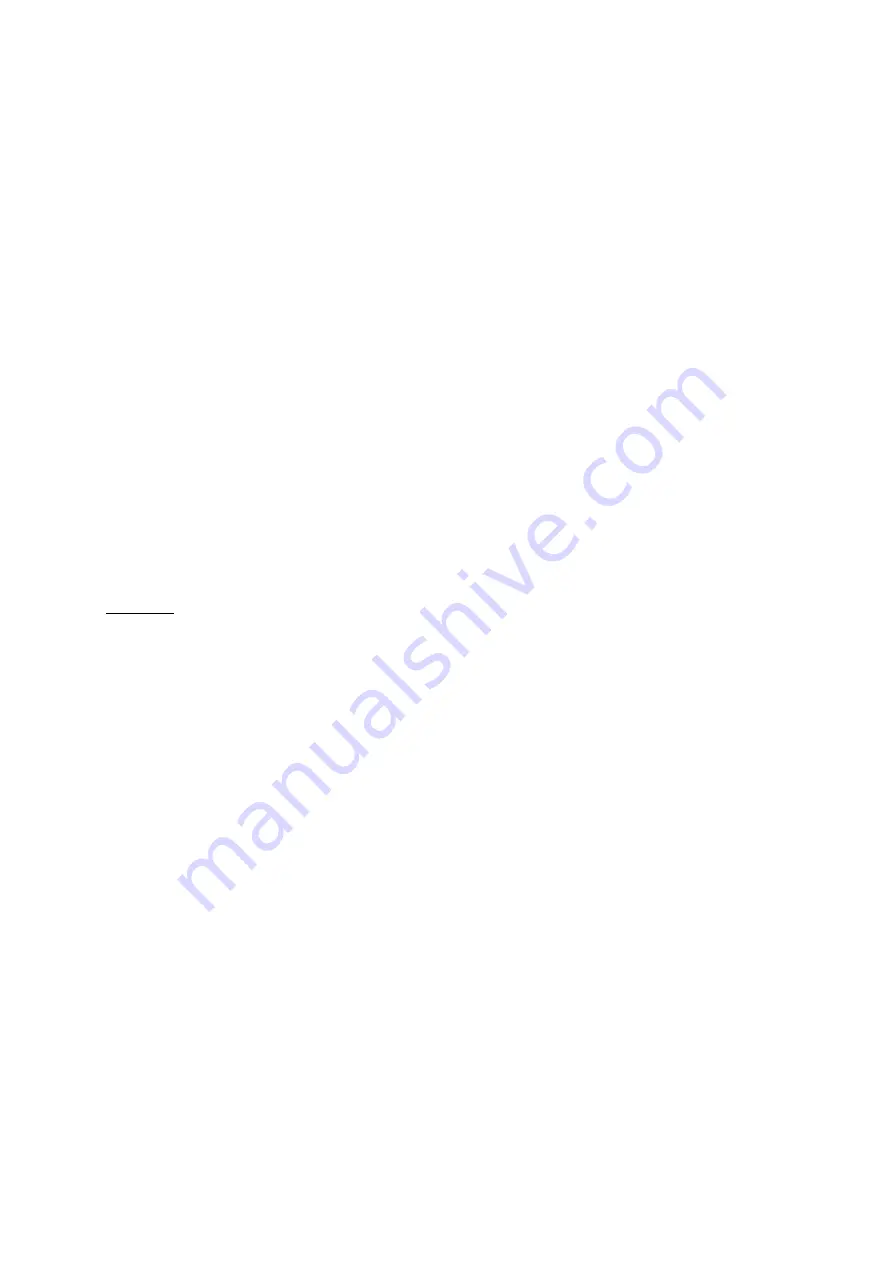
Parker Hannifin S.p.A. - Divisione S.B.C. “SPD” User’s Manual
89
To evaluate the minimum sampling time, use the following formula:
Tc
min
= ( Nr + Nt + 5 ) * 0.12
where: Tc
min
is the minimum sampling time in milliseconds
Nr is the number of SPDs that receive the reference
Nt is the number of SPDs that transmit the feedback
The constant 0.12 is valid for 1 Mbps bus speed
Note 1:
bit 41.15 can be used in “real time mode”; bit 41.15 is set to 1 every synchronism and
multisynchronism message receiving via SBCCAN.
Therefore, it is possible to check the communication status between Master and Slave via
CanBus through a simple pico-PLC program.
The pico-PLC code on the drive be as follows:
…
Ld
41.15
Out
41.5
Rst
41.15
…
If the check of the communication status between Master and Slave via CanBus is
implemented into the drive pico-PLC, the test is executed every 6.144 [ms] (i.e. minimum
execution time of pico-PLC program) or multiples.
Attention: both Pr103 (Status) and Pr102 (Command) must be set through a specific pico-
PLC program into each drive.
Note 2:
the Master can send the new reference data only if at least 400 [µs] passed from the
last synchronism message, or if the response message has already been received.
The typical timing of the SBCCAN in real time mode is shown in the diagram on the next
page: