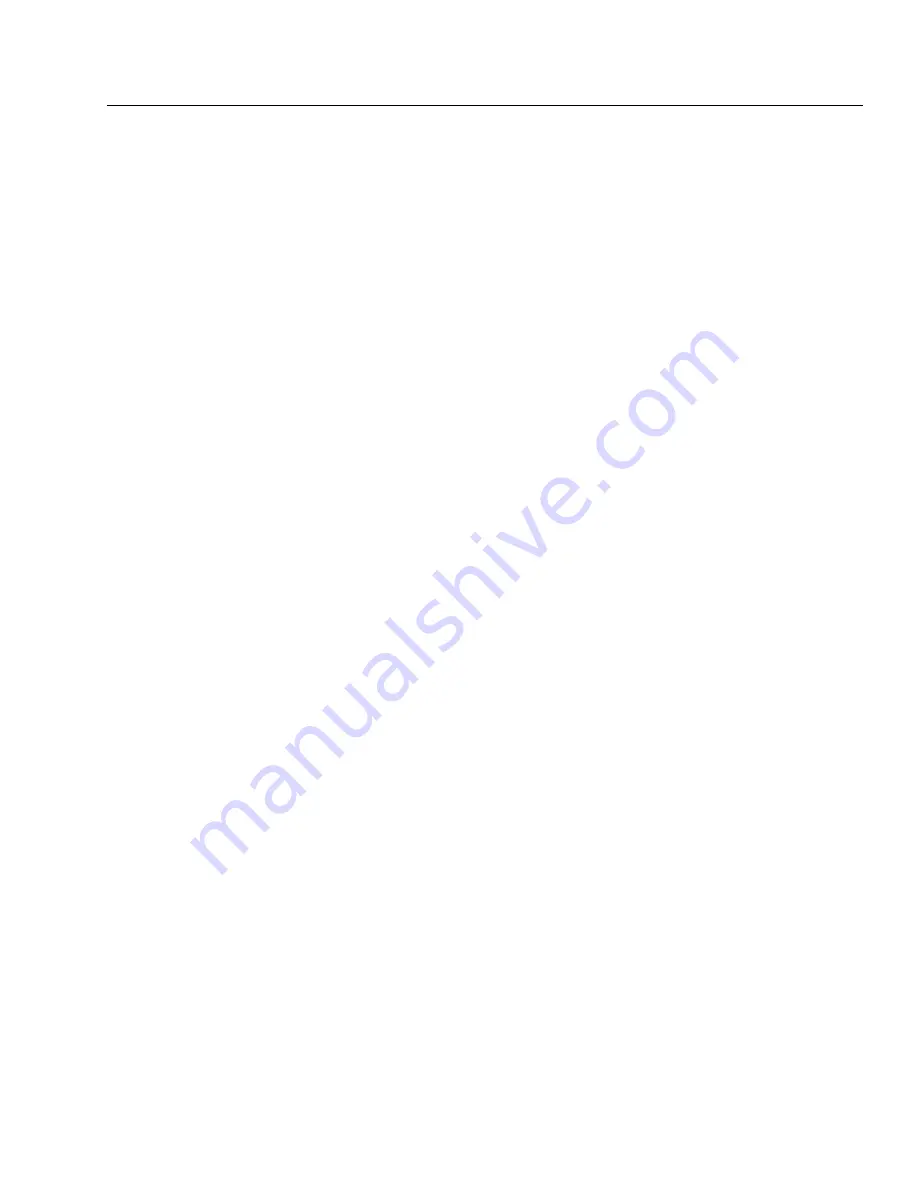
CONTROL VALVES.
After 100 hours of engine operation, the valve poppet and internal lining of the control valve can become
coated with a film of dried oil causing the valve to stick. To determine if valve poppet is sticking, perform
electrical test. If solenoid checks satisfactory, remove valve poppet and clean control valve bore and poppet. To
clean:
1. Remove nacelle hatch cover to gain access to the valve.
2. Remove electrical connector. Unscrew solenoid.
— CAUTION —
DO NOT LOSE STEEL HEX ACTUATOR PIN.
3. Remove valve poppet. It may be necessary to apply slim nose pliers to pin projection to pull poppet from
valve.
4. Thoroughly clean valve bore and poppet with commercial hydrocarbon type solvent.
5. Reassemble valve and solenoid.
TIMER.
No field maintenance is recommended. For repair or replacement, contact your B. F. Goodrich dealer or
distributor.
PNEUMATIC BOOTS.
REMOVAL OF BOOTS.
The removal of deicer boots should be done in a well ventilated area to avoid difficulty from the fumes of the
solvents. Materials required to remove the boots are: Turco 388 dried cement remover, Kelite 21. and a pressure
handle squirt can. Proceed as follows:
— Note —
Disconnect line fittings from boot fittings
1. Starting at one corner of the upper trailing edge of the deicer, apply a minimum amount of solvent to the
seam line while tension is applied to peel back the corner of the deicer.
2. Using a pressure handle squirt can filled with solvent, separate the deicer boot from the surface for a
distance of 4 inches an the way along the upper trailing edge.
3. The area between the deicer and the wing which has now been separated will act as a reservoir for the
solvent, therefore, the deicer can be pulled down towards the leading edge with a uniform tension.
PA - 4 4 - 1 8 0 / 1 8 0 T
AIRPLANE MAINTENANCE MANUAL
3 0 - 1 3 - 0 5
Page 30-09
Revised: May 15, 1989
2D13
PIPER AIRCRAFT
Summary of Contents for SEMINOLE PA-44-180
Page 38: ...CHAPTER DIMENSIONS AND AREAS 1B14...
Page 49: ...CHAPTER LIFTING AND SHORING 1C1...
Page 53: ...CHAPTER LEVELING AND WEIGHING 1C5...
Page 58: ...CHAPTER TOWING AND TAXIING 1C10...
Page 62: ...CHAPTER PARKING AND MOORING 1C14...
Page 65: ...CHAPTER REQUIRED PLACARDS 1C17...
Page 70: ...CHAPTER SERVICING 1C22...
Page 98: ...CHAPTER STANDARD PRACTICES AIRFRAME 1E2...
Page 108: ...CHAPTER ENVIRONMENTAL SYSTEM 1E12...
Page 189: ...CHAPTER AUTOFLIGHT 1H21...
Page 192: ...CHAPTER COMMUNICATIONS 1H24...
Page 202: ...CHAPTER ELECTRICAL POWER 1I10...
Page 228: ...CHAPTER EQUIPMENT FURNISHINGS 1J12...
Page 233: ...CHAPTER FIRE PROTECTION 1J17...
Page 238: ...CHAPTER FLIGHT CONTROLS 1J24...
Page 304: ...2A18 CHAPTER FUEL...
Page 325: ...2B17 CHAPTER HYDRAULIC POWER...
Page 357: ...2D1 CHAPTER ICE AND RAIN PROTECTION...
Page 414: ...CHAPTER LANDING GEAR 2F13...
Page 479: ...2I6 CHAPTER LIGHTS...
Page 488: ...2I16 CHAPTER NAVIGATION AND PITOT STATIC...
Page 503: ...2J7 CHAPTER OXYGEN...
Page 524: ...2K6 CHAPTER VACUUM...
Page 535: ...2K19 CHAPTER ELECTRICAL ELECTRONIC PANELS AND MULTIPURPOSE PARTS...
Page 546: ...INTENTIONALLY LEFT BLANK PA 44 180 180T AIRPLANE MAINTENANCE MANUAL 2L6 PIPER AIRCRAFT...
Page 547: ...2L7 CHAPTER STRUCTURES...
Page 582: ...CHAPTER DOORS 3A18...
Page 593: ...CHAPTER STABILIZERS 3B8...
Page 604: ...CHAPTER WINDOWS 3B22...
Page 611: ...CHAPTER WINGS 3C10...
Page 624: ...CHAPTER PROPELLER 3D1...
Page 643: ...CHAPTER POWER PLANT 3D21...
Page 667: ...CHAPTER ENGINE FUEL SYSTEM 3F1...
Page 681: ...CHAPTER IGNITION 3F16...
Page 712: ...CHAPTER ENGINE INDICATING 3H1...
Page 730: ...CHAPTER EXHAUST 3H19...
Page 734: ...CHAPTER OIL 3I1...
Page 743: ...CHAPTER STARTING 3I11...
Page 755: ...CHAPTER TURBINES 3J1...