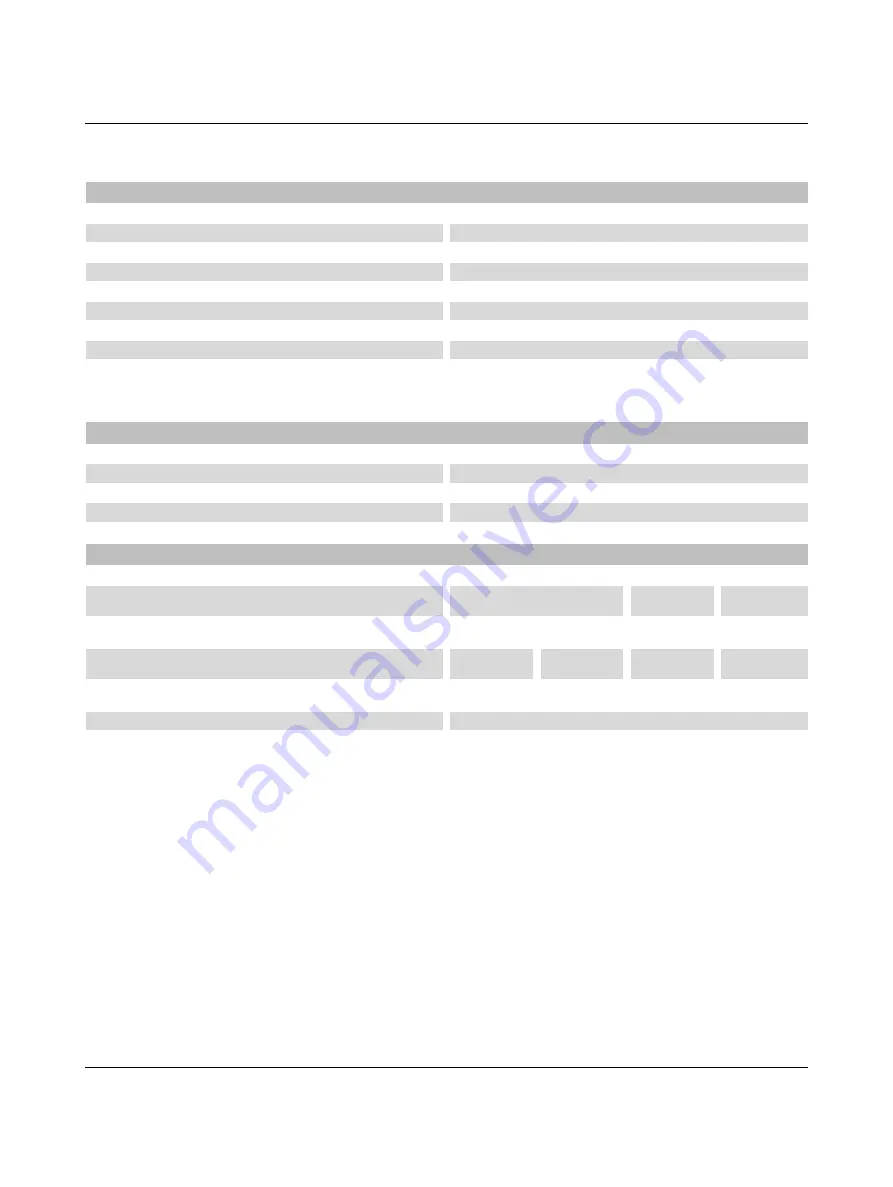
2338_en_O
PHOENIX CONTACT
107
D 2.2
NLC-055… base unit
General
2700453
2700464
2700486
2700487
Dimensions (H x W x D)
103 x 80 x 60 mm
Weight
178 g
262 g
248 g
150 g
Degree of protection
IP20
Class of protection
Class III, EN 61131-2, IEC 61131-2
Connection method
Screw terminal, 0.2 - 2.5 mm², 12-24 AWG, 0.5-0.6 Nm
Operating temperature range
*
-25…60°C
-25…60°C
Storage temperature range
-25…85°C
Humidity (maximum) @ 25°C
90%
*
Temperature range of 0... 50°C with Operator Panel installed
System data
2700453
2700464
2700486
2700487
Number of expansion modules
3
Number of communication expansion modules
1
Number of base unit option modules
2
Supply voltages
2700453
2700464
2700486
2700487
Base power (nominal)
24 V DC
12 V DC
100…
240 V AC
Base power permissible range (ripple included)
19.2…30 V DC
9…15 V DC
100…
240 V AC
Typical current consumption
100 mA
150 mA
250 mA
50 mA
@ 230 V AC
Maximum current consumption
250 mA
250 mA
400 mA
70 mA
@ 110 V AC
Protection
Reverse polarity
Summary of Contents for Nanoline NLC-035-024D-04I-02QRD-05A
Page 1: ...User manual Installing and using Nanoline controllers UM EN NLC...
Page 8: ...Nanoline 4 PHOENIX CONTACT 2338_en_O...
Page 38: ...Nanoline 34 PHOENIX CONTACT 2338_en_O...
Page 54: ...Nanoline 50 PHOENIX CONTACT 2338_en_O...
Page 66: ...Nanoline 62 PHOENIX CONTACT 2338_en_O...
Page 94: ...Nanoline 90 PHOENIX CONTACT 2338_en_O...