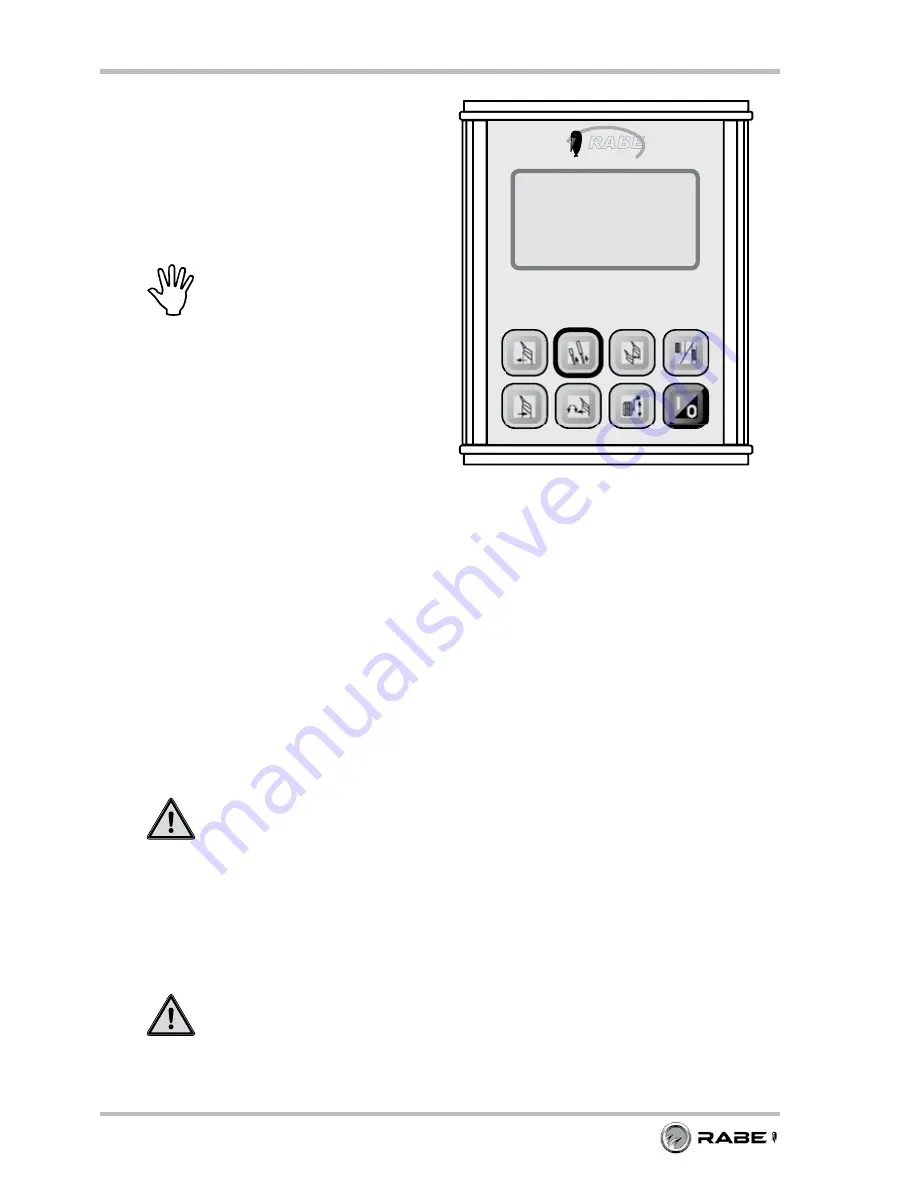
RABE
PAVOtronic
80
PAVO V140 / VHA 140
09.2011
16.0 Maintenance
16.1 Safety instructions - Maintenance and repair
WARNING
Risk of accident due to pinching or crushing while performing maintenance work.
Turn off the engine of the tractor and take the key out of the ignition.
Only perform work when the implement is in a safe condition and has been secured to
prevent it from dropping and rolling away.
Use all provided supports.
During all work, wear work gloves, the prescribed working clothing and protective equipment.
Always disconnect the power before starting any work on the electrical system.
Before performing welding work, disconnect all power connections to the tractor.
Secure the implement to prevent unauthorised start-up while such work is in progress.
Risk of injury due to heavy components.
When handling heavy components, use suitable lifting devices or seek the assistance
of a second person.
•
•
•
•
•
•
•
Maintenance
PAVOtronic terminal
PAVOtronic with a damp cloth, if
necessary a mild household cleaner
may be used in addition.
NOtE
Store the PAVOtronic such that it is
protected from moisture and cold.
Do not store the PavOtronic in
the open.
►
•
Fig. 111: PAVOtronic
Summary of Contents for Pavo V 140
Page 1: ...EN Operating Instructions Serial no Pavo V 140 PAVO VHA 140 with PAVOtronic Series 1...
Page 4: ...PAVO V140 VHA 140 09 2011...
Page 18: ...18 PAVO V140 VHA 140 09 2011...
Page 99: ...99 PAVO V140 VHA 140 09 2011 EU Declaration of Conformity Declaration of Conformity...
Page 100: ...100 PAVO V140 VHA 140 09 2011...