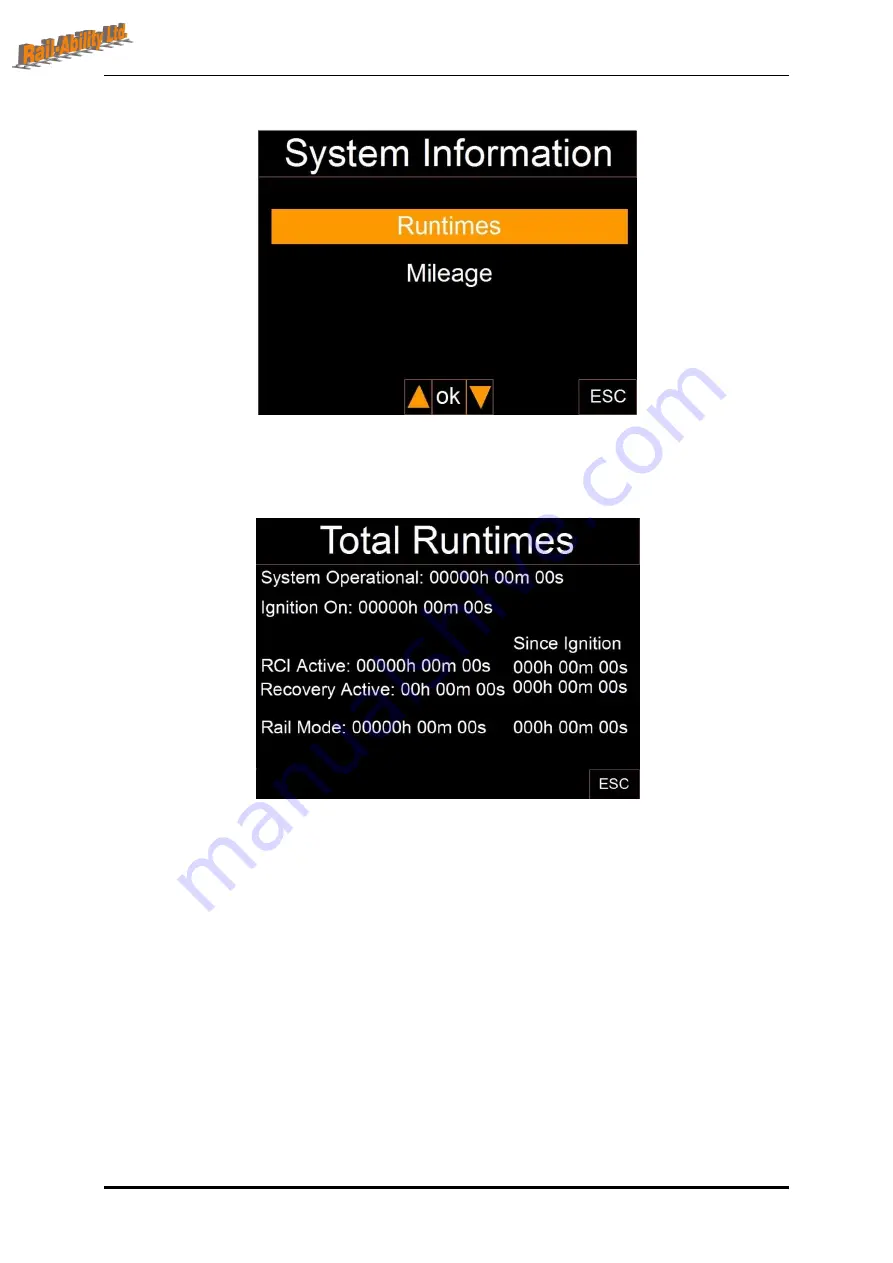
DRAFT
Operator’s Manual
© Copyright 2014 - Rail-Ability Limited
Page
41
of
64
Conversion
12.5.15 System Information
Figure 28 - System Information Page
Having accessed the “System Information” option from the main menu, the screen will display as
shown above. Use the F4 key for “ESC” to return to the main menu page.
Figure 29 - Runtimes Page
The “Runtimes” option of the “System Information” menu will display the page above. The times are
updated constantly, and apart from the “since ignition” values are retained in the memory of the
system even after shutdown.
The “RCI Active” values are in reference to the Prolec system components, the “Recovery Active”
values are increased only with the operation of the recovery pumps, and “Rail Mode” time is
incremented only when both rail axles are considered fully deployed by the system.