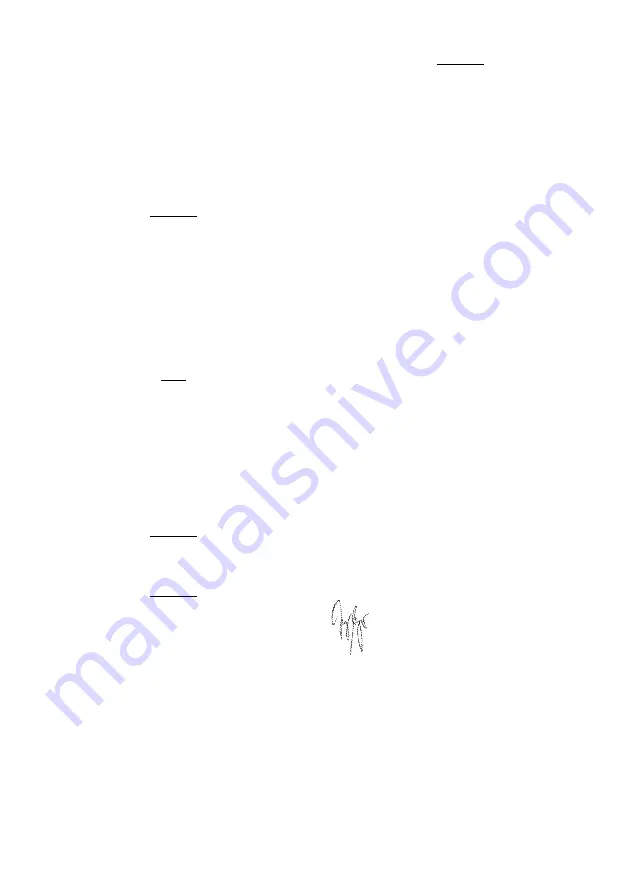
- 21 -
1. Detach the three-jaw chuck and attach the four-jaw chuck.
2. Open the four jaws, clean the contact faces and clamp the
work piece lightly according to visual estimation.
3. Move the support and turning tool onto the plane surface of
the work piece.
4. Turn the chuck by hand to establish symmetrical deviations.
5. Adjust by opening one of the jaws and re-set the opposite
jaw accordingly.
6. Tighten all four jaws evenly, alternating crosswise.
Important
In the normal clamping jaw position, only work pieces with an
edge length of max. 55 mm can be clamped. The maximum
length is 100 mm in the reverse position. Larger work pieces
are not securely held. Danger of accident.
4-jaw chuck (concentrically clamping)
Jaws not individually adjustable (automatic centring). Chuck Ø
100 mm. Max. clamping range 83 mm. Larger work pieces are
not securely held. Danger of accident.
Collet chuck attachment and collet chucks
Note:
The collet chuck unit is especially suitable for processing
round parts with great precision. The concentricity is consi-
derably greater than when working with a jaw chuck.
1. Remove three fastening screws from the three-jaw chuck
and remove chuck.
2. Thoroughly clean the fit for the collet chuck mount
2
(Fig. 22) and the fit in the main spindle
1
.
3. Attach the collet chuck mount
2
using four fastening
screws
3
.
Important
Always use the correct collet chuck to suit the work
piece. Chucks with an oversized diameter are destroyed.
4. Insert the collet chuck
6
and loosely attach the union nut
5
.
Important
Never tighten the union nut when there is no work piece
inserted. Remove the pins 4 for tightening the union nut 5
immediately after tightening.
5. Insert the appropriate work piece in the collet chuck and
tighten the union nut
5
using the tool pins
4
.
Fixed steady rest
The steady rest is particularly suitable for hollowing out long
work pieces with diameters up to 50 mm.
1. Release the fastening screw
4
(Fig. 23) and position retai-
ning plate
3
laterally.
2. Place the steady rest on the bed guide and set to the desi-
red position.
3. Swivel the retaining plate
3
parallel to the steady rest base
and tighten fastening screw
4
.
4. Release all clamp screws
1
and drive the individual retai-
ning jaws
2
onto the workpiece.
Important
The jaws 2 must only touch the work piece and must not
clamp it. Otherwise there is a risk of the work piece
surface becoming scratched and the motor becoming
overloaded.
If the work piece is not round and smooth at the support
point, it must first be turned round. Lubricate the jaws and
work piece regularly when turning.
5. Check that the work piece is positioned in the steady rest
free of play and re-tighten clamp screws
1
.
Travelling steady rest
Installation identical to the fixed steady rest, but this steady
rest is attached to the support (Fig. 24).
Faceplate with clamps
This is installed in place of the lathe chuck. Ideal for clamping
larger and asymmetrical workpieces. Ø 150 mm. 2 continuous
T-grooves. incl. clamps.
EC Declaration of Conformity
Name and address:
PROXXON S.A.
6-10, Härebierg
L-6868 Wecker
Product designation: PD 400
Article No.:
24400
In sole responsibility, we declare that this product conforms to
the following directives and normative documents:
EU EMC Directive 2004/108/EC
DIN EN 55014-1 / 02.2010
DIN EN 55014-2 / 06.2009
DIN EN 61000-3-2 / 06.2011
DIN EN 61000-3-3 / 06.2009
EU Machinery Directive 2006/42/EC
DIN EN 61029-1 / 01.2010
Date: 19.04.2012
Dipl.-Ing. Jörg Wagner
PROXXON S.A.
Machine Safety Department
The CE document authorized agent is identical with the
signatory.
Summary of Contents for PD 400
Page 1: ...D GB F I E NL DK S CZ TR PL RUSS Manual PD 400...
Page 102: ...102 19 14 22 16 15 17 18 18 20 21 1 13 16 15 17 20 Ersatzteilliste Baugruppe 00 Wechselr der...
Page 108: ...108 Ersatzteilliste Baugruppe 03 Support...
Page 111: ...111 Notizen...
Page 112: ...Art Nr 24 400 99 PR 704712701 5 J...