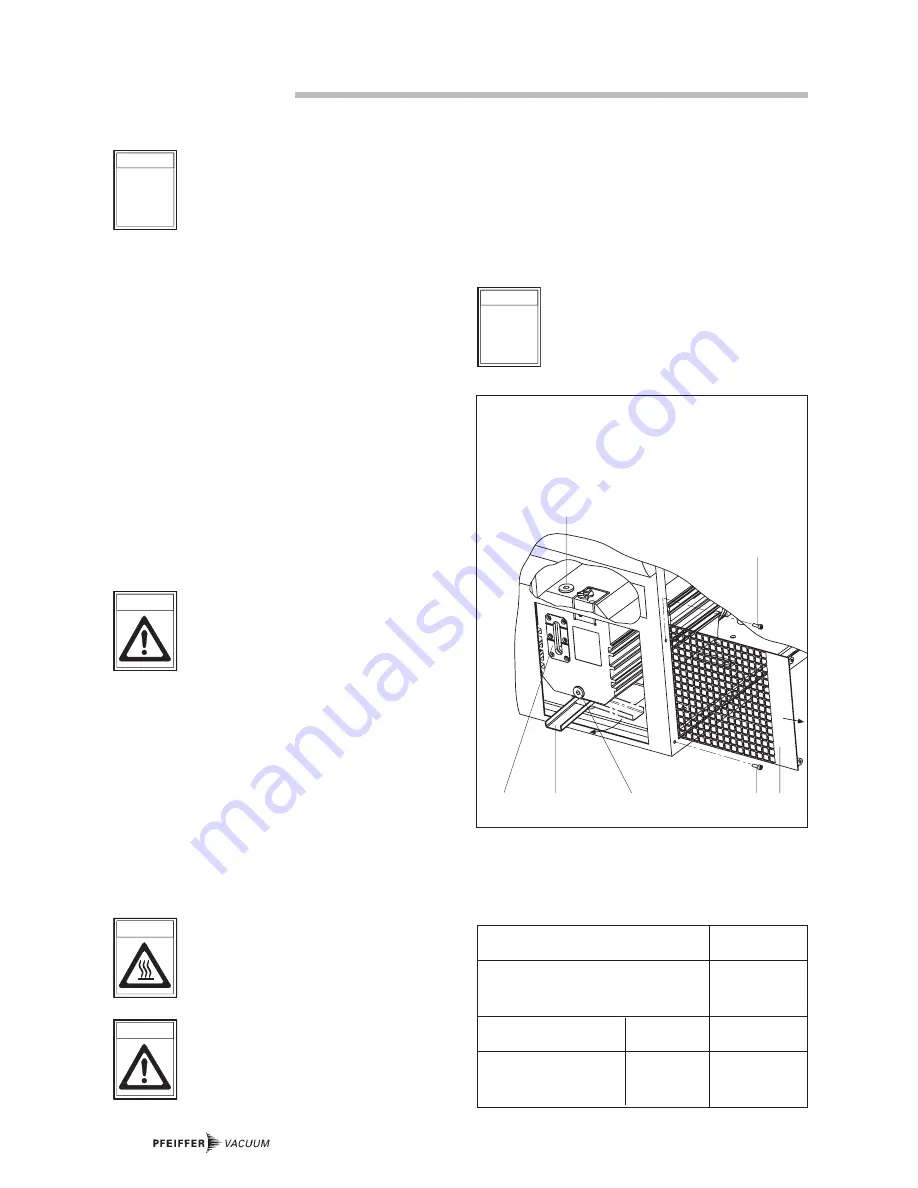
12
6. Maintenance
Maintenance on the individual components of
the pumping station should be carried out in
accordance with the instructions in the
respective sections of the relevant operating
instructions.
6.1. Replacing The Lubricant Reservoir And
The Operating Fluid
– The d
diia
ap
ph
hrra
ag
gm
m p
pu
um
mp
p bearings are lubricated for the whole
of their working life.
– The lubricant reservoir in respect of the ttu
urrb
bo
op
pu
um
mp
p should
be replaced at least once a year. Where extreme
operating conditions or unclean processes are involved,
the replacement interval should be shorter.
Procedure:
➡
Unscrew the four screws from the cover plate and remove.
➡
Unscrew four screws from the turbopump holding plate.
➡
Lift out the turbopump with the holding plate from the
pumping station.
➡
Carry out the change of the lubricant reservoir in
accordance with the turbopump operating instructions.
The Lubricant can contain toxic substances
from the medium pumped. Lubricant must be
disposed of in accordance with the respective
regulations.
Safety instructions data sheet for the lubricant
on request.
– The operating fluid for the rro
otta
arryy vva
an
ne
e vva
ac
cu
uu
um
m p
pu
um
mp
p
should be changed at least once a year.
Procedure:
➡
Unscrew the two screws on the right hand side panel.
Slightly lift up the side panel and remove.
➡
Unscrew two screws 4 and pull out perforated plate 5 to
the right hand side.
➡
Exert slight downward pressure on operating fluid duct 6,
turn 90° and bring into the forward position.
➡
Unscrew operating fluid drain screw 7 and drain operating
fluid via operating fluid duct 6 into a suitable container.
The temperature of the operating fluid can be as
high as 80 °C.
Toxic gases and vapours can escape from the
operating fluid which can be enriched with
substances which represent a hazard to health.
Disposal must be carried out in accordance with
the relevant regulations.
WARNING
WARNING
WARNING
☞
PLEASE NOTE
Lubricant reservoir
on turbomolecular pumps
Order number
TMH/U 071
PM 073 073 -T
TMH/U 261
PM 063 265-T
TMH/U 521
PM 063 265 -T
Operating fluid for rotary
vane vacuum pumps
Pack size
Order number
P3
1 l
PK 001 106 -T
P3
5 l
PK 001 107 -T
P3
20 l
PK 001 108 -T
4 5
7
6
9
4
8
Changing the operating fluid on rotary vane vacuum pumps
4
Screws (2 pieces)
5
Perforated plate
6
Operating fluid duct
7
Operating fluid drain screw
8
Operating fluid filler screw
9
Sight glass
Order numbers for the lubricant reservoir on turbopumps and
operating fluid on rotary vane vacuum pumps
➡
Screw back in operating fluid drain screw 7 taking care
with the O-ring.
➡
Fill in operating fluid as described in Section 4.1. of these
operating instructions.
➡
Re-fit the perforated plate and the side panel.
➡
Check the operating fluid daily where non-stop operations
are involved, otherwise each time the pumping station is
switched on.
Further information regarding changes of
operating fluid can be found in the operating
instructions for the respective rotary vane
vacuum pump.
☞
PLEASE NOTE