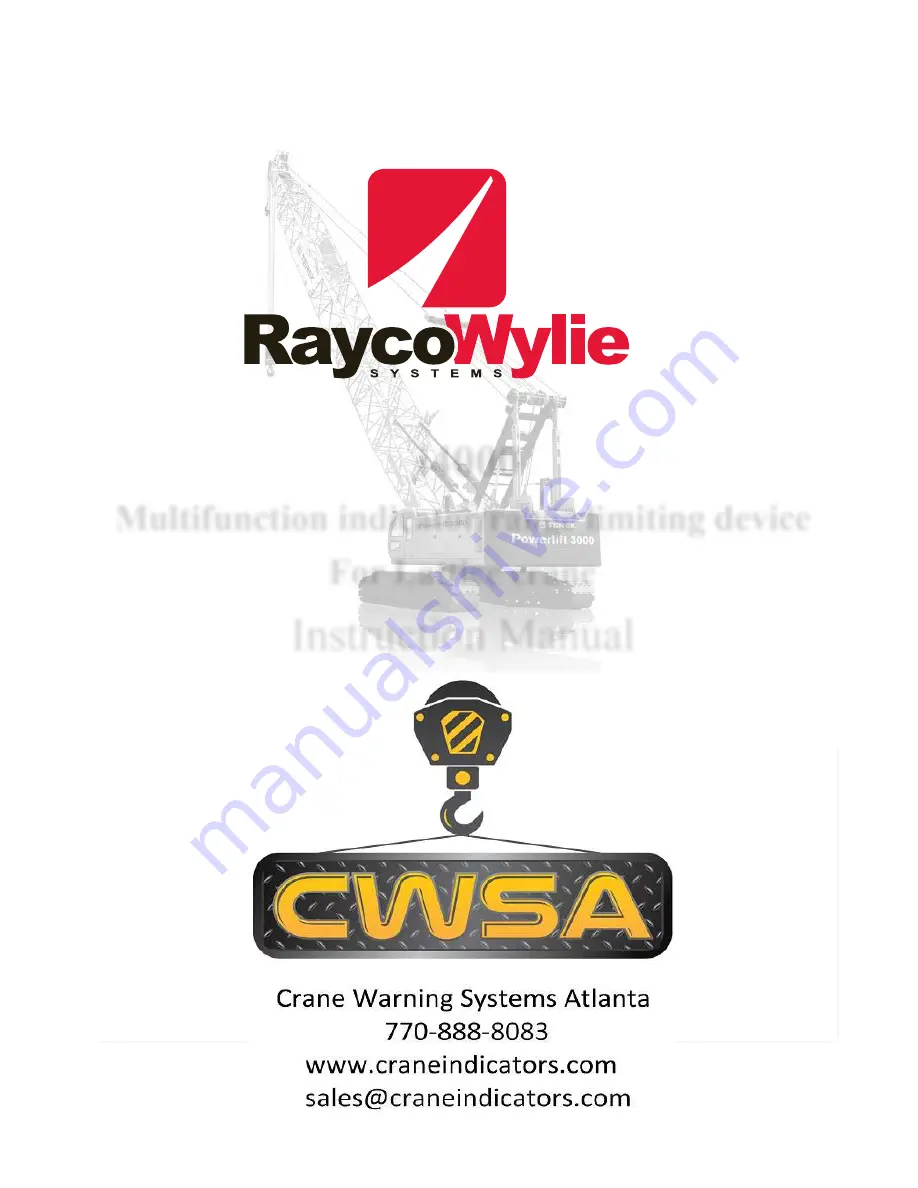
Instruction Manual
i4000
Multifunction indicator/range limiting device
For Lattice crane
Copyright © 2018
RaycoWylie Systems
All rights reserved.
Wylie Systems
(Rayco Technology Group)
201 Prospect Avenue
Suite 106 - Box 159
Hagerstown, MD 21742
USA
Tel: +1 888-252-1957
Fax: +1 (418) 266-6610
Rayco Electronic Systems
(Rayco Technology Group)
2440 Dalton Avenue
Ste-Foy, Qc
CANADA
G1P 3X1
Tel: +1 (418) 266-6600
Fax: +1 (418) 266-6610
Wylie Systems
(Rayco Technology Group)
Drury Lane
St-Leonards on Sea, East Sussex
ENGLAND
TN38 9BA
Tel: +44 (0) 1424-421235
Fax: +44 (0) 1424-433760
55M4000EBE00 Rev C
Crane Warning Systems Atlanta
6175 Hickory Flat Hwy Suite #110-376
Canton, GA 30115
877-672-2951 Toll Free
678-261-1438 fax
www.craneindicators.com
Summary of Contents for i4000
Page 2: ......
Page 3: ......
Page 4: ......
Page 6: ......
Page 8: ......
Page 12: ......
Page 17: ...17 i4000 Lattice Crane Instruction Manual 55M4000EBE00 Rev C 1 6 Overall scheme ...
Page 28: ......
Page 30: ......
Page 57: ......
Page 71: ...71 i4000 Lattice Crane Instruction Manual 55M4000EBE00 Rev C Notes ...
Page 72: ......