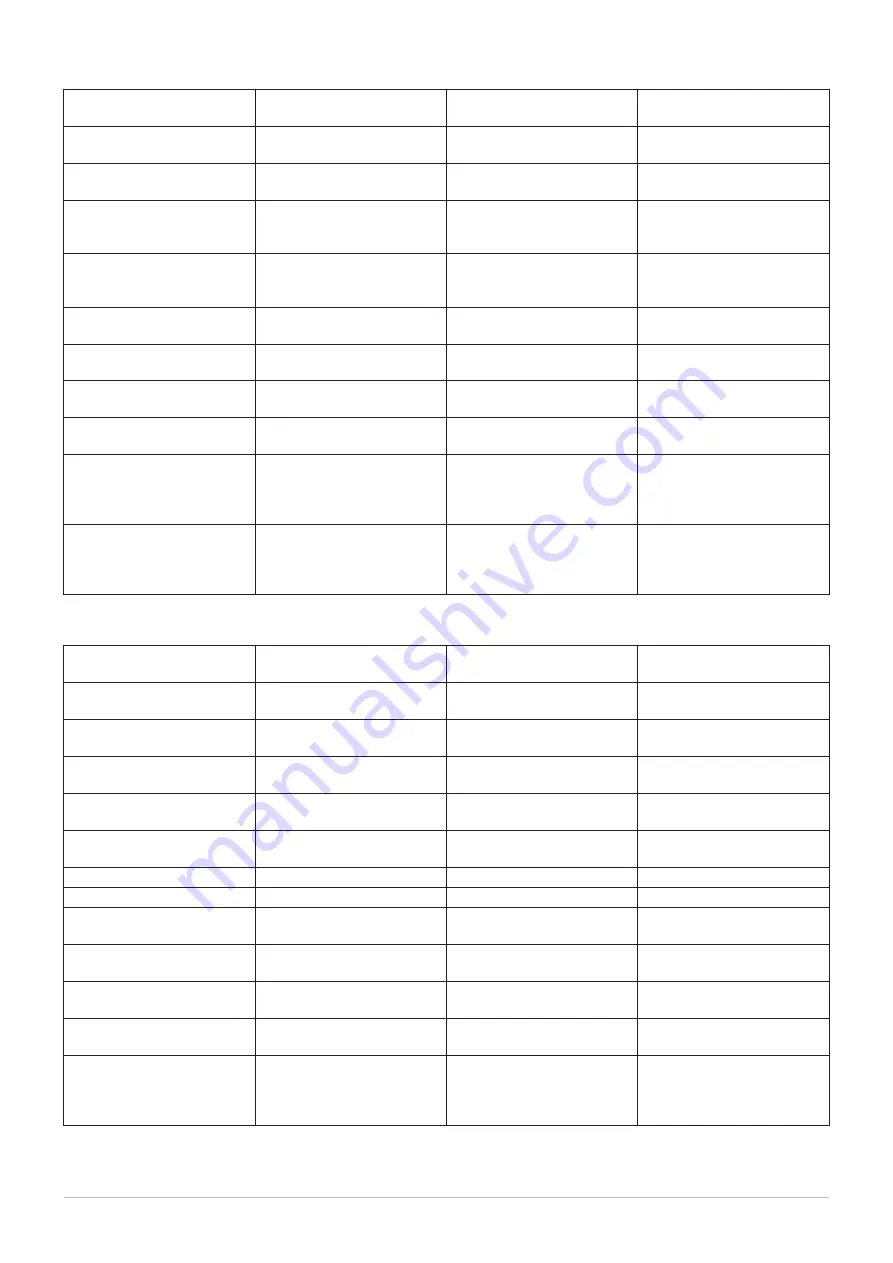
CM181
Zone RU present
Presense of Room Unit in this
zone
0 No
1 Yes
CM190
Zone Troom setpoint
Wished room temperature
setpoint of the zone
0 °C 50 °C
CM191
Zone Troom setpoint
Wished room temperature
setpoint of the zone
0 °C 50 °C
CM200
ZoneCurrentHeatMode
Displaying current operating
mode of the zone
0 Standby
1 Heating
2 Cooling
CM201
ZoneCurrentHeatMode
Displaying current operating
mode of the zone
0 Standby
1 Heating
2 Cooling
CM210
ZoneTout temp
Current outdoor temperature
of the zone
-70 °C 70 °C
CM211
ZoneTout temp
Current outdoor temperature
of the zone
-70 °C 70 °C
CM240
Zone Tout connected
Outdoor temperature sensor
is connected to the zone
0 No
1 Yes
CM241
Zone Tout connected
Outdoor temperature sensor
is connected to the zone
0 No
1 Yes
CM280
ZoneRTC TcalcRoomStp
Internal room temperature
setpoint calculated by the
room temperature controller of
the zone
-60 °C 60 °C
CM281
ZoneRTC TcalcRoomStp
Internal room temperature
setpoint calculated by the
room temperature controller of
the zone
-60 °C 60 °C
Tab.58 Zone High Temperatur
Zone over heating
Active over heating of the
zone
0 Off
1 On
Zone over heating
Active over heating of the
zone
0 Off
1 On
CM030
Zone RoomTemperature
Measure of the room
temperature of the zone
0 °C 50 °C
CM031
Zone RoomTemperature
Measure of the room
temperature of the zone
0 °C 50 °C
CM050
Status Pump zone
Status of the Pump of zone
0 No
1 Yes
CM051
Status Pump zone
Status of the Pump of zone
0 No
1 Yes
CM060
ZonePumpSpeed
Current Pump speed of zone
0 % 100 %
CM061
ZonePumpSpeed
Current Pump speed of zone
0 % 100 %
CM070
Zone Tflow Setpoint
Current Flow temperature
setpoint of zone
0 °C 150 °C
CM071
Zone Tflow Setpoint
Current Flow temperature
setpoint of zone
0 °C 150 °C
CM110
ZoneTRoomUnit setp
Room Unit temperature
setpoint of zone
0 °C 35 °C
CM111
ZoneTRoomUnit setp
Room Unit temperature
setpoint of zone
0 °C 35 °C
CM120
ZoneCurrentMode
Zone Current Mode
0 Scheduling
1 Manual
2 Antifrost
3 Temporary
9 Settings
7717201 - v03 - 25062019
MID _HMI T-control - Gas 120 ACE
71