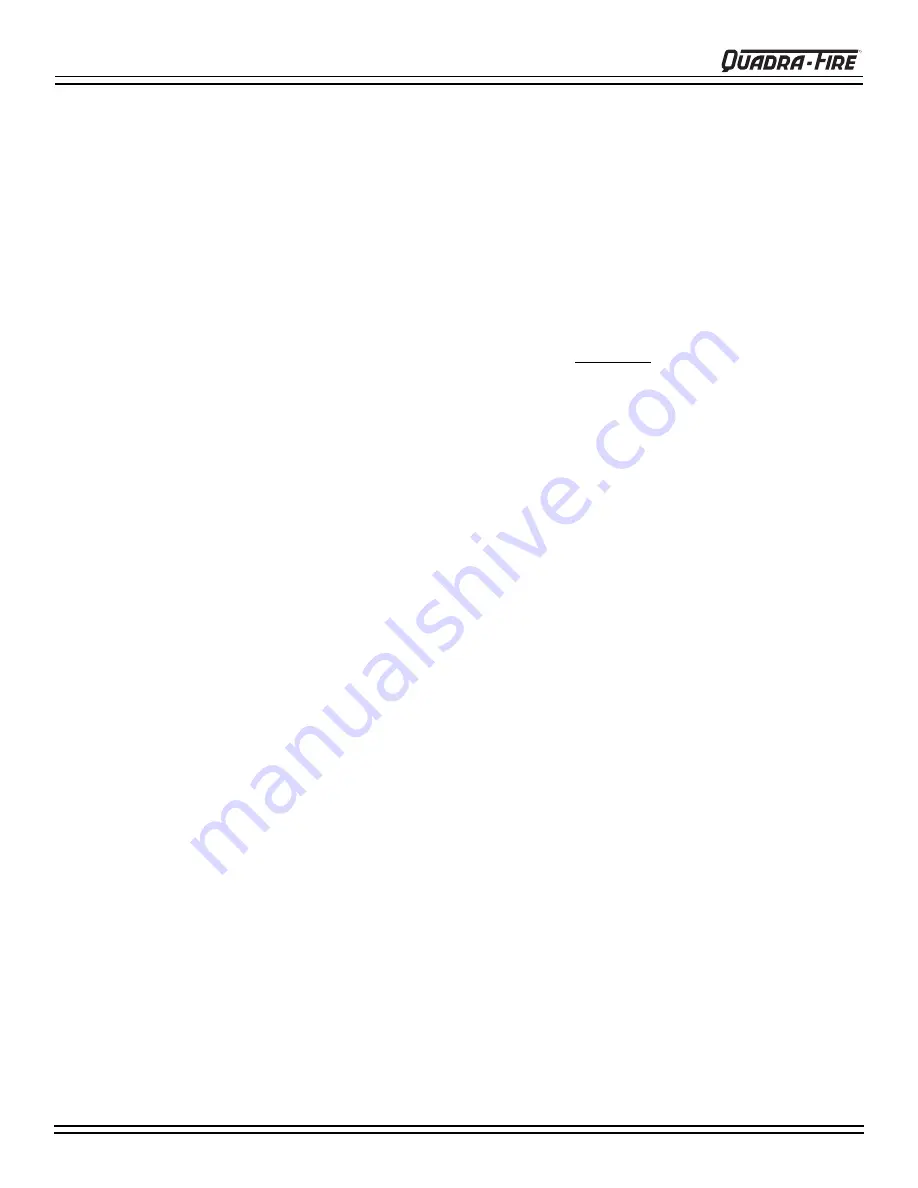
Page 7
March 27, 2008
4100-I ACT WOOD INSERT
250-7201 Rev D
R
IF INSTALLING THIS MODEL TO A MASONRY CHIMNEY,
ALWAYS BE SURE THE CHIMNEY IS IN GOOD CONDITION
AND THAT IT MEETS THE MINIMUM STANDARDS OF THE
NATIONAL FIRE PROTECTION ASSOCIATION (NFPA)
STANDARD 211. A FACTORY BUILT CHIMNEY MUST BE
6 INCH (152mm) UL103 HT AND ULC S629.
THIS APPLIANCE IS MADE WITH A 6 INCH (152mm) DIAM-
ETER CHIMNEY CONNECTOR AS THE FLUE COLLAR ON
THE UNIT. CHANGING THE DIAMETER OF THE CHIMNEY
CAN AFFECT DRAFT AND CAUSE POOR PERFOR-
MANCE. IT IS NOT RECOMMENDED TO USE OFFSETS
OR ELBOWS AT ALTITUDES ABOVE 4000 FEET ABOVE
SEA LEVEL OR WHEN THERE ARE OTHER FACTORS
THAT AFFECT FLUE DRAFT. SEE PAGE 5.
CAUTION: THIS APPLIANCE IS HOT WHILE IN OPERA-
TION AND MAY REMAIN SO UP TO 40 MINUTES OR
LONGER AFTER THERE IS NO FUEL IN THE FIREBOX.
IF THIS APPLIANCE IS IN A HIGH TRAFFIC AREA OR
CHILDREN MAY BE NEAR, IT IS RECOMMENDED THAT
YOU PURCHASE A DECORATIVE BARRIER TO GO IN
FRONT OF THE APPLIANCE.
CALCULATING ALTERNATE FLOOR
PROTECTION MATERIAL
Thermal Conductivity: k value
The k value indicates the amount of heat (in BTU’s) that will fl ow
in 1 hour through 1 square foot of a uniform material 1 inch thick
for each degree (F) of temperature difference from one side of
the material to the other. The LOWER the k factor means less
heat is being conducted through the non-combustible material to
the combustible material beneath it. The k value of a material
must be equal or smaller then the required k value to be accept-
able.
(BTU)
(inch)
(foot
2
(hour) (
o
F)
Thermal Resistance: R value
The R value is a measure of a material’s resisteance to heat
transfer. R value is convenient when more than one material is
used since you can add the R values together, whereas you can
not do this for k value. The HIGHER the R factor means less
heat is being conducted through the non-combustible material to
the combustible material beneath it. The R value of a material
must be equal or larger then the required R value to be accept-
able.
Converting k to R:
Divide 1 by k and multiply the results times the thickness in inch-
es of the material.
R = 1/k x inches of thickness
Converting R to k:
Divide the inches of thickness by R.
k = inches of thickness/R
Calculations:
Example: Floor protection requires k value of 0.84 and 3/4 inch
thick.
Alternative material has a k value of 0.6 and is 3/4 inch thick.
Divide 0.6 by .75 = k value of 0.80. This k value is smaller than
0.84 and therefore is acceptable.
GENERAL INSTALLATION PROCEDURE
•
DO NOT CONNECT THIS UNIT TO A CHIMNEY
FLUE SERVING ANOTHER APPLIANCE.
•
Install liner, if required, for your chosen installation.
•
Attach metal warning plate to the back of the fi replace
with screws or nails.
•
Set appliance on the hearth (See Hearth Requirements
page 5
and Support Kit information on
page 16.
)
•
Complete the vent connection required for your instal-
lation type.
•
Relocate plate for Outside Air. (Required for Mobile
Home Installation)
page 13
; Assemble Panel Set
and Cast Trim Set or the Basic Panel & Trim Set and
install as one piece.
See page 14.
•
Position unit into fi replace leaving width enough for fi ber-
glass batting to be inserted around face seal.
•
Work unit securely into the fi replace using sheet metal
shims if leveling bolts are needed.
See Figure 12B on
page 12.
•
Remove all labels from glass prior to building fi rst fi re.
•
Ensure that plated surfaces are cleaned prior to build-
ing fi rst fi re.
See page 20
.
•
Read Operation Instructions found on
pages 18 and
19.