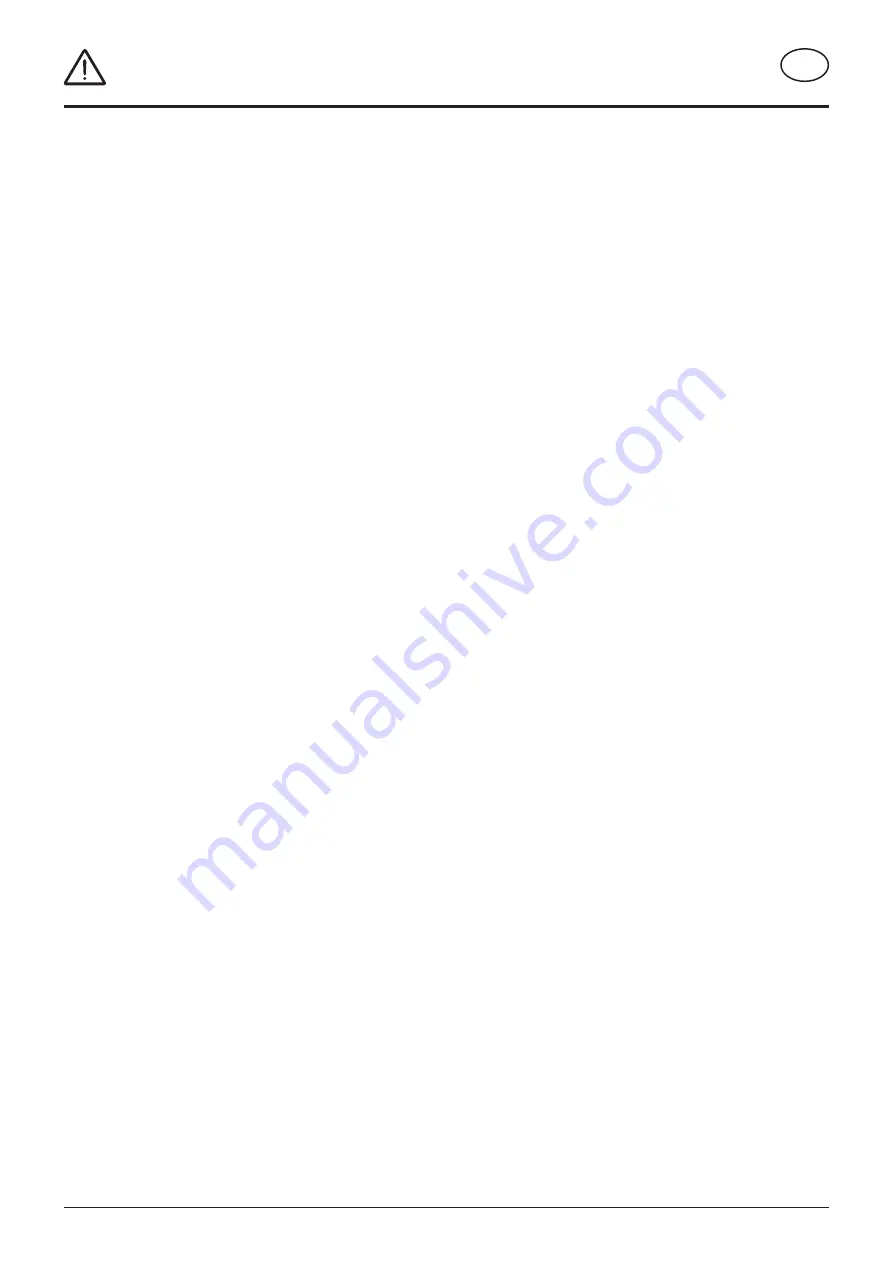
- 45 -
1200_GB-ANHANGA1_SICHERHEIT_SCHWADKREISEL
SUPPLEMENT - A
GB
j. Never turn p.t.o. on when motor is turned off!
k. When working with the p.t.o., ensure nobody is in the
danger areas where the rotating p.t.o. or cardan shaft
are located!
l. Always turn p.t.o. off when angles become too great
or it is no longer required!
m. Be alert! After turning the p.t.o. off, danger still exists
from on-running centrifugal mass! During this time
keep away from the machine! Wait until it comes to a
complete standstill before starting any work!
n. Cleaning, lubricating or adjusting the p.t.o.-driven
machine or cardan shaft should be carried out only
when the p.t.o. and motor are turned off, and ignition
key is removed!
o. Place uncoupled cardan shaft in the holder provided
or suspend it using chains!
p. After uncoupling the cardan shaft, put protective cover
over the p.t.o. stub!
q. Repair any damages before operating the machine!
5. Hydraulic system
a. The hydraulic system is always under high pressure!
Ensure the specified hydraulic hose connections are
used when connecting hydraulic cylinders and motors!
b. When connecting hydraulic hoses to the tractor’s
hydraulics, ensure that both the tractor’s and the
machine’s hydraulics are depressurized!
c. For hydraulic function connections between tractor
and machine, coupling sleeves and sockets should
be labelled so that operating errors can be eliminated!
If function connections are reversed (e.g. lifting/lowering)
– Risk of accidents!
d. Check hydraulic hose lines regularly and exchange
them when damaged and aged! The new hydraulic
hose lines must meet the technical demands of the
machine’s manufacturer!
e. When looking for leaks, use suitable means that protect
from injury!
f. Fluids (hydraulic fluid) escaping under high pressure
can penetrate the skin and cause serious injury! Call
a doctor immediately if injured! Danger of infection!
g. Before working on the hydraulics, lower the machine,
depressurize the hydraulics and turn the motor off!
6. Tyres
a. When working on tyres ensure the machine is stabled
securely and guaranteed against rolling (wheel chocks)!
b. Fitting wheels and tyres requires adequate knowledge
and proper tools!
c. Repairs to tyres and wheels must only be carried out
by specialists and with the appropriate tools!
d. Check air pressure regularly! Be aware of the specified
air pressure!
7. Maintenance
a. In principle, any overhaul, maintenance and cleaning
work as well as eliminating any function faults should
be carried out with the drive turned off, motor at a
standstill and ignition key removed!
b. Wait until machine has completely stopped! Repairs
to prestressed energy stores (springs, pressure
accumulators, etc.) requires adequate knowledge and
proper tools, and must only be carried out in specialist
workshops!
c. Check nuts and bolts regularly for tightness and
retighten if necessary!
d. When working on a raised machine always ensure
security using appropriate supports!
e. When switching work tools, use suitable tools and
gloves!
f. Dispose of oil, grease and filters properly! Always
disconnect the power supply before working on the
electrical system!
g. If safety equipment is subject to wear and tear, check
regularly and replace in time!
h. Any exchange parts must, at least, meet the machine
manufacturer’s established technical demands! This is
achieved by using genuine parts, for example! When
carrying out any electrical welding on the tractor and
attached machines, clamp the cable at the generator
and on the battery!