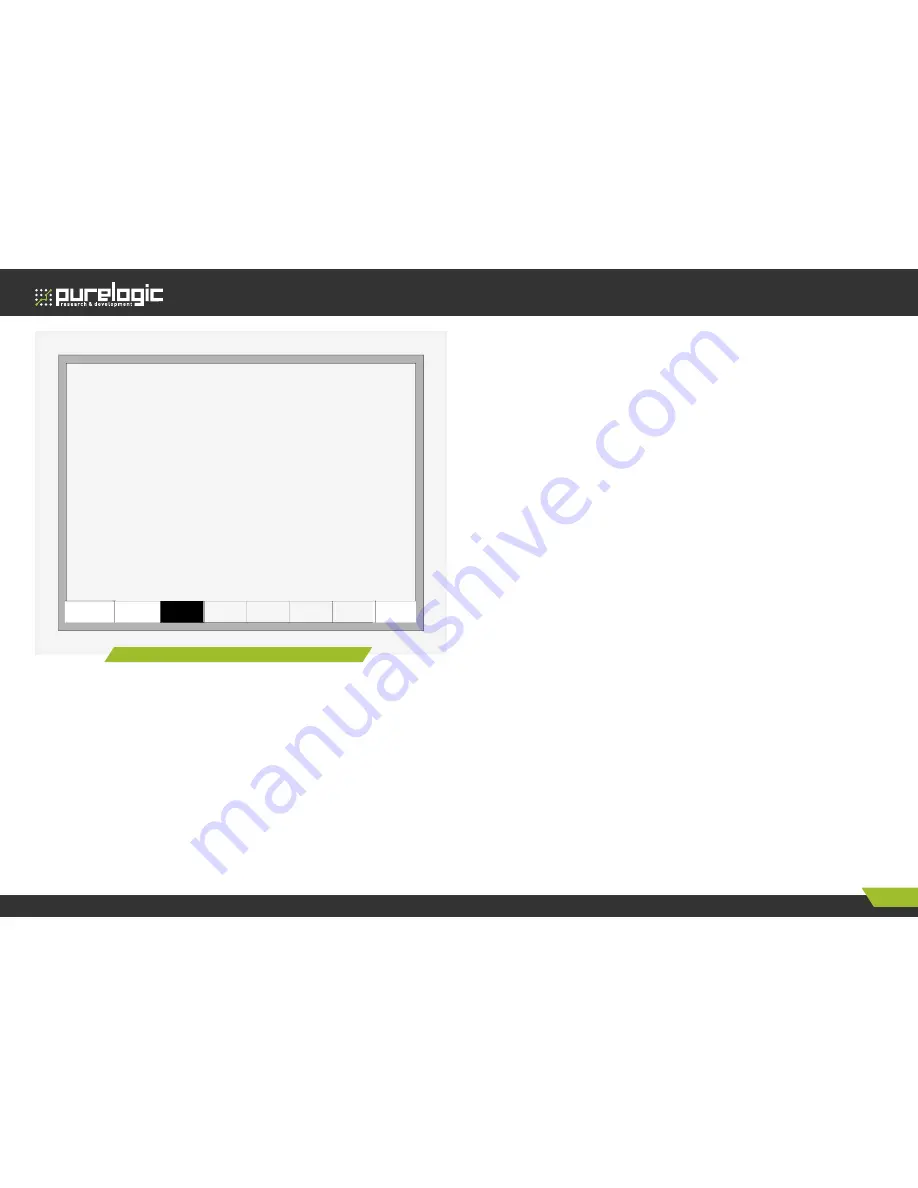
HYD-2100.
CNC Plasma&Flame Cutting Control System
Edition of 28.07.2015
33
www.purelogic.ru
8 (800) 555 63 74
F1 Common
F2 Flame
F3 Plasma
F4 Powder
F5 System
F6 Import F7 Export
F8 Save
s
0
0
.
0
e
m
i
t
c
r
A
s
0
0
.
0
e
m
i
t
e
c
r
e
i
P
s
0
0
.
0
e
m
i
t
p
u
h
c
r
o
T
s
0
0
.
0
e
m
i
t
k
c
e
h
c
g
n
i
c
r
A
s
0
0
.
0
e
m
i
t
k
c
e
h
c
n
o
i
t
i
s
o
P
s
0
0
.
0
e
m
i
t
p
u
n
o
i
t
i
s
o
P
%
m
p
m
m
0
0
.
0
c
r
a
e
s
o
l
C
m
m
0
0
.
0
c
r
A
e
s
o
l
c
o
t
e
c
n
a
t
s
i
D
s
0
0
.
0
y
a
l
e
d
c
r
a
e
s
o
L
>
-
<
o
N
e
l
b
a
n
e
c
r
a
h
c
t
a
W
F1 Common
F2 Flame
F3 Plasma
F4 Powder
F5 System
F6 Import F7 Export
F8 Save
s
0
0
.
0
e
m
i
t
c
r
A
s
0
0
.
0
e
m
i
t
e
c
r
e
i
P
s
0
0
.
0
e
m
i
t
p
u
h
c
r
o
T
s
0
0
.
0
e
m
i
t
k
c
e
h
c
g
n
i
c
r
A
s
0
0
.
0
e
m
i
t
k
c
e
h
c
n
o
i
t
i
s
o
P
s
0
0
.
0
e
m
i
t
p
u
n
o
i
t
i
s
o
P
%
m
p
m
m
0
0
.
0
c
r
a
e
s
o
l
C
m
m
0
0
.
0
c
r
A
e
s
o
l
c
o
t
e
c
n
a
t
s
i
D
s
0
0
.
0
y
a
l
e
d
c
r
a
e
s
o
L
>
-
<
o
N
e
l
b
a
n
e
c
r
a
h
c
t
a
W
Figure 41. Plasma parameters
• Arc time: Before the arc starting, the system time to wait. At this
point, all output I /O are turned off. Enter any positive number, unit is s.
• Pierce time: Perforation time. Enter any positive number, unit is s.
• Torch Up Time: When arc press is turned off, the time for the torch to
lift up. Enter any positive number, unit is s.
• Arcing Check Time: Enter any positive number, unit is s. If not
detected any feedback signal of success arc starting within the
detection time, the system prompts an error message and terminates
the current work of cutting, according memory breakpoints to
withdraw from the program.
• Position check Time: Enter any positive number, unit is s. Delay time
of the success of position check.
• Position up Time: Enter any positive number, unit is s. Before
positioning check, the time for the torch to lift up.
• Close arc: In setting the rate of X%, open the output port, close the
arc press signal, to prevent the steel melting under low-speed cutting
tip due to temperature is too high.
• Distance to close arc: in the minimum distance of the cutting line of
the initial segment or end segment, close the arc voltage increases.
• Lose arc delay: detect the delay time of the feedback of the broken
arc, if there’s still no arc voltage input, the situation is considered to be
broken arc. This parameter can effectively avoid the arc broken alert
because of the sensitivity of the broken arc detection in the cutting
methods with lead, this guarantees the continuousness of the
cutting and avoid the interrupt of frequent alert .
• Watch arc enable: Real-time detection of arc voltage signal in cutting process.
If setting «yes», in the cutting process, the system detects he real-time arc voltage feedback signal. If do not detect the signal, the system terminates the
current work of cutting, according memory breakpoints to withdraw from the program.
If installing a «No», then in the cutting process does not detect arc voltage feedback signal.
POWDER PARAMETERS
As shown in the Fig. 42, these are Powder Parameters, which are related with the precision of transmission shaft of the machine.