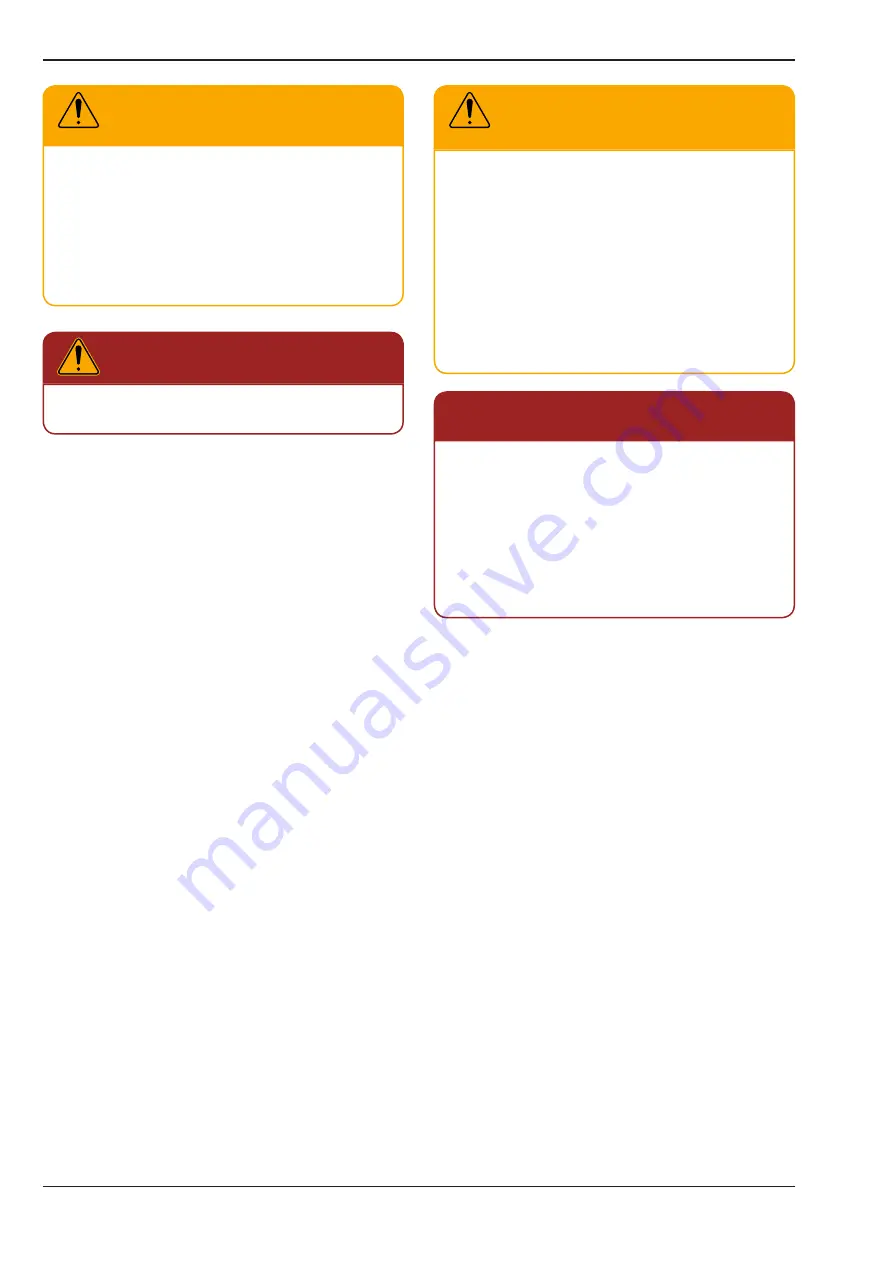
Rozdział 4
Terms of use
4.12
PRONAR T185/1
TRAILER DISCONNECTING
•
Place the trailer on a hard and flat
surface.
• Lower the support to parking position.
• If the trailer is equipped with a te-
lescopic support, lower the HITCH
drawbar.
• Switch off the tractor engine and
remove the ignition key, secure the
tractor with the parking brake.
• Immobilize the trailer with parking
brake.
• Place blocking wedges under one
wheel of the trailer, one in the rear
and the other in front of the wheel.
• Disconnect all cables in turn. Secure
the ends by fitting the rubber caps on
the hydraulic connectors.
• Place the cables on the cable support
(1) - Figure (4.12).
• Release the drawbar eye, start the
tractor and drive away with the tractor.
H.3.4.622.02.1.EN
CAUTION
In the event of a longer standstill of the trailer, it may
turn out that the air pressure in the pneumatic bra-
king system is insufficient to release the brake sho-
es. In this case, after starting the tractor and the air
compressor, wait until the air in the pneumatic tank
is topped up.
DANGER
The use of defective trailers is forbidden.
CAUTION
When disconnecting the pneumatic cables of a dual
cable, first disconnect the cable marked red and only
then the cable marked yellow.
It is forbidden to park the trailer with the container
loaded, disconnected from the tractor and supported
by the support.
It is forbidden to disconnect the trailer from the tractor
if the swing frame or middle frame are not folded and
when the suspension lock cylinders are extended.
Take particular care when disconnecting the trailer
from the tractor.
Ensure good visibility. Unless it is necessary, do not
stay between the trailer and the tractor.
Before disconnecting cables and drawbar eye, close
tractor cab and secure it against access by unautho-
rized persons. The tractor engine must be turned off..
Summary of Contents for T185/1
Page 2: ......
Page 3: ...INTRODUCTION ...
Page 10: ...Introduction 8 PRONAR T185 1 ...
Page 11: ......
Page 12: ......
Page 15: ......
Page 16: ......
Page 17: ...GENERAL INFORMATION CHAPTER 1 ...
Page 31: ...SAFETY OF USE CHAPTER 2 ...
Page 50: ...Chapter 2 Safety of use 2 20 PRONAR T185 1 ...
Page 51: ...CONSTRUCTION AND OPERATION CHAPTER 3 ...
Page 66: ...Rozdział 3 Construction and operation 3 16 PRONAR T185 1 ...
Page 67: ...TERMS OF USE CHAPTER 4 ...
Page 102: ...Rozdział 4 Terms of use 4 36 PRONAR T185 1 ...
Page 103: ...PERIODIC INSPECTIONS CHAPTER 5 ...
Page 135: ...TECHNICAL SERVICE CHAPTER 6 ...
Page 152: ...Rozdział 6 Technical service 6 18 PRONAR T185 1 ...
Page 155: ......
Page 156: ......