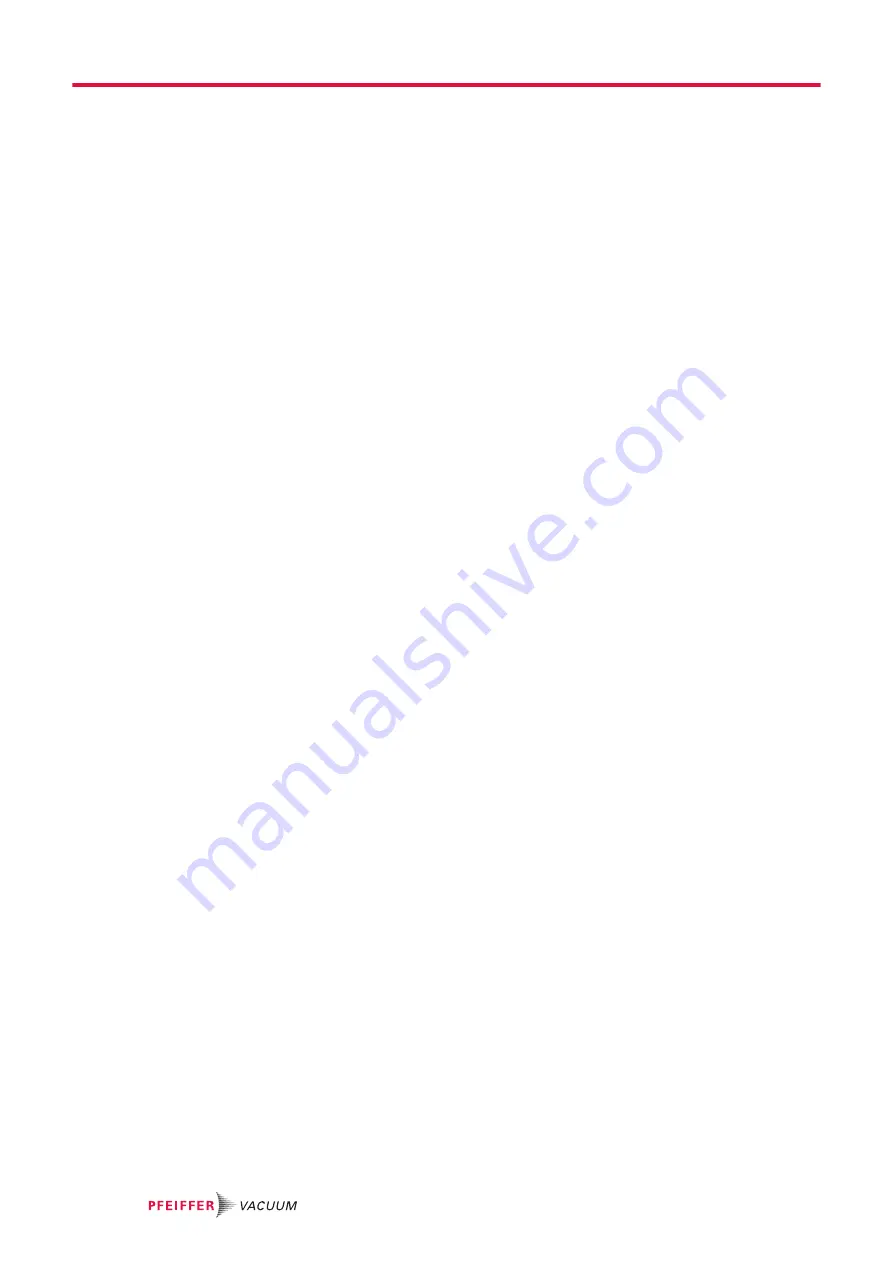
● Pumping of condensing vapors
● Pumping of fluids
● Pumping of dust
● Operation with impermissible high gas throughput
● Operation with impermissible high fore-vacuum pressure
● Operation with excessively high irradiated heat output
● Operation in impermissible high magnetic fields
● Operation in an incorrect gas mode
● Venting with impermissible high venting rates
● Use for pressure generation
● Use in areas with ionizing radiation
● Operation in explosion-hazard areas
● Use in systems in which sporadic loads and vibrations or periodic forces act on the device
● The causing of hazardous operating conditions by a presetting on the electronic drive unit that is
contrary to the process
● Use of accessories or spare parts that are not listed in these instructions
Safety
16/80