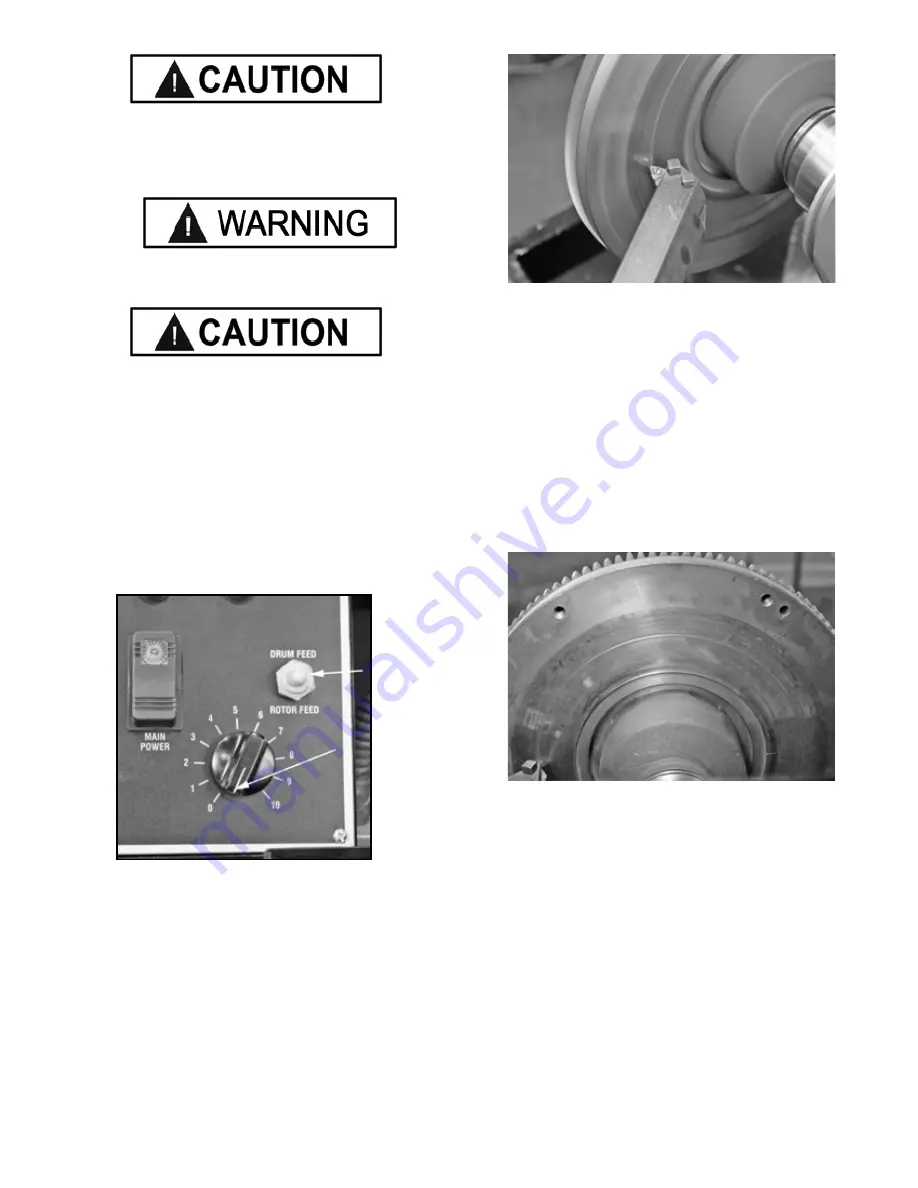
36
ENSURE THAT THE CUTTING TIP IS CLEAR OF THE
FLYWHEEL PRIOR TO TURNING ON THE SPINDLE
MOTOR.
MAKE SURE THE DRUM / ROTOR CROSS FEED
SWITCH IS IN THE NEUTRAL POSITION.
K
EEP HANDS clear of moving parts at all times. Keep
hair, loose clothing, neckties, shop rags, jewelry, fingers,
and all parts of body away from moving parts. Always
wear safety glasses or a face shield. Cutting an exposed
surface such as a brake drum, rotor or flywheel will pro-
duce flying chips and debris.
9.. Move the Feed Selector Switch to the Neutral
position.
10. Set the speed feed dial to 0.
11. Turn on the Main Spindle Power Switch.
12. Rotate the Spindle Feed Hand Wheel clock wise until
the Cutter begins to cut a shallow scratch cut in the
flywheel.
13. Back off the Cutter by turning the Spindle Feed Hand
Wheel Clock wise.
14. Turn off the Main Spindle Power.
15. Examine the scratch cut making sure it is uniform
around the entire circumference of the flywheel. If the
scratch cut appears to be deeper on one side of the fly-
wheel and not a uniform depth, remove the flywheel from
the arbor, check the mounting adapters and arbor for
nicks, burrs, or chips, remount the flywheel, and repeat the
process.
Once the flywheel is determined to be mounted properly
and the scratch cut is good, continue on the machining
the Flywheel in Step 18.
Summary of Contents for RL-8500
Page 10: ...10...
Page 44: ...44 MOTORFEED ASSEMBLY 39...
Page 45: ...45 Motor Feed Assembly...
Page 46: ...46 Drum Feed Assembly...
Page 47: ...47 Drum Feed Assembly...
Page 48: ...48...
Page 50: ...50 MAIN MOTOR 39 41...
Page 52: ...52...