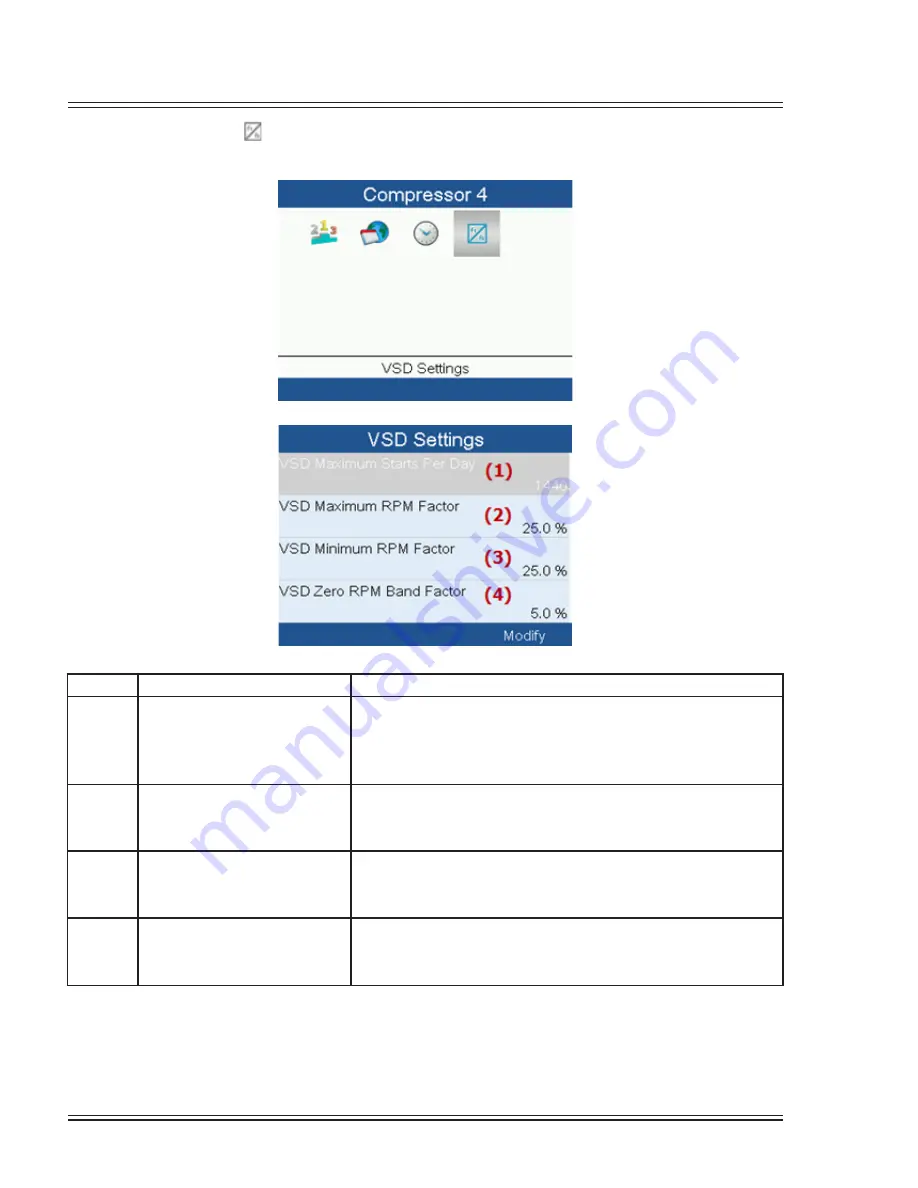
Section IV - Operating Procedures
80
Quincy Compressor-QSI
®
•
The final item is “VSD” . This option is for any slave compressor which is running on VSD. When they are
running as slaves, they would be seen as fixed speed compressors. To check its settings, Use scroll keys and move
cursor to VSD and press Enter key. Following screen will appear:
Number
Timers
Description
1
VSD Maximum Starts Per Day
The second up to sixth VSD compressor will be seen as a
Fixed Speed compressor running at optimal/ maximum speed.
Since these VSD’s are seen as fixed speed compressors, a
‘Number of starts per day’ is required for the regulation.
2
VSD Maximum RPM Factor
Percentage of Control VSD Speed; required for the decision to
start/load/unload and stop fixed speed and maximum speed
VSD’s.
3
VSD Minimum RPM Factor
Percentage of Control VSD Speed; required for the
decision to start/load/unload and stop fixed speed and
maximum speed VSD’s.
4
VSD Zero RPM Band Factor
Percentage multiplied with the ‘Minimum Speed’ to
decide that the Control VSD can be considered as
stopped.
Summary of Contents for QSI Series
Page 2: ......
Page 7: ...Section I General Quincy Compressor QSI 5 MODEL IDENTIFICATION...
Page 62: ...Section IV Operating Procedures 60 Quincy Compressor QSI 1 Week Timer 2 Remaining Running Time...
Page 79: ...Section IV Operating Procedures Quincy Compressor QSI 77...