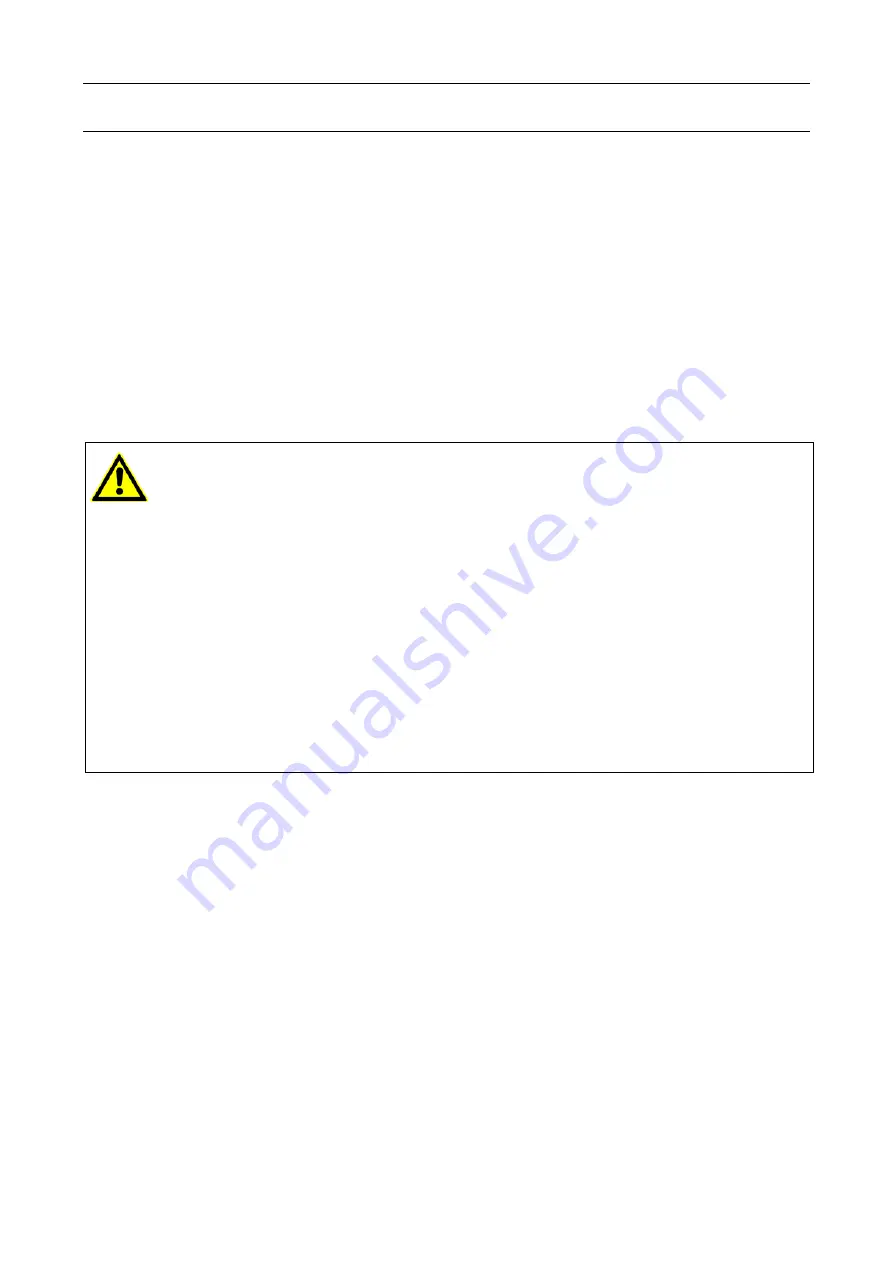
phytron
6.3 Motor Cables
We recommend to wire the stepper motor with a 5-lead cable with shielding mesh. For
optimum electromagnetic compatibility (EMC), the cable should not be interrupted by
additional connectors or screw terminals.
Recommended minimum cable cross section:
0.2 mm²
(0.1 mm² per Ampere motor current)
The protective earth wire (green/yellow) of the motor cable should be connected to the
earthing screw near the CLD
+
motor connector. At the other motor cable end, the
green/yellow wire should be connected to the motor's earthing screw.
The phase currents are leaded outside through a motor lead filter to damp the logic’s high
frequency noise signals. So the noise emission on the motor cables is nearly neglectable.
For best electromagnetic compatibility (EMC) , you must connect the shielding
mesh to the CLD
+
housing. Use the cable clamps at the front side. Free cable
ends must be as free as possible.
The shielding mesh must also be connected on a large surface to the motor
housing. Use EMC-type conduit fittings. All parts of the motor must be
conductively connected with each other.
In case of motors without adapted conduit fittings the cable shielding must be
connected as near to the motor as possible and has to be applied to PE.
Important:
Motor leads not used should be insulated separately
(important if using wiring scheme 3 or 4)!
If the motor is connected in the required way, the fault-free operation is assured according
to EN 61000-6-1/2.
The manufacturer of the equipment/machine is responsible for the adherence to limit
values, required by the EMC legislation.
23
MA 2112-A002 GB
Summary of Contents for 10010115
Page 1: ...Manual 2112 A002 GB CLD Linear Power Stage For Stepper Motor with Plain Text Display...
Page 2: ......
Page 10: ...Manual CLD 1 4 Schematic Diagram Fig 3 Schematic diagram CLD MA 2112 A002 GB 8...
Page 19: ...phytron Fig 5 Mountaing kits 17 MA 2112 A002 GB...
Page 33: ...phytron 8 The Menu Fig 15 Structogram of the menu 31 MA 2112 A002 GB...
Page 49: ...phytron Appendix C Declarations of Conformity 47 MA 2112 A002 GB...
Page 50: ...Manual CLD MA 2112 A002 GB 48...
Page 53: ......
Page 54: ......
Page 55: ......