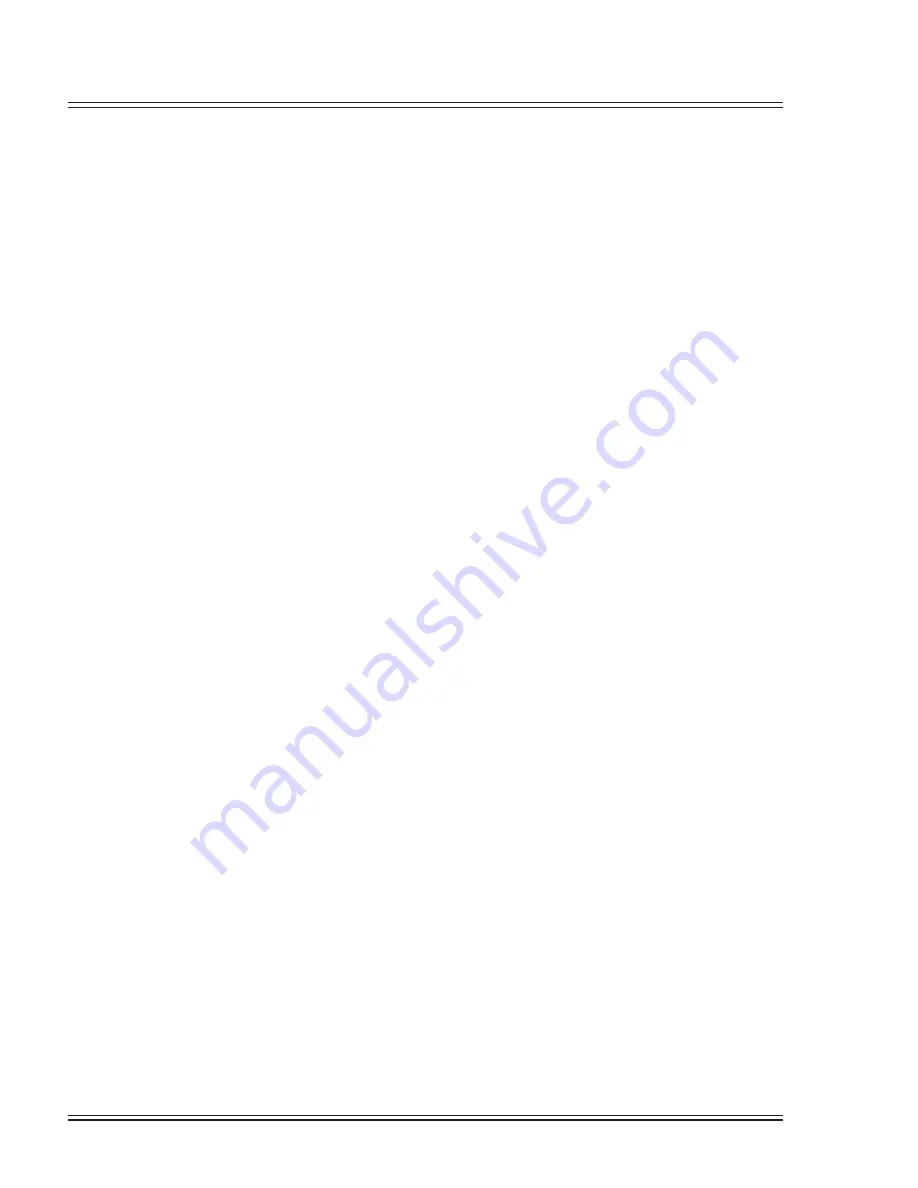
Addendum 2 - Shell /Tube Heat Exchanger Install and Service Recommendations
132
Quincy Compressor-QSI
®
Recommendations:
Replace gaskets when removing end castings. It is recommended that gaskets be soaked in oil to prevent corrosion
and ensure a tight seal.
Salt water should not be used in standard models. Use salt water in special models having 90/10 copper-nickel tubes,
tube sheets*, bronze bonnets and zinc anodes on the tube side. Brackish water or other corrosive fluids may require
special materials of construction.
When zinc anodes are used for a particular application, they should be inspected two weeks after initial startup.
At this time, by visual inspection of the anode, determination of future inspection intervals can be made, based on the
actual corrosion rate of the zinc metal.
The zinc anodes must be replaced when 70% of the zinc volume has been consumed.
It may be necessary to drain the water chambers of the exchanger to protect it from damage by freezing temperatures.
Drains are provided in most standard models.
The oil chamber of the exchanger may become filled with sludge accumulation and require cleaning. It is recommend
-
ed that the unit be flooded with a commercial solvent and left to soak for one-half hour. Back flowing with the solvent
or regular oil will remove most sludge. Repeated soaking and back flowing may be required, depending on the degree
of sludge build-up.
It may be necessary to clean the inside of the cooling tubes to remove any contamination and/or scale build up. It is
recommended that a fifty-fifty percent solution of inhibited muriatic acid and water may be used. For severe problems,
the use of a brush through the tubes may be of some help. Be sure to use a soft bristled brush to prevent scouring the
tube surface causing accelerated corrosion. Upon completion of cleaning, be certain that all chemicals are removed
from the shell side and the tube side before the heat exchanger is placed into service.
*Available on C/CA Series models only.
Summary of Contents for QSI Series
Page 2: ......
Page 7: ...Section I General Quincy Compressor QSI 5 MODEL IDENTIFICATION...
Page 62: ...Section IV Operating Procedures 60 Quincy Compressor QSI 1 Week Timer 2 Remaining Running Time...
Page 79: ...Section IV Operating Procedures Quincy Compressor QSI 77...