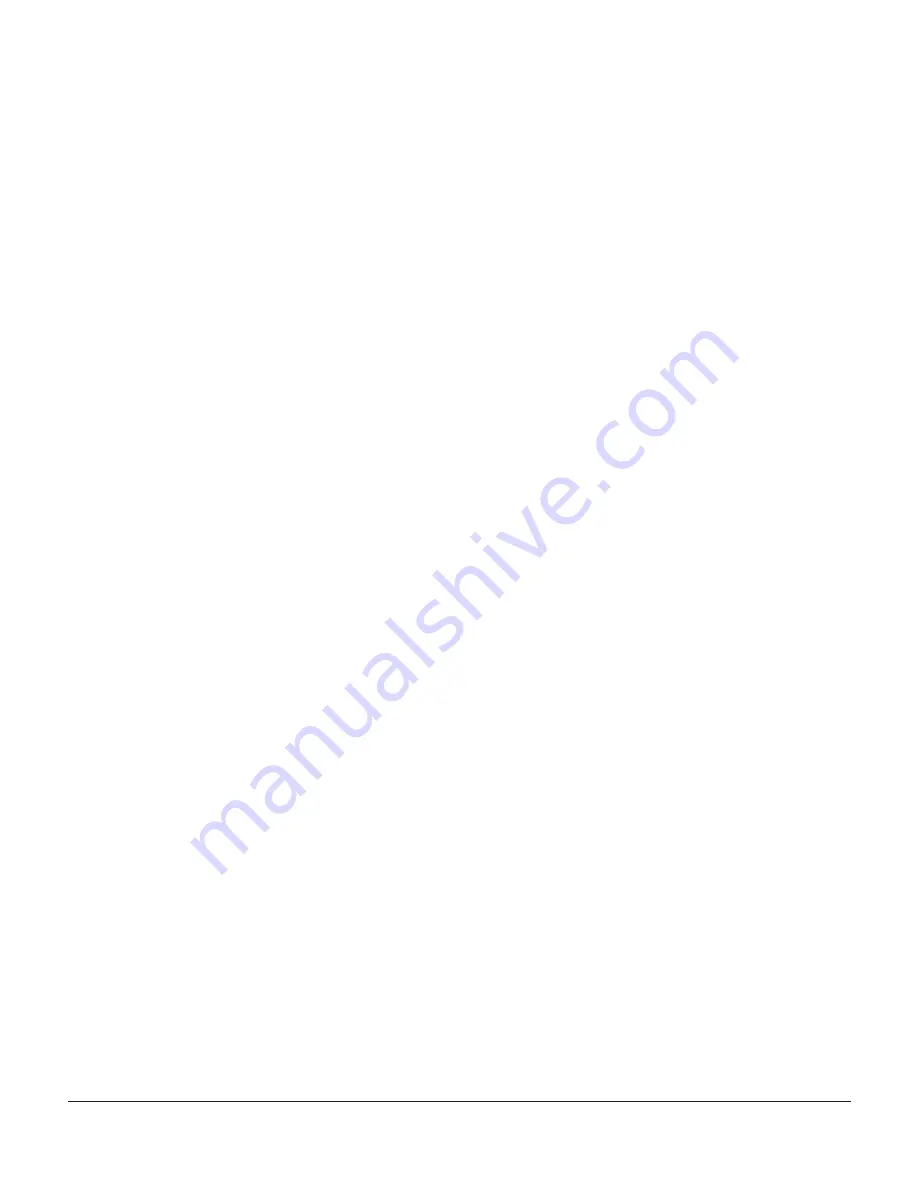
AS40 Conveyors | Installation & Maintenance Instructions
33
u
Return Policy
If, for any reason, an item needs to be returned to QC Conveyors or an in-house order needs to be canceled or revised, the Purchaser is required to adhere to the following
series of steps to ensure that the return or cancellation is handled in the proper manner.
>
Promptly call QC Conveyors Customer Service at (513) 753-6000 and request a Returned Goods Authorization. At this time, you will be asked to answer pertinent
questions relating to the returned items. We ask that you have the following information ready:
(A) Name of distributor (if applicable) through which item(s) were purchased.
(B) Name of the Customer and/or end user of the item(s).
(C) Any/all purchase order numbers related to the item(s) in question.
(D) Phone numbers and names of contacts involved in the return (if it becomes necessary that they be contacted later).
(E) Complete part numbers of all items involved in the return.
(F) Complete description as to the reason for the return and the actions that need to be taken. (If the item is to be replaced, a new purchase
order number must be supplied by the Purchaser along with complete shipping and billing instructions. These replacements will be treated as
separate orders by QC Conveyors and evaluated for possible credit only after returned items are received and evaluated.
>
After the call is made to QC Conveyors, we will process your RGA and you will be e-mailed the RGA number to use for returning the item(s). RGA numbers will not be
given verbally over the phone.
>
Upon receipt of your RGA, you are required to return the item(s) within 30 days of receipt of authorization. After 30 days, the Return Authorization will be void if
item(s) are not received by QC Conveyors. All shipping charges and freight insurance charges of returned goods will be the responsibility of the Purchaser.
>
The RGA number must be clearly marked on the outside of all packages. It must also be on any paperwork, packing slips, or delivery receipts. If there is no RGA
number visible on the package, the package may be refused and sent back at the Purchaser’s expense.
>
After receipt of returned goods, QC Conveyors will evaluate the item(s) for credit and take the appropriate action. Standard items that are returned in new, resalable
condition will be credited for the amount of the purchase less 20%. Full credit will only be issued on items that are considered to be defective at the time of ship-
ment from QC Conveyors and are evaluated to be under warranty. Please allow 30 days for credits to be issued.
u
Order Cancellation / Revision Policy
If it becomes necessary to cancel or revise an order prior to the order being shipped, QC Conveyors reserves the right to evaluate each order that is to be canceled or
revised and determine if any charges are applicable. A 20% restocking charge will apply if an order is assembled and ready to ship prior to its cancellation or revision and
the order is totally comprised of standard stock items. If the order contains other than stock items, an evaluation will be made based on the status of the order. Additional
charges will be included with the 20% restocking charge if any of the following conditions are met:
(A) The order contains any items that are considered to be non-stock items and these items have already been produced by QC Conveyors or one
of its suppliers.
(B) The order contains any items that require special handling or assembly and these processes have been completed.
(C) The Customer has specified that they will pick-up an order from QC Conveyors’ facility by a predetermined time and that time frame has
expired. In this case, QC Conveyors will make an attempt to notify the Customer. If this cannot be accomplished in a reasonable time, the order
will be disassembled and the Customer will be charged a restocking fee and any additional charges based on the orders contents as explained
herein.