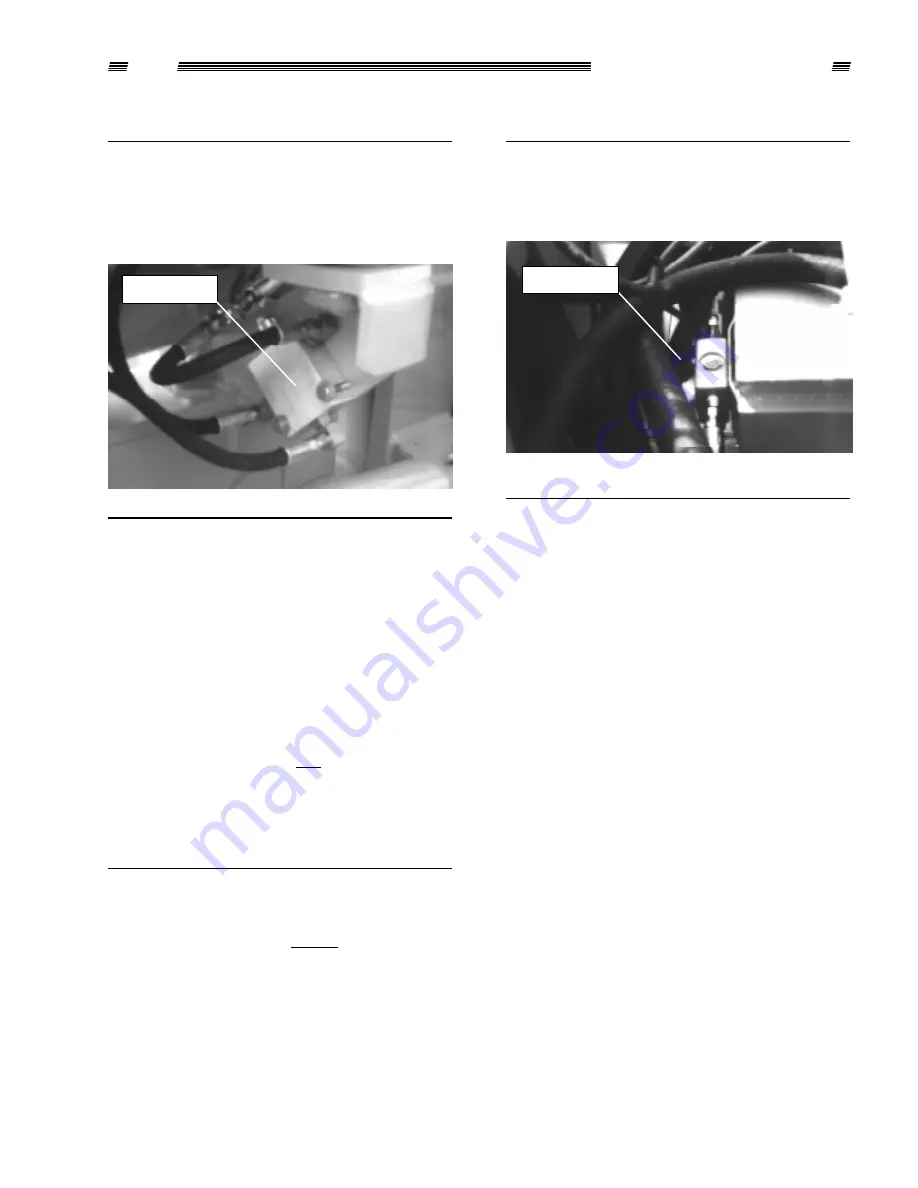
Copyright © 1998 Rayco - All Rights Reserved
Printed in U.S.A.
71
RG 1672 DXH DIESEL SUPER CUTTER
TM
RAYCO
®
T
ROUBLE
-S
HOOTING
Solution for Faulty Cylinder Piston Seal
The hydraulic cylinder seals should be replaced.
Hydraulic cylinder rebuild kits are available from
RAYCO or your RAYCO dealer.
C. Problem
- Over center Valve Dirty or
Misadjusted
Solution
1. Disassemble over - center valve.
2. Clean ball/spring assembly with compressed air
or a clean cloth, and make sure ball seats
without obstruction.
3. Reassemble.
If problem persists, check adjustment.
Symptom
- Cutting Boom Swings
Sideways Uncontrolled
A.
Problem
- Cylinder rod seal
leaking
If when operated, cylinder loses fluid around rod, rod
seal is leaking.
Solution for Faulty Cylinder Rod Seal
Replace cylinder rod seal, using kit available from
your RAYCO distributor.
B.
Problem
- Cylinder piston seals
leaking
To determine if cylinder piston seals are leaking,
perform a hydraulic pressure check of the cylin-
ders circuit. (Refer to chart on preceding page.)
Solution for Faulty Cylinder Piston Seal
The hydraulic cylinder seals should be replaced.
Hydraulic cylinder rebuild kits are available from
RAYCO or your RAYCO dealer.
C. Problem
- Dual Pilot Check Valve Dirty
Solution
1. Using a screwdriver and a 7/8" hex socket,
remove ball/spring assembly on side (of dual
pilot check valve) that exhausts whenever
symptom appears.
2. Clean ball/spring assembly with compressed air
or a clean cloth, and make sure ball seats
without obstruction.
3. Reassemble.
Check
Check
Summary of Contents for SUPER CUTTER RG 1672 DXH DIESEL
Page 4: ......