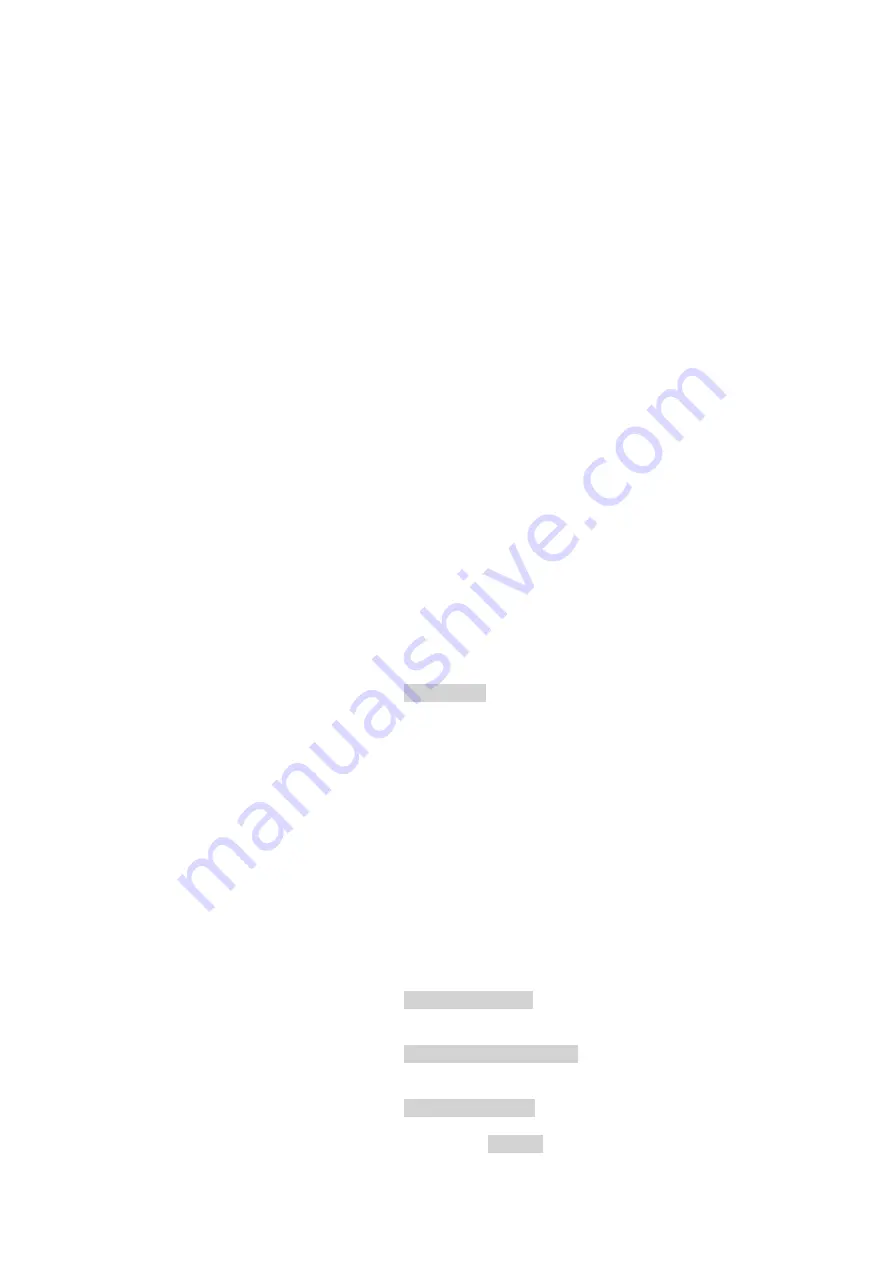
Operating Instructions D50+ | P50+ | SHERAprint 50
27
│
96
Rapid Shape GmbH
│
DOCR000438
4.1.3
Aligning the Machine
To ensure proper operation, the machine needs to be aligned in a
horizontal position for operation. Uneven floors can be levelled out
using stainless steel shims included in delivery.
To quickly align the machine, the shims can be placed under the
castors on the machine. The shims can also be fitted to the machine if
it is to be used in the same location for a prolonged period of
operation.
Quick Alignment
To align the machine quickly, please proceed as follows:
1.
Prerequisite: You have established that the machine is not
aligned in a horizontal position. At least one air bubble inside a
spirit level is outside the respective reading ring.
2.
Take the shims in your hands. There are 1 and 2 mm thick shims
included in delivery.
3.
Depending on the extent to which the machine is out of
alignment, take a shim with the appropriate thickness and slide
it under the respective castor to gradually align the machine.
Repeat the procedure on the other castors if necessary, until the
corresponding air bubble is inside the respective reading ring
and the machine is level.
Long-Term Alignment
Recommendation: Use a team of two to align the machine. For the
long-term alignment of the machine, please proceed as follows:
1.
Prerequisite: You have already aligned the machine using shims
under the castors (see above) and now you want to fit them to
the machine.
2.
Wear protective gloves on your hands.
3.
Open the upper hood.
4.
Preparations: Remove the collection basket and place it on a
paper towel.
Caution! Watch out for material dripping from the
collection basket. Hold the basket at a slight angle towards the
back to prevent material from leaking out. Also place a paper
towel directly underneath the basket opening.
5.
Ensure that the build platform, knife drip guard and knife, if
inserted, are clean and firmly affixed in place. If liquid material
is found adhering to the components, remove them first from the
machine before removing the material reservoir.
6.
Pull the reservoir out of the machine. To do so, press the
reservoir down slightly and then pull it out of the machine. Store
the reservoir in a reservoir box.
7.
Now switch the machine off.
→
Chapter 8.1.2
8.
Push the machine off the shims. Place the shims to one side so
that you can place them back in the corrects positions
afterwards.
9.
Push the machine back to its previous position.
10.
Removing the frame: Loosen and remove the frame fixing screws
on the lower left-hand and right-hand sides. Remove the frame
elements from the machine frame and set them aside.
11.
Removing the bottom hood: Loosen and remove the fixing
screws on the bottom hood of the machine. Remove the hood
from the machine frame and set it aside.
12.
Start with one castor: Now loosen the four locking nuts on the
castor (do not remove them completely).
13.
One person: Carefully tilt the machine to one side slightly so
that the weight is taken off the castor. The second person: Slid
the shim(s) with the long side between the castor and the